Whew! Concluding a few months of mostly traveling we got back to Shangri-la late Sunday evening after driving non-stop from Alabama, where L’il T’s family just moved (we were “helping,” a/k/a grandparenting L’il T and his brother). Travel advisory — avoid Chattanooga if at all possible, the construction and attendant constriction made it a more than an hour of stop and go experience at 97 degrees.
I am looking forward to resuming some semblance of norma life, including full days in the shop. This is made possible by the cessation of travel for most of the foreseeable future, along with finding a sturdy Mennonite lad to do most of the yard work. We were spending 3-4 days a week just keeping the grass cut, brush beat back, and trimming the edges. This young man could do what is necessary in 3-4 hours, rather than 3-4 days. Oh, to have the exuberance and fortitude of the young! That plus a $10k lawnmower makes a big difference.
Other than routine chores around the homestead I’ll be preparing for a Labor Day Weekend shindig at my friend Tim’s place, celebrating the historic crafts of our ancestors. I’ll be assembling a vintage-form tool kit to fit into my antique cabinetmaker’s tool chest which has been used as storage for the past couple decades. So, I’ll be there with tools and one of my Nicholson workbenches, in period costume, probably making a small dowry chest. If you are in the region, stop on by.
In addition I’ll be ramping up for my only teaching event of the year, a 3-day Introduction to Historic Woodfinishing workshop near Charlottesville VA.
And resuming work on my magnum opus tool cabinet, and oh by the way L’il T is now big enough to use a step stool to wash his hands and brush his teeth. The ones I made for his mom and aunt are still in service after 35+ years.
And my traveling tool kit needs completing. As do a couple of Gragg chairs. And those half-finished Studley mallet exercises, and the patterns for the genuine replicas. And the custom oculars for my rifle scopes, bypassing the now nearly defunct right eye (dominant). And the boat load of writing and editing staring me in the face. And setting up a video system to make in-shop vids after I get the Gragg video edited. And tuning my ripple molder.
And, and, and…
Beginning even before “Starting Time” we were inundated with a constant stream of visitors and the Donsbarn.com booth (the cracks in the barn door opening was soon breached by boomer sooners, who were eventually told to get out until 10 AM). I was working one aisle, John the other, and engagement was spirited.


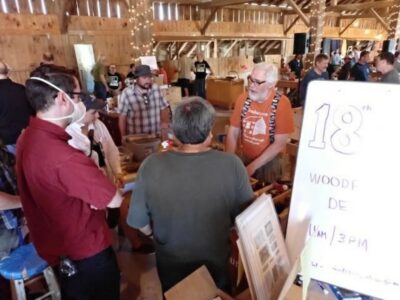
As I alluded in previous posts I had decided to give two 45-60-minute demonstrations of taking a parquetry panel from the rough to glossy, including the preparation and use of the polissoir. Each of the four demos was well attended — 15-20, which was all about the capacity of my 10′ x 10′ booth — with the observers arriving early and staying until the end. The 11AM demos were focused on cold beeswax finishing with true French polishing (wax and water), while the 3PM demos were all about molten beeswax followed by spirit varnish pad polishing.
Not much more to say or show visually, we were engaged with the flowing audience non-stop through the day, and we did not catch our breath and sit on out stools until 4.50, ten minutes before closing.

Awaiting show time Saturday morning.

Our booth was a perfect location for the Roy Show, but he stood exactly behind the post in the center of the frame.
The only difference in Day 2 was the huge crowd at the beginning of the day as the doors were opened at 9.30 in advance of the presentation by Roy Underhill. The rest of the day Saturday was much like Friday, with the only difference being that each of us were able to do an hour long walkabout to visit all the other venues and toolmakers. I’ll show some pics from my walkabout next time.
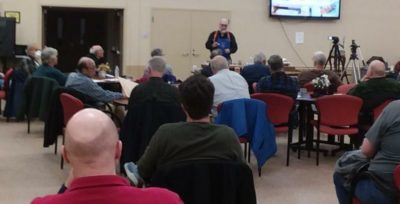
Last Saturday we were in Columbia, Maryland, first for my presentation to the Howard County Woodworker’s Guild, where a rollicking good time was had by all. I’ve spoken there twice before, most recently on the sober, memorable day of the second Space Shuttle disaster in 2003(?). There was no memorable public disaster last Saturday, other than the ongoing collapse of Western Civilization.
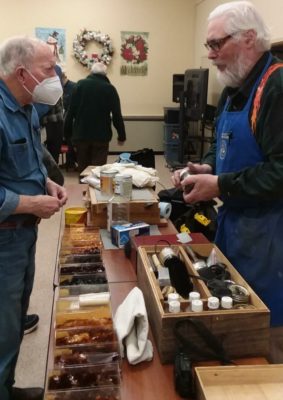
I had a such a terrific time! I sometimes forget how much I enjoy teaching traditional wood finishing. The large-ish audience was very engaged and I had some difficulty getting things wrapped up and loaded afterwards as person after person came to ask questions as I was packing up.
For this 75-minute demo I selected the highlights from my 3-day workshop Historic Wood Finishing. They might invite me back to teach that event, and I am pretty sure Joshua Farnsworth will ask me to teach it at his school near Charlottesville this summer. Check their respective web sites to catch any updates for that.
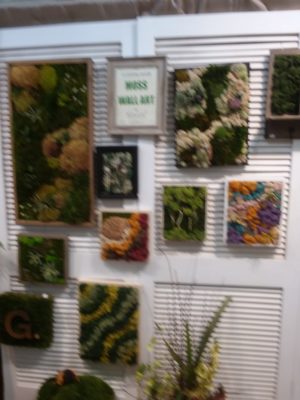
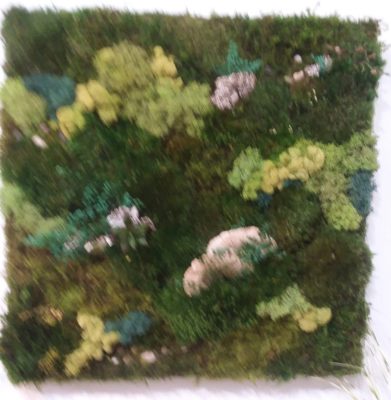
After this we met with long-time dear friends K and N to tour the moss art studio where she works, and consuming a delightful meal with them. We bought several of the moss art works as we were both enamored with them.
(I know, I am really lousy at taking pictures with my phone.)
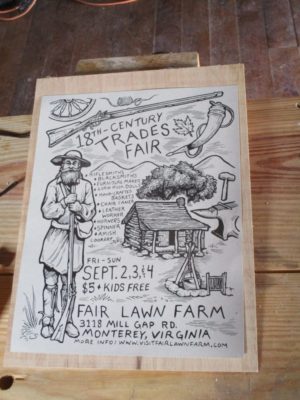
Some months ago I was approached by my friend TimD, who was organizing a “Historic trades” weekend at his place with fellow gunsmiths, horn workers, blacksmiths, weavers, etc. Tim is an accomplished craftsman, primarily making flintlock rifles and associated accessories like powder horns. So, he was gathering a number of friends and acquaintances for a weekend shindig open to the public and he asked me to demonstrate making my Tordonshell to the crowds. It was a peculiar technology to include but I was delighted to participate. I spent three days on display and explained Tordonshell to literally hundreds of attendees.
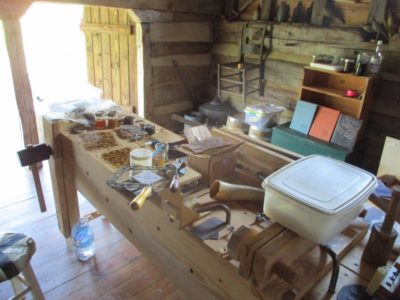
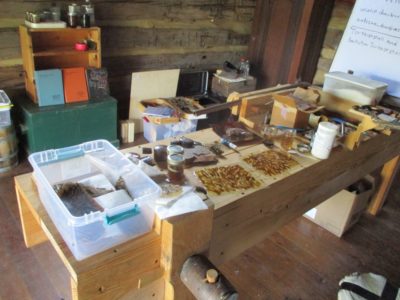
I was set up to occupy Tim’s gunsmith shop, a reconstructed late 18th/early19th log structure, using the partner’s workbench I built for him a few years ago.
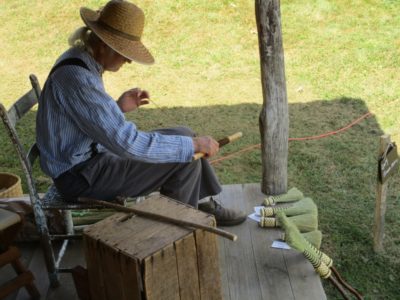
The front porch of the shop was occupied by other artisans including a wool spinner and my very own polissoir-maker Gary.
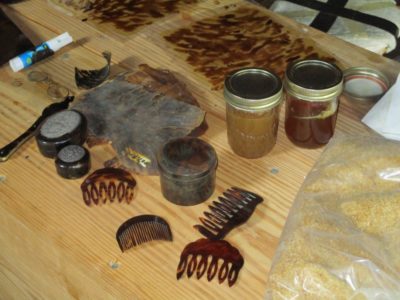
I was frankly surprised by both the number of visitors I had, and the intensity of their interest in both genuine tortoiseshell and my imitation of it.
Next year’s event is already on the books for Labor Day weekend and is expected to have around 30 demonstrators. I am already at work for my demonstrations, as I will be making things out of finished Tordonshell as opposed to making the Tordonshell itself.
I hope you can join u there.
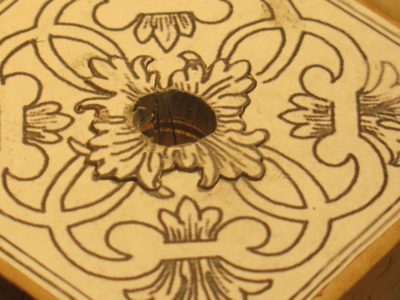
As I continued preparations leading up to last Saturday’s Boullework presentation to the SAPFM Blue Ridge Chapter I was able to make good progress once I discovered the cause of my earlier frustrations. Which was, as I realized once the initial center cut was completed and the material removed, that the first blade break resulted in a small fragment being embedded in the kerf. Every succeeding blade was damaged by encountering this fragment, continuing the sawing difficulties. When you’re talking 0000 blades it does not take much to throw them off.
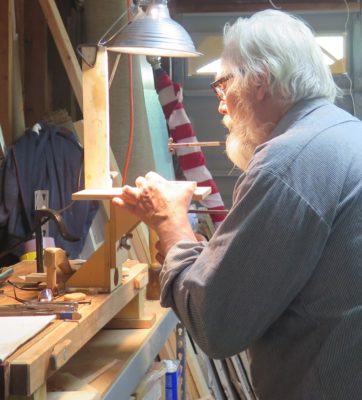

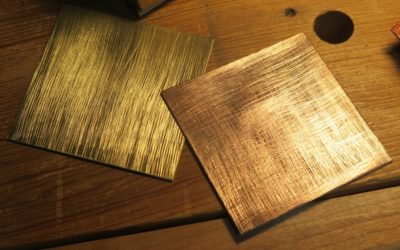

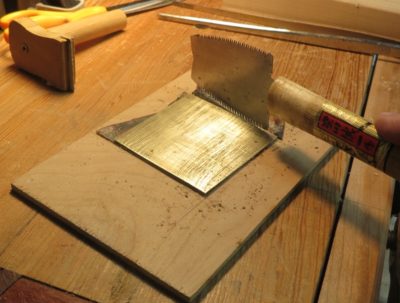
Getting a little more sawing done and assembling the demo materials was pretty straightforward.

I even made a scute of tordonshell. Fun, fun, fun.
PS Since I am on the home stretch for reviewing the Gragg chair video (probably about a dozen finished half-hour-ish episodes plus a bonus episode or two) and creating the edit sheets for the project, I am casting my brain forward to next winter. I am thinking about a shorter series on Boullework, Don-stye. Or at least revising and updating my original monograph from my presentation in Amsterdam.
It’s been quite a while since I 1) did any Boullework and 2) made a public presentation.

The last week or two I’ve been going through the exercises I’m demonstrating this coming Saturday to the SAPFM Blue Ridge Chapter, everything from making tordonshell to cutting some new Boullework panels.

When I assembled the metal and tordonshell packet and set about to sawing, the magic just wasn’t there. On a normal day once I get in the rhythm I can go for an hour or longer per saw bade, sometimes even half a day. But not this particular day. Sigh.

I was snapping blades like I was trying to break pasta. It took me four hours to saw a 1/2″ circle (and a pretty raggedy one at that) and I broke more than two dozen blades in the process. When I swept up the pile was truly impressive, but my camera was not handy.

Bad posture? Bad lot of blades? (it really does happen some time) Packet too thick? Rusty antiquated shoulder? Vision problems? (well, that is a given)
Some days are just like that. I’ll aim to get the bear tomorrow.

I am delighted that in the aftermath of being disinvited from the Winterthur conference on marquetry, the Blue Ridge Chapter of SAPFM immediately extended the invitation for me to make my presentation to their group on May 21 in Fredericksburg VA, at Woodworkers Workshop, 1104 Summit Street. I will be the afternoon speaker/demonstrator. It’s my first traveling presentation in more than two years and I am looking forward to it.
You can get any particular information you need through the SAPFM.org website if you are interested in attending, or you can let me know and I will forward your interest to our Chapter Coordinator. I think there is a $10 fee to cover coffee and lunch.
In related news, I will be one of the presenters (Historic Finishing) at the SAPFM Mid-Year Conference, coincidentally also in Fredericksburg, June 26.
I recently attended and spoke at Groopshop 2019, about 25 miles southeast of Minneapolis on our friend Matt’s farm. I do not recall the finally tally of attendees but I’m estimating about 60 folks convened for three days of intense fellowship and exchanging of knowledge and ideas related to the furniture restoration enterprise.
My talks were on the topics of insect eradication in infested wooden objects (video recorded en toto and certainly to make it to the interwebz at some point) and toolmaking, especially low tech tool making as part of the restorer’s art.

Topics for the other presentations and demonstrations included the far-flung topics of Wood Finishing Terminology, Custom/Production guitar Finishing, Repairing Metal Hardware, Leather Repair, Museum Upholstery, Polishing Out Finishes, Reactive Colorants In/On Wood, History and Technology Of Aerosols, Government Regulations for Refinishing Shops, and many more.

The sessions were interspersed with eating and small groups congregating, and I look forward to our next gathering. A truly grand time was had by all.

Since its beginning Groop has been a moderated email forum but we learned that on Jan 1 it transitions into a private Facebook discussion group.
The second day of GroopShop was just as engaging and instructive as the first, and one again I was paying so much attention to the speakers that my photo record was not as good as it should have been.
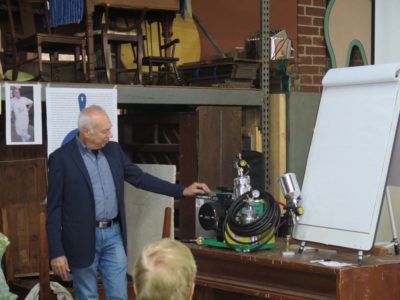
The opening session was a demo by one of the reps from Apollo Spray Systems, the HVLP units used widely in our circles. The blow-by-blow of the history of product development was fascinating to me.

My friends Mark and Valeri from Besway/Benco, manufacturers of chemicals and products for the finishing room, provided a chilling account of the regulatory war against our trade. Do Gooders are relentless, that is why they win unless they are opposed in a smash-mouth fashion by someone with the means to do so. Since sanctimonious moral certitude is the regulator’s fuel, I do not expect us to prevail for the most part.
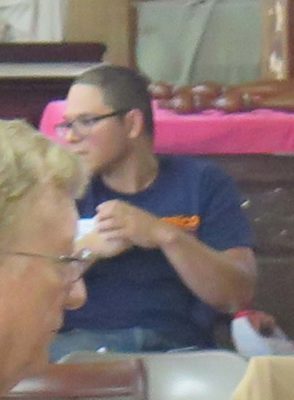
Freddy Roman gave an impassioned and enlightening talk about using social media for marketing his business. In that realm he really is the Energizer bunny. Were I less curmudgeonly I might go this route.

I gave my 120-minute spiel on “Decoding Hide Glue,” covering everything from manufacture to modification to application. We got almost all of it recorded and it will soon be posted, or at least as soon as I can knit it all together.

Bill Ryan is an on-site-work warrior doing mostly architectural punch-list work in new construction, and he brought his complete traveling workshop with him to show its contents and applications. Very inspiring. I am still kicking myself for not taking a picture of his traveling kit.
Tom Delvecchio presented his recent fascination and exploration of 3D printing and its applications to his work in the restoration shop. I’ve long been considering this technology, and since there is a manufacturer her in this county I will delve more deeply.
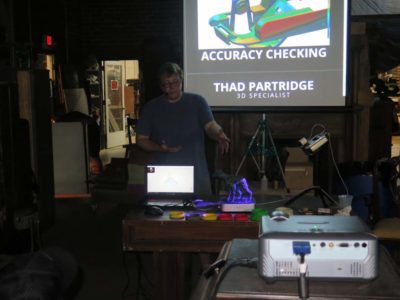
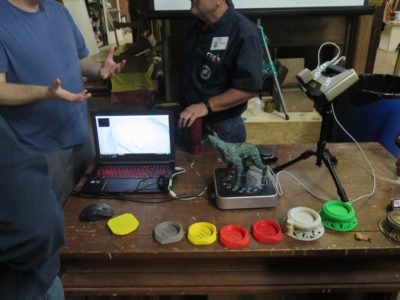
The after-dinner talk was one of the most intriguing I’ve seen as a young fellow demonstrated 3D imaging and its link to robotic 3D manufacturing. The implication for replicating metal furniture parts especially was astounding. We used to work on 3D imaging at SI and the progress made in this area is staggering.
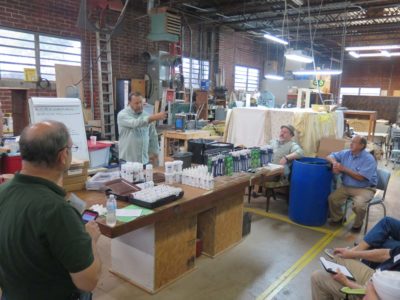
The final presenter for the gathering was the next morning with the rep from Mohawk covering his line of products, and how that offering has changed over time. Like many practitioners of the furniture restoration arts Mohawk is what I cut my teeth on; I attended a Touch-Up workshop back in 1974 and still have drawers full of the materials I got then, using them as needed to this day.
And thus endeth GroopShop 2018. As always I came away inspired and informed. If you have any interest in the finishing and restoration arts, you should belong to the Professional Refinishers Group.



Mrs. Barn and I spent the afternoon at the Atlanta Botanical Garden. It was delightful. Then we drove home. Less delightful.
For the final session of the SAPFM Tidewater Chapter Spring Meeting I was asked to talk about “matching color” but I took the liberty of broadening the topic to “matching appearance” which I think is more useful. Though my demonstration component did indeed focus on understanding the perception of color and its modification, it occurred within the larger context of “appearance.” Normally this is a topic I like to spend a week covering, so in 90 minutes I barely got to the highlights. In fact, at this fairly late date I have decided to add a full chapter on the topic to my Period Finisher’s Manual book for Lost Art Press.

There are many aspects of appearance of interest to woodfinishing and I addressed each and their interrelation briefly. One point I made repeatedly is that if matching color is a critical component of any projects, that must be accomplished in the finishing layers (or between them), NOT in staining the wood.

Trying to match any color via the manipulation of wood stain on the bare wood surface is a fool’s errand. To get to where you want to go, you must know where you are starting. And that means the wood surface must be sized with enough coating to establish the base appearance and color.
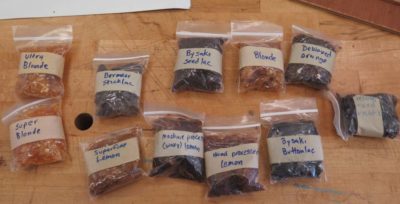
There are times where the selection of the coating itself is a critical component of achieving a specified color.
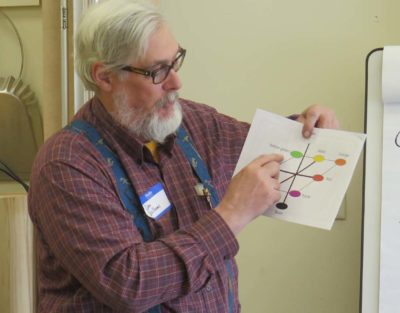
Once you get to the point of manipulating the coloration, I believe that the traditional color wheel is inadequate to the task. Instead I prefer a different conceptual model for color, and that model is known as the “L,a,b” color system. I will not go into detail here as to how I use this system in my own color work, suffice to say it is functionally a subtractive system i.e., if something is too red, I add green, if it is too yellow I add blue, to neutralize the excess color.

Adding tonality to the surface appearance can be achieved through tinting the coating itself with dyes or pigments. Here I am using some very intense organometallic synthetic dyes that were originally created for industrial and automotive paints, if I recall correctly. These are Orasol dyes and have a somewhat peculiar palette to select from, and are available to the finishing trade at Olde Mill.

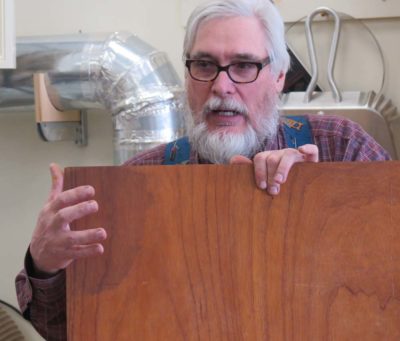
The means of imparting coloration are many, and once again I only use color in or in-between the finish. One of the simplest and most effective techniques — and historically accurate to boot — is a light glaze of asphaltum.

And speaking of glazing, I spoke for a few minutes about how to determine whether or not you have good glazing brushes.
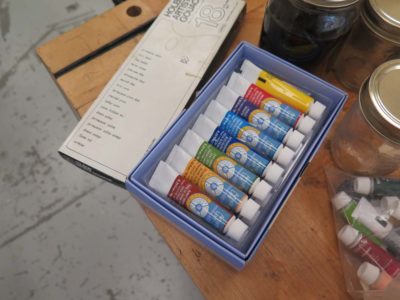




Another glazing technique I demonstrated was using artists’ watercolor paints known as goauche with a waterborne shellac binder that I made right there in the meeting. If you do not get the color or tonality correct, just wipe it off with a damp rag and start over again. You have perhaps a half hour to do this before the waterborne shellac sets, and it is very tenacious once dry.
And then it was time for everyone to go home.
Recent Comments