For the home stretch of the jam-packed three-day workshop the final set of exercises involved the giant panel. It had already served its first purpose, getting the students comfortable with laying down an exquisite brushed shellac surface over a large area. Since the panels were roughly half the size of a dining table, I’m thinking any hurdles of intimidation have been overcome.
At this point the panel was subdivided into four quadrants, each of them to be treated in a unique manner. The first quarter was easy — just leave it alone as an example of laying down an excellent base of three-inning shellac.

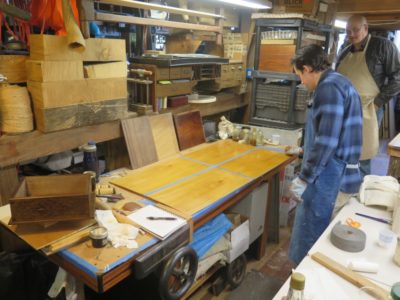
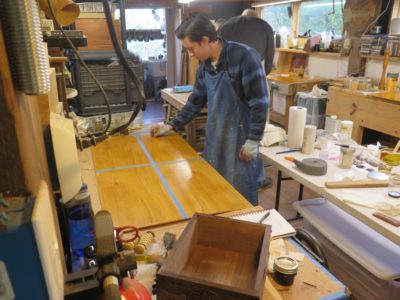
A second quarter was spirit varnish pad polished to a high sheen, demonstrating the option of creating a not-grain-filled padded surface.

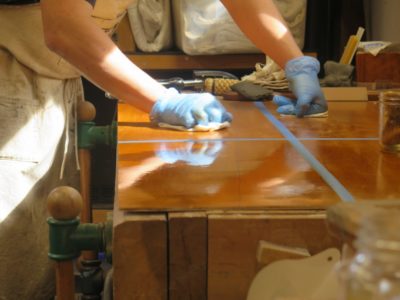
The third quarter was hand polished with abrasive powders, first 4F pumice then rottenstone in mineral oil, using a polishing pad identical to the spirit varnishing pad. This was followed by a light application of paste wax and buffed when the wax was firm.

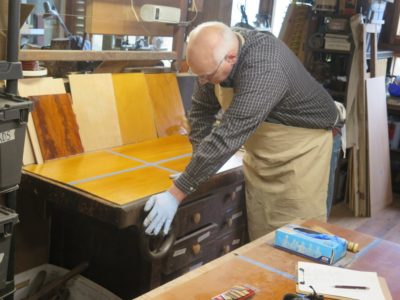


The final quarter was burnished with Liberon 0000 steel wool saturated with paste wax, and as with the rottenstone polishing, rubbed until you just get tired. When the paste wax was firm ex poste it was buffed with flannel to a brilliant glow.
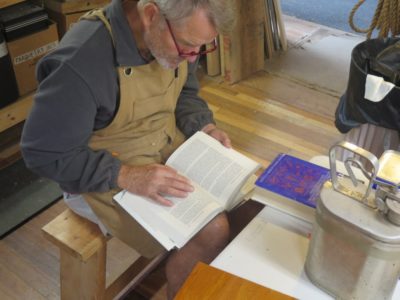
As always there is at least one somebody who gets seduced by my library.

When we wrapped up the event it was clear that they had all mastered the techniques wonderfully, and departed with confidence and a set of sample boards to guide and inspire them for decades to come.
If scheduling a workshop identical to the one these fellows completed, drop me a note. I will no longer “schedule” any workshops but only host them on request.
… to prepare for.
This week I was formally disinvited from presenting at the Winterthur marquetry conference this upcoming April, so those scores of hours over winter I had budgeted for creating my Boullework demonstration and writing the subsequent book chapter has now been cleared from my schedule.
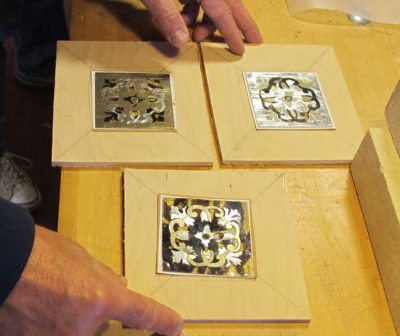
As I was chatting recently with a woodworking friend about my presentation at the conference, he asked, “Do they know about your attitude regarding Covid protocols?” Gobsmacked, it had never occurred to me. Given our daily lives in the least populous county east of The Mississippi, it is simply not a common part of the conversation for people with whom I associate. Yes, Covid is a real pathogen and yes it has impacted our community (many, if not most, of the people I know here have had it), but we live our lives normally without disruption and do not obsess about it. I realized I should extend the courtesy of informing the conference organizers explicitly of my position, which I did in unambiguous terms.
Our county has been de facto mask-free for 18 months with numerous public gatherings like concerts, civic commemorations, seminars, etc., aside from some of the “larger” businesses like our local banks, the courthouse, school, and the medical center (the only entity for which masking makes a lick of sense). We talk face-to-face, we shake hands and hug, we dine together in homes and restaurants, we conduct business with each other as normal.
Our church suspended worship for a month in early 2020 then resumed worship and encouraged masking for another few weeks, but has met continuously since last Spring with all protocols being voluntary. Has there been Covid in our congregation? Certainly there has but everyone has recovered nicely, even our pastor who became the most gravely ill of the cases in the county to that point. Ditto every other church in the county (the Mennonite Church has exactly two adults who have not had Covid). Even the banks do not require masks for customers, only the staff are wearing them, which creates an exceedingly off-putting atmosphere. We have had hundreds of cases in our county of 2100 people, but only two “Covid deaths,” both of whom for which the pathogen was merely the final straw for exceedingly compromised personal health.
In short, I informed the Winterthur marquetry conference organizers that I have not and would not be getting any of the experimental gene therapy injections, nor would I wear a mask while in attendance at the conference. If they were fine with that, great. If not, well, “Houston, we have a problem.”
Houston had a problem.
The host institution would not allow me to attend under those terms, so I will not. I have my views and they have their rules, and apparently never the twain shall meet. I certainly bear no ill will and hope the conference is a resounding success! If it is live-streamed I will probably check into the proceedings.
An unexpected batch of time cleared? Check.
Washington, D.C.
October 3, 1863
By the President of the United States of America.
A Proclamation.
The year that is drawing towards its close, has been filled with the blessings of fruitful fields and healthful skies. To these bounties, which are so constantly enjoyed that we are prone to forget the source from which they come, others have been added, which are of so extraordinary a nature, that they cannot fail to penetrate and soften even the heart which is habitually insensible to the ever watchful providence of Almighty God.
In the midst of a civil war of unequalled magnitude and severity, which has sometimes seemed to foreign States to invite and to provoke their aggression, peace has been preserved with all nations, order has been maintained, the laws have been respected and obeyed, and harmony has prevailed everywhere except in the theatre of military conflict; while that theatre has been greatly contracted by the advancing armies and navies of the Union. Needful diversions of wealth and of strength from the fields of peaceful industry to the national defence, have not arrested the plough, the shuttle or the ship; the axe has enlarged the borders of our settlements, and the mines, as well of iron and coal as of the precious metals, have yielded even more abundantly than heretofore. Population has steadily increased, notwithstanding the waste that has been made in the camp, the siege and the battle-field; and the country, rejoicing in the consciousness of augmented strength and vigor, is permitted to expect continuance of years with large increase of freedom.
No human counsel hath devised nor hath any mortal hand worked out these great things. They are the gracious gifts of the Most High God, who, while dealing with us in anger for our sins, hath nevertheless remembered mercy. It has seemed to me fit and proper that they should be solemnly, reverently and gratefully acknowledged as with one heart and one voice by the whole American People. I do therefore invite my fellow citizens in every part of the United States, and also those who are at sea and those who are sojourning in foreign lands, to set apart and observe the last Thursday of November next, as a day of Thanksgiving and Praise to our beneficent Father who dwelleth in the Heavens. And I recommend to them that while offering up the ascriptions justly due to Him for such singular deliverances and blessings, they do also, with humble penitence for our national perverseness and disobedience, commend to His tender care all those who have become widows, orphans, mourners or sufferers in the lamentable civil strife in which we are unavoidably engaged, and fervently implore the interposition of the Almighty Hand to heal the wounds of the nation and to restore it as soon as may be consistent with the Divine purposes to the full enjoyment of peace, harmony, tranquillity and Union.
In the finishing trade we often quip that our job is to make wood, “Brown and shiney.” Historically one of the main methods employed for the “brown” part was asphaltum, or tar. I knew of using tar as a toning glaze in gilding, where the tar would be diluted with white spirits and used to accentuate the gilded surfaces. I had not used it for wood until about fifteen years ago, responding to the evangelism of Alan Noel, a/k/a “The Czar of Tar,” and famed Atlanta based finisher and restorer and long time friend

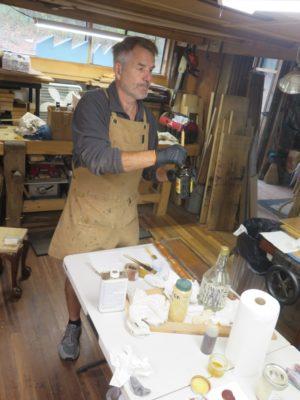
For the workshop I’d asked Knoxville Dave to provide instruction on both pad polishing and asphaltum glazing, since he does so much more of that than I do. Yes indeed, that is a can of fiberless parging asphalt that he is mixing and diluting to glaze consistency.
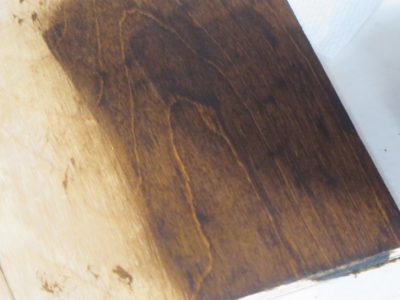
We both using glazing as our “go to” technique for coloring, since it is so much more controllable than any penetrating colorant, and can be controlled to perfection. Sometimes staining works perfectly, but is is “just off a little bit” enough to take that technique off the table for me.
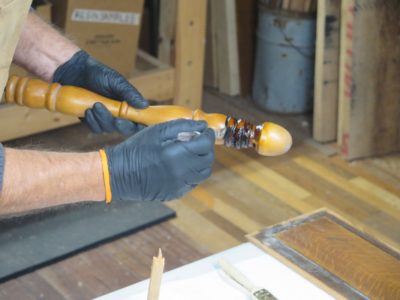


The exercise that really showcases the asphalt glazing technique was toning the turnings. They were first shellacked then burnished, leaving a magnificent foundation on to which you lay the color. The dilute asphalt was spread on the surface, then manipulated with cloth pads and fine bristle brushes to provided subtle shading to the presentation surface.
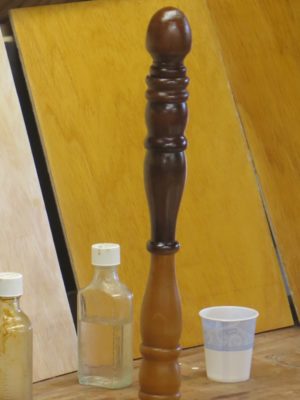
One of the beauties of asphaltum is that it performs almost like a dye, yet can be manipulated to provide both understated and exuberant change.

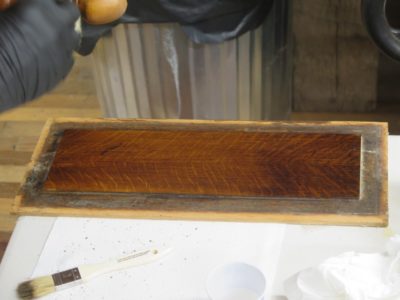

Dave also demonstrated using the glaze on a flat panel to great effect, mimicking the “ammonia fuming” so prized in Craftsman furniture finishes.
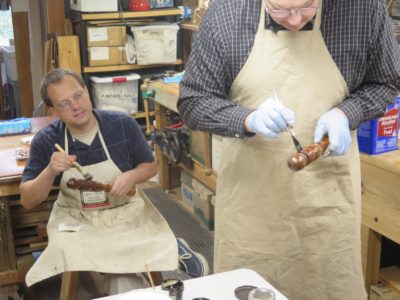


With that, the students were turned loose on the workpieces.

One of the fellows did some asphalt glazing to his new carved Bible box to great effect.
After the asphalt dried the surfaces were sealed with another coat of the shellac varnish.
The only thing left for the workshop was final detailing for the mega panel. Stay tuned.
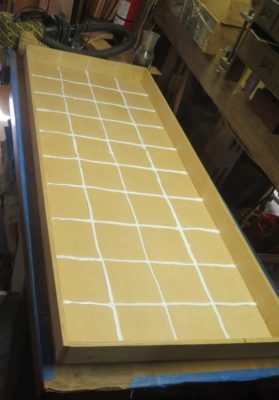
Gluing the internal ribs was no big deal; first I dry-fit all the ribs then marked their locations, so that I would know where to put the bead of glue. I used PVA mostly because I have a lot of it left over from another project and just wanted to use it up.
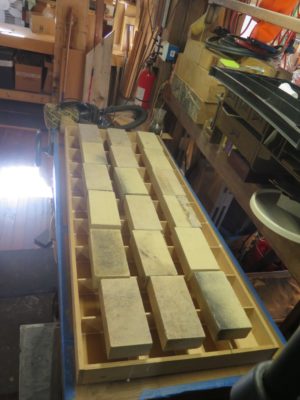
Once the glue lines were down and the grid re-placed on top of them I simply “clamped” them in place with a couple hundred pounds of bricks. Everything stayed put over night and in the morning all was well.

I moved on to the backing blocks needed for the threaded screw holes and a couple of other features. For the threaded vise holes I just held them in place with spring clamps.
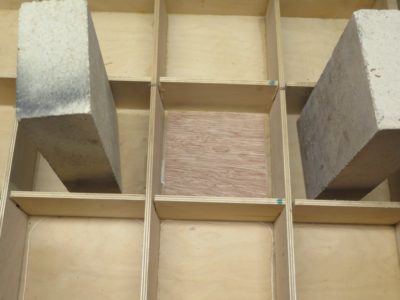

For the backing blocks on the top and bottom faces I uses more of the same ‘brick as clamps” strategy.
One area of great frustration, fear and failure for many woodworkers is the challenge of applying a hand-finish to voluptuous surfaces, including carved and turned objects. While I could not provide a syllabus with examples of every possible option in this exercise I was able to introduce the principles, practices and tools requisite for the task. The key to success in varnishing the curvey parts is to use the correct tool, in this case an oval wash or Filbert Mop brush for watercolor paintings.
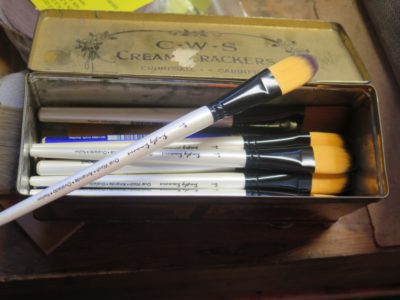


There are many excellent brands of watercolor brushes for artists that work brilliantly for wood finishing, but I have sorta settled on Simmons brushes in part because they were widely available at Michael’s. Even their cheapest brush, the “Simply Simmons” line, can provide an exquisite brushed surface. I have a few of the middle-quality brushes, the Simmons Sienna line, and they are even better. Of the premier line, the Simmons Sapphire, I have about a half dozen, and they are sublime, a blend of nylon fibers and sable bristles.
Regardless of which one you choose, and the price range is around $10-15 for the Simply Simmons to $75-100 for the Sapphire, you will have excellent results on undulating surfaces because the Oval Wash/Filbert Mop configuration does not have the square corner typical for most brushes. Those corners are the source of nothing but headaches on the carved or turned surface as it is the corners that “squeegee” off excess varnish, leading to the runs, drips, and errors that are the curse from finishing with the wrong tool.

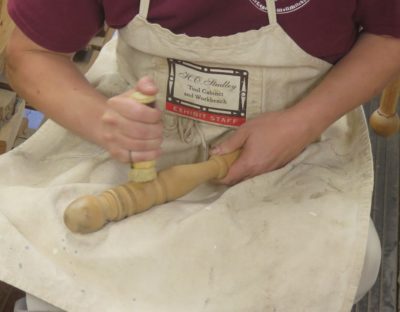
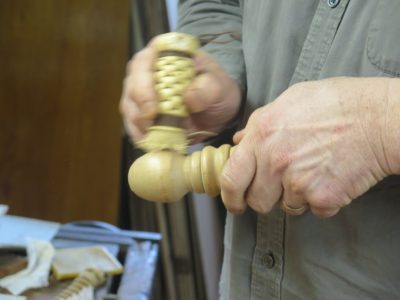
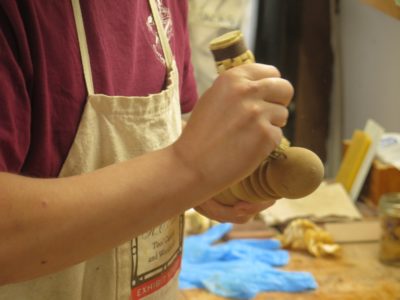
In this workshop I had a pile of turned spindles and frame-and-panel cabinet doors to provide the battleground for the exercises. As almost always the starting point is to burnish the entire surface with a polissoir, and I have designed a “Carver’s Model” polissoir with 3/4″ bristles for just this instance.


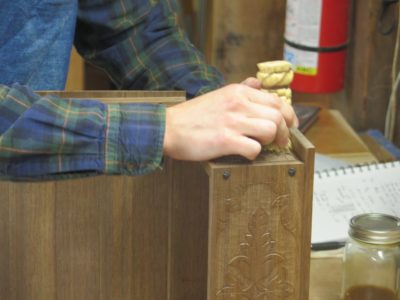

One of the real delights for the workshop was that one of the students had just made a carved Bible box the week before, and brought it along for the class.

The transformation of the raw carved surface by the application of a few minutes’ worth of burnishing was truly astounding.

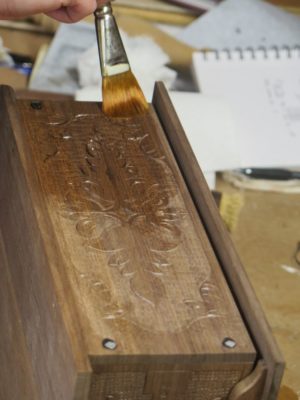
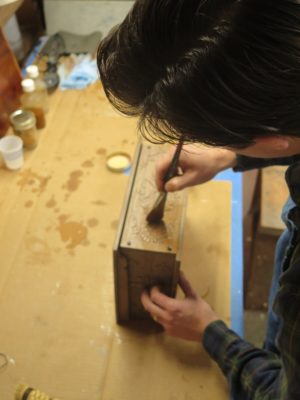
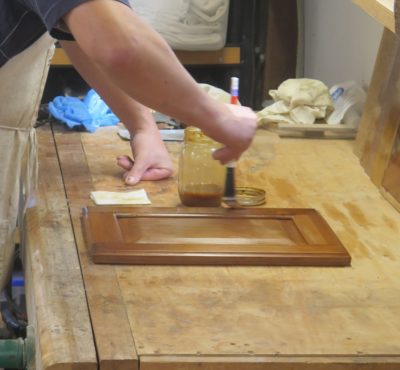
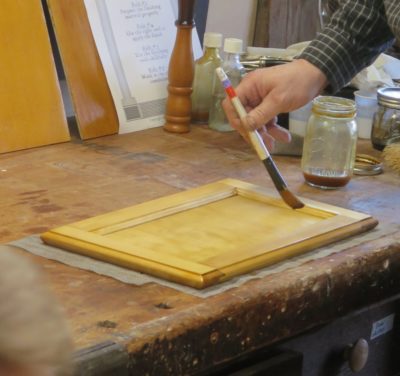
Then it was time to get to brushing the shellac varnish, and the draping character of the oval brushes – almost literally clinging to the irregular surface – was life-changing to the students as they were able to lay down multiple flawless applications of varnish.
Suddenly, what had been an aspect of wood finishing imparting fear and loathing became something to anticipate with celebration.
The last couple of weeks have been the whirlwind we have come to expect about this time every autumn as the yard is mowed one last time, garden is put to bed, the cabin and barn are readied for our vigorous winters (clear plastic is taped over all the cabin windows; three years ago was insulating and sealing the crawl space, two years ago was re-chinking the the cabin logs, this year was the new roof, and next year will be new windows all around), and the requisite tons of firewood are processed.
While Mrs. Barn toiled for several sunny days with the final harvests from the garden and the uprooting and soil-turning involved in the aftermath, along with digging up hundreds of flower bulbs to be stored in the crawl space under the cabin, I was tasked with building a new cover for the raised bed she uses for growing greens long into the winter. That raised bed has always had a winter cover but the last one finally gave up the ghost so a new one was required.
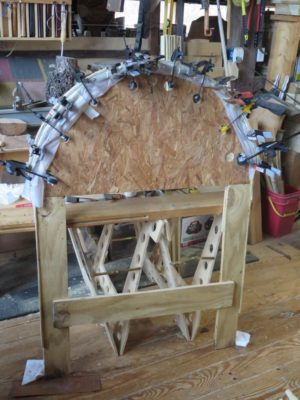
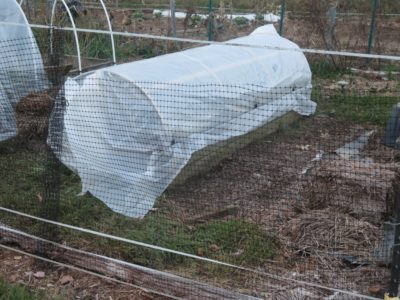
I decided to build this one a good bit nicer and sturdier than the previous one, including four-ply laminated hoop ribs. Since this project was one that is likely to be reprised over the years we have here I made a frame on which I could assemble and glue the curved elements from 1/8″ resawn PT SYP. I used T3 for the adhesive, gluing up one new rib every day. Somehow I managed to fail in the picture-taking department, but in the end I have a custom-fitted cover for the bed.
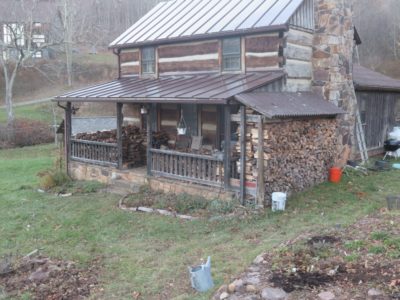
After that I moved on to the annual re-stocking of the firewood pile. I had about half of it already cut, split, and stacked on pallets next to the barn. Once I moved that down to the crib I decided to process the remaining needed for the front porch even though I had a sizable surplus in the lower barn.
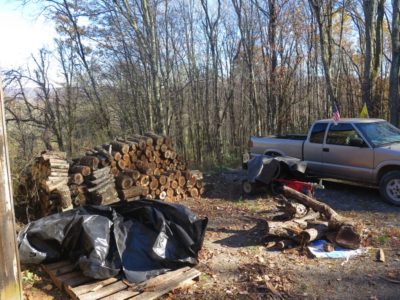
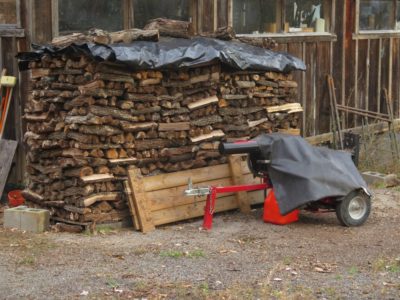
I got into the rhythm and worked my way through the whole pile of cut wood left over from last year (I still have about 2-3 years’ worth felled up in the woods, which I will process as time and inspiration allow over this winter), and wound up in the place I’d always wanted to be – starting a winter with two winters’ worth of firewood ready to go.
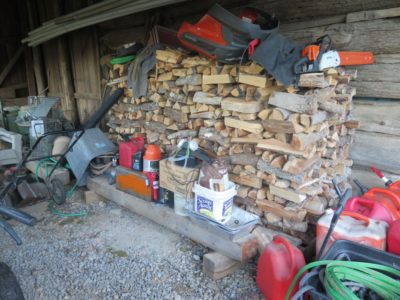
This was the excess pile in the lower barn from last year so I just left it alone to serve as the future BTU inventory.
Somehow this modest set of accomplishments managed to occupy nearly a complete fortnight.
Sigh.
Back to regular order until spring, I hope.
I’ve not posted for almost two weeks, but in answer to the question, “Did you injure yourself again?” the answer is “No.” It’s just been the period on the homestead that is always action packed every year, closing down the gardens after summer (Mrs. Barn was still harvesting beans and squash until a few days ago!) and getting the place ready for winter, combined with extensive barn cleaning (oh yeah, that’s a burning blog topic — “Watch me organize my inventory of dry powder pigments and tubes of oil paints and watercolors.”) This year it all included making a new hoop-house cover for the raised bed she uses for greens long into winter, and as always splitting and stacking tons of firewood cut last year, and much more. Alas, I do not work as quickly as I used to, nor for as long, and every year an armful of firewood gets just a little bit heavier.
Things should be back to the “normal” routine by the end of the week. I’m delighted to have been able to leave the wood stove unused until the halfway point of November this year, it will get fired up perhaps next weekend, wondering if the generally mild autumn will transition to a brutal winter. If so, we are ready.
Stay tuned.
Recent Comments