I have become increasingly fascinated with serpentine curvilinear forms of contemporary woodworking, so naturally I found myself in Jeff Miller’s session on Friday morning. Jeff has delved so deeply into the world of design, integrating the curve into his creations to such a degree that he considers it part of his fundamental lexicon. Even a cursory browsing of his portfolio reveals his exquisite use of curves.
This was a particular pleasure for me as it seems like in previous WIA and similar events every time Jeff was presenting it was opposite either a session I was teaching or some other commitment I needed to fulfill.
In this session Jeff led us through the concepts and practices of creating curved forms that would be nearly impossible to achieve, particularly from an engineering perspective, through any other means than glued up laminations. I especially appreciated his demonstration of creating perfectly matched gluing cauls for these shapes. I have done this myself but his method struck me as being a lot simple and more precise. Basically he creates the exact profile he wants for the curve, then builds a stacked caul by tracing each layer off of the original with a router and a precision trimming/tracing bit. I will definitely by giving than one a try the next time I need to complete some fabrication requiring matched cauls.
My only gripe about this session, and in fact all of the demonstration sessions, was that the lighting in the classroom was abysmal. That is often the case when attending a hands-on demonstration in a conference center which is set up for corporate bull sessions and PowerPoint-only presentations. So, much of what Jeff was showing was not readily visible to me. Fortunately he had a lot of examples to pass around the room. But, my photos of the session stunk.
It was an important reminder for me to make sure I always travel with my own lighting system when demonstrating. That would have been immensely helpful for every one of the sessions I attended all weekend.

You might recall my recent post about Ray Larsen’s piano maker’s workbench, probably with one degree of separation from Studley himself. Ray recently contacted me to let me know he was considering selling the bench to someone who would restore and use it. If you are interested in connecting with Ray about this bench, drop me a note via the “contact” button on this page and I will forward it to him.
I am an entirely disinterested party in this affair, seeking only to match a grand work bench with an enthusiastic new owner.
I am not a morning person, and thanks to the WIA home page hotel reservations we found ourselves staying more than 20 miles away from the conference hotel. Check: lesson learned. Make your own reservations.
This all comes together in that the first session on Day 1 of WIA was one I very much wanted to attend, and in fact I made it only a few minutes late. Mostly that might be due to the facts that 1) it was Friday morning rush hour, that 2) the road signage in greater KC is among the worst I have ever encountered and Google and Mapquest merely compound the problem with incomprehensible directions, and 3) my ambulatory speed was set to 0.1. I think it took more than fifteen minutes for me to get from the parking garage into the exhibit hall, then up a flight of stairs and across the long balcony to the conference room.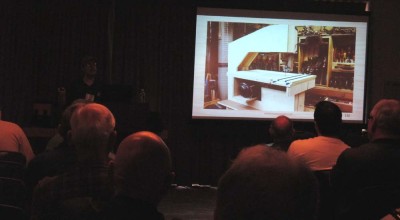
Nevertheless I get to the presentation of James “Stumpy Nubs” Hamilton probably five minutes after he started. The title for the session was something like “Make Your Own Woodworking Machines” and based on the riches of information from his web site I figured it would be a lot of fun. And it was! Two hours of jigs and home made devices was a total gas. Yes, I have been steadily moving towards hand-tool primacy in my own work, but I do have a pretty complete machine capability in The Barn, and to quote hand tool star Vic Tesolin, “Of course I love machines, I’m a guy!”
The Stumpy Nubs session was indeed a trove of motivational treasures. In particular I am prompted to finally build the horizontal drum sander I can use when preparing the yards and yards of veneer strips I produce for executing Roubo-style parquetry. I’ve already thought of a couple of ways I can tweak their design to better suit my own needs. This will please ol’Stump to no end as he probably views his role as evangelist and innovation encourager, taking delight in seeing his ideas taken to new heights. I’ve already got the basic ingredients in-hand: hyper-curiosity, a stash of electric motors and machine parts, and lots of Baltic Birch plywood.
Mrs. Barn and I also had a wonderful time later chatting with Jim and his dad Mike in their booth over in the Exhibit Hall.
The lead-up to WIA, in fact my very attending it, was predicated on the Monday morning appointment with the orthopedist. Much to my (expected) delighted, he noted that my recuperation was progressing excellently, and that at the six-weeks-and-four-day mark he released me to resume normal activities. I was now free to progress through the stages of bipedal locomotion, casting the walker aside and moving through the crutches and then a cane and then nothing.
We hit the road the next day, winding up in Kansas City on Thursday. Mrs. Barn was not sanguine with the idea of me driving, so she spent every mile of the trip behind the wheel.
Along the way we even took the time to do something we almost never do, we actually stopped and engaged in tourism. Since it was only 25 miles off the interstate we took the detour and spent a half-day at Pleasant Hill Shaker Village just outside Lexington KY. I was walking for four hours with the assistance to my pair of crutches. It was exhausting.
Worse than that, the almost nonexistent on-site programming and tepid presentation at Pleasant Hill was disappointing. We learned from the one fellow we saw working there that the plan to eradicate craft practices from the site will be complete in the hear future. To me that removes a return visit from the list of things to do.

Still there were some noteworthy encounters, beginning with the remarkable circular staircase at the building now serving as a restaurant and hotel.
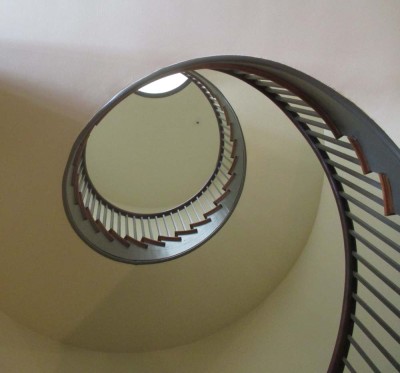
My steadiness on crutches was iffy, so I did not get the perfect picture from the bottom.
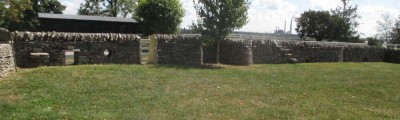
While walking around, probably my favorite thing of the whole place was this amazing stone wall.
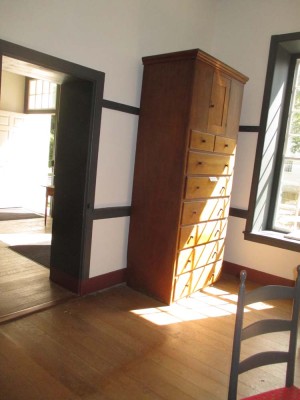
Among the pieces of furniture these two caught my eye. The first one has a one-piece side board, eight feet tall by about twenty inches deep,
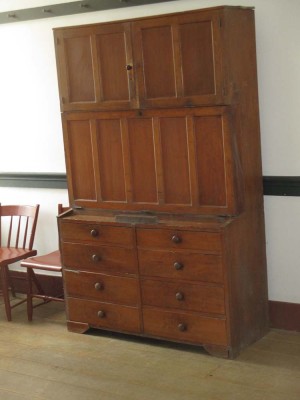
with this one being my all time favorite. I might have to build something like this some day.
Even though I was mobile, it was not sprite-like and my motion was super slow motion. This rendered much of the place inaccessible to me, but still it was terrific to spend the day upright and moving..
That night as I drifted off to sleep I had the delightful experience of aching from a day of “walking.”
Recent Comments