N.B. Things have been crazy busy in a wonderful way and I’m looking forward to a more sedate pace in the coming days. Stay tuned. — DCW
Three weeks ago I gathered with 10 novitiate varnishistas from around the country for a three-day romp down the long and winding trail of historic woodfinishing hosted by Joshua Farnsworth at his Wood and Shop facility near Charlottesville VA. Over the years I have evolved a very tight syllabus to make sure every participant leaves with a set of successful exercises under their belts, or fingernails as the case may be. This solid foundation allows me to work around the edges and incorporate some new things as I did this year, with mixed success.


A large part of the course success is due to the fact that I supply EVERYTHING for the students to use. Though that is a substantial undertaking it does guarantee a greater chance of success than if I mail out a supplies-and-tools list. After a couple experiences of wasting several hours of class time scrounging up supplies, tools, and projects for the students who forgot them I tossed that concept overboard many years ago.
The routine should be fairly familiar to anyone who follows this blog, so this year I will simply be posting a gallery of images to capsulize the three days. There is no way a few pictures can convey fully the richness of the event from either a learning or fellowship perspective, plus there were many portions where I had no pictures because I was, well, teaching. There are entire exercises that were not included in the photos.

Smoothing the 24″ x 48″ birch plywood panels in preparation for fifteen coats of 1-1/2-pound lemon shellac.

Shellac makes its first appearance
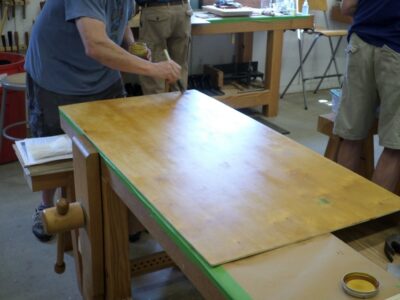
The end of the “first inning” (five brushed coats of shellac)
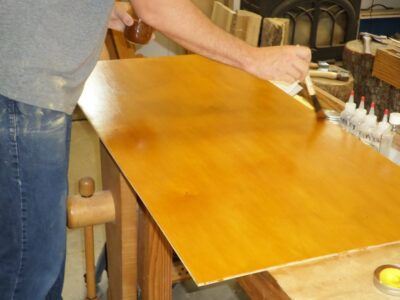
After drying for several hours, we ended Day 1 with a light scuffing of 220 sandpaper followed by another five brush coats of shellac.
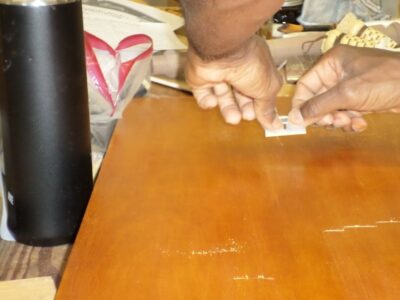
After drying overnight following the “second inning,” the surface was uniformly scraped, followed by a “third inning” of five coats and set aside to dry for 24 hours.

The final steps for the large panel included dividing it into quadrants, each of which was treated differently. This quadrant was dry-pumiced in preparation for shellac pad polishing.
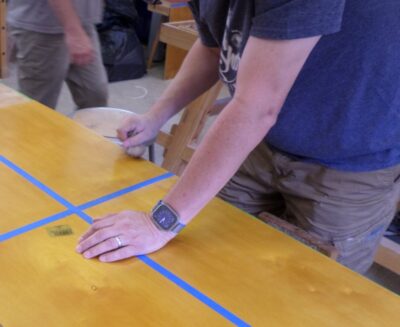
Final shellac varnish pad polishing.
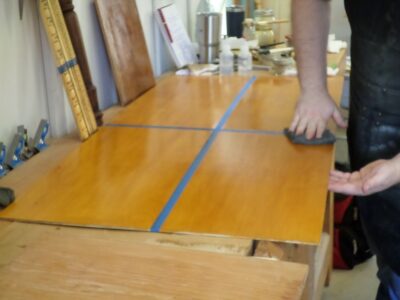
A second quadrant was polished with tripoli (rottenstone) in white spirits, the third was rubbed strenuously with Liberson 0000 steel wool saturated with paste wax, and the fourth was left “off the brush.”

Smoothing a mahogany panel with a pumice block.
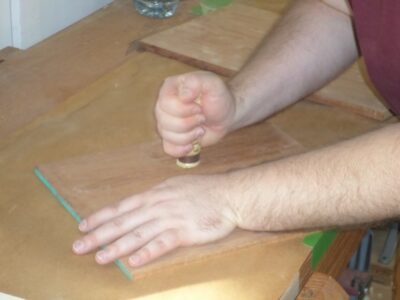
Working the mahogany panel with a 1″ x 1/8″ polissoir, followed by molten beeswax (scraped clean) as a grain filler.

Making and using a linen pounce/pad to apply the 1/2-pound shellac varnish.
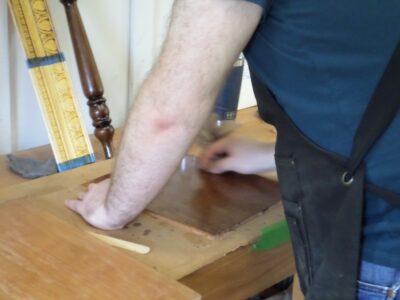
Building the padded shellac varnish.
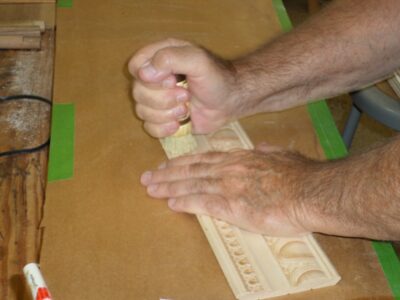
Burnishing an embossed molding with the Carver’s Model polissoir, followed by a few coats of brushed shellac.

Revisiting the shellacked surface with the Carver’s Polissoir.

Applying asphalt glazing to half of the molding piece.

Feathering out the asphalt glazing with a badger brush.
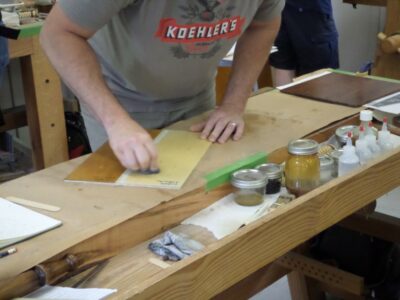
Comparing the appearance of five coats each of Bullseye Amber and Bullseye Clear from the hardware store.

A classroom full of busy varnishers.
And much, much more.
So there’s a snapshot (pun intended) of the recent gathering. I know we will have the class again next summer at the school in Earlysville VA.

These are the handouts of the syllabus for the upcoming Introduction to Historic Woodfinishing workshop, honed over the years and the dozens of times I’ve taught the workshop. About the only changes I make any more are if the course schedule is truncated to be shorter than the three days I have here.


In my collection of 3,000+ vinyl albums is the Pink Floyd double live album Ummagumma, with the memorable photograph of their traveling equipment artistically arranged on a landing strip.

It is reminiscent of my own preparations for my upcoming Introduction to Historic Woodfinishing next week in Earlysville VA. As I’ve said previously, I found out long ago that the only way I could make the workshop complete and beneficial for all the attendees was to provide absolutely everything they need, in terms of workpieces, tools, and supplies. And that adds up to quite a pile of materials.

At this point I’m about 2/3 of the way there. All I know is that by the time I pull out of here next Wednesday the bed of my truck will be full.
The first couple of times I taught Introduction to Historic Woodfinishing about forty years ago, I would send a “tools and supplies” list for the participants to acquire on their own, and indicated we would be working on their own projects and work exercises in the class. It did not take me long to realize that at least one person in the class would arrive with the wrong tools and supplies (usually making substitutions that were inadequate) or arrive without a project, in which case we were running around last minute to come up with some pieces of wood for them to work on.

A turned walnut spindle for each student to learn finishing on curved surfaces.

A pile o’ hardwood and luan plywood panels for each of the exercises.
Ever since then I have found the only way to fulfill the syllabus was to provide everything for every student, an undertaking that is not an inconsiderable resource sink. But, this way everyone gets the full experience I have planned for them. (I found the same hurdles to my Japanning classes and employed the same solutions.)
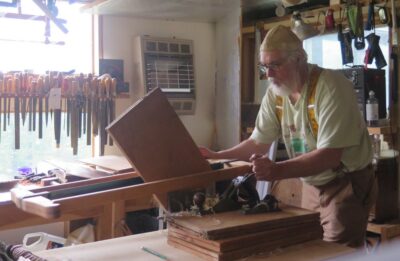
For the past several days I’ve been assembling all the necessaries for my upcoming class, including bins of work pieces, supplies, tools, and cases of jars. Among them is a couple hardwood panels (one mahogany, one cherry) to compliment the plywood panels that suffice for most class work. To that end I spent the day yesterday resawing six cherry panels (22″ x 11″ x 5/4″) and mahogany panels and am working through hand planing them. My approach is to usually flatten cross grain and finish along the grain.
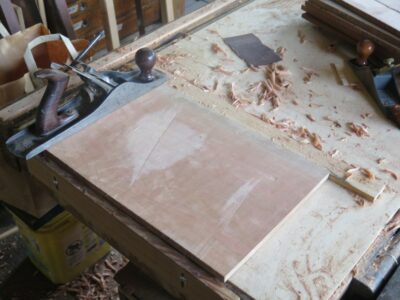
I don’t know if it has been the recent months of absence from Shangri-la or the fact that I am completing my seventh decade, but this morning my shoulders and hips are barking. Loudly.
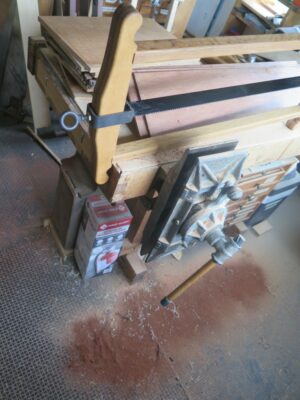
Nevertheless I enjoy immensely the shop floor aesthetics at the end of a very productive day.
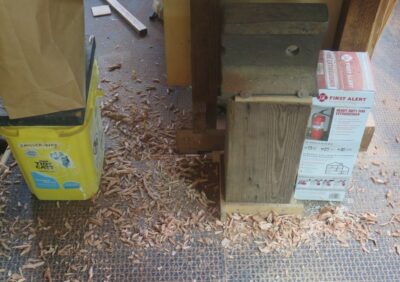
Whew! Concluding a few months of mostly traveling we got back to Shangri-la late Sunday evening after driving non-stop from Alabama, where L’il T’s family just moved (we were “helping,” a/k/a grandparenting L’il T and his brother). Travel advisory — avoid Chattanooga if at all possible, the construction and attendant constriction made it a more than an hour of stop and go experience at 97 degrees.
I am looking forward to resuming some semblance of norma life, including full days in the shop. This is made possible by the cessation of travel for most of the foreseeable future, along with finding a sturdy Mennonite lad to do most of the yard work. We were spending 3-4 days a week just keeping the grass cut, brush beat back, and trimming the edges. This young man could do what is necessary in 3-4 hours, rather than 3-4 days. Oh, to have the exuberance and fortitude of the young! That plus a $10k lawnmower makes a big difference.
Other than routine chores around the homestead I’ll be preparing for a Labor Day Weekend shindig at my friend Tim’s place, celebrating the historic crafts of our ancestors. I’ll be assembling a vintage-form tool kit to fit into my antique cabinetmaker’s tool chest which has been used as storage for the past couple decades. So, I’ll be there with tools and one of my Nicholson workbenches, in period costume, probably making a small dowry chest. If you are in the region, stop on by.
In addition I’ll be ramping up for my only teaching event of the year, a 3-day Introduction to Historic Woodfinishing workshop near Charlottesville VA.
And resuming work on my magnum opus tool cabinet, and oh by the way L’il T is now big enough to use a step stool to wash his hands and brush his teeth. The ones I made for his mom and aunt are still in service after 35+ years.
And my traveling tool kit needs completing. As do a couple of Gragg chairs. And those half-finished Studley mallet exercises, and the patterns for the genuine replicas. And the custom oculars for my rifle scopes, bypassing the now nearly defunct right eye (dominant). And the boat load of writing and editing staring me in the face. And setting up a video system to make in-shop vids after I get the Gragg video edited. And tuning my ripple molder.
And, and, and…
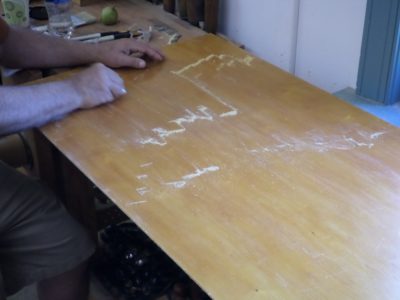
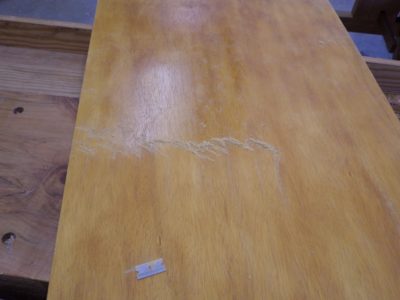
Day 2 began with scraping the large panels with razor blades to get them really smooth, followed by a final “inning” of 5 or 6 coats of shellac varnish, giving a total application of about 15 coats. These were then set aside for final rub-out at the conclusion of Day 3.

We then moved on to brushing a few coats of varnish on turnings and embossed moldings to introduce the notion of using an oval tip brush on undulating surfaces. The right tool makes all the difference.
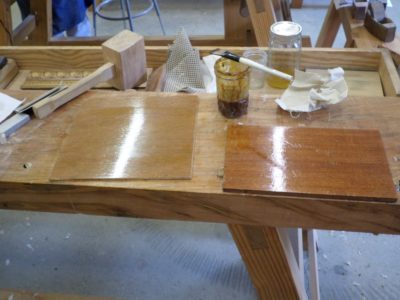
Smaller panels were varnished in preparation for further exercises; the plywood panel was for water/wax polishing (we never got to that one since we ran out of time) and the mahogany panel was for spirit varnish pad polishing.

The final event of the day was applying, scraping, and buffing a molten beeswax foundation to these solid cherry panels in preparation for subsequent pad polishing. Prior to the advent of plaster-like grain fillers in the late 19th century, beeswax was the grain filler for almost all glossy finishes.
It might not sound like much but these activities did fill the whole day.
Thus endeth Day 2.
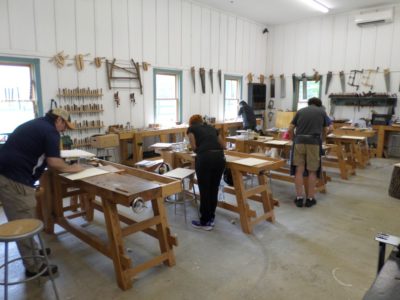
I recently had the great opportunity to teach my 3-day Introduction to Historic Woodfinishing workshop at Joshua Farnsworth’s Wood and Shop school. I have probably taught this class twenty or thirty times, having settled on a base syllabus long ago but continuing to tweak it a smidge every so often. I’ll post it in one of the upcoming blogs once I can figure out how to make a screen capture image.
The first day is mostly consumed with my (in?)famous exercise of finishing a 24″ x 48″ piece of birch plywood with a 1-inch brush, beginning the day’s activities with five or six coats of 1-1/2 lb shellac. (sorry, I forgot to take pics of this step)
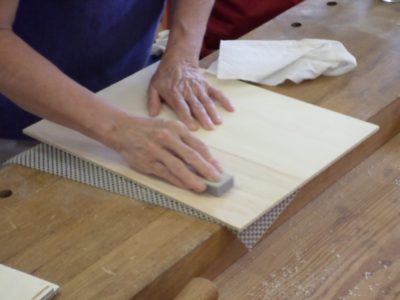
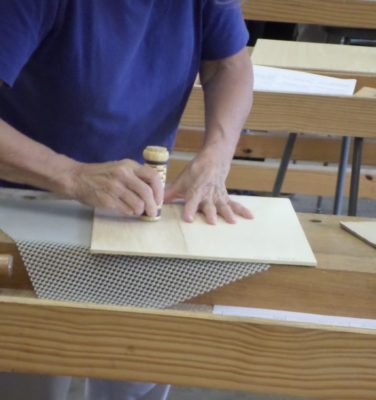
This is followed in short order with exercises in using pumice blocks to “sand” the surfaces, polissoirs to burnish the surface, and a generous application of molten beeswax.

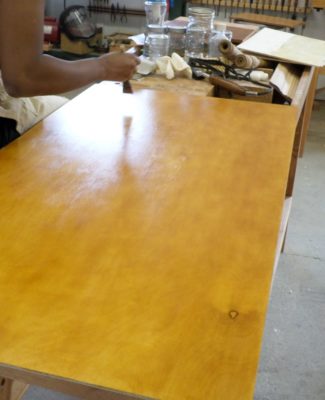

Late in the afternoon the big panels are sanded lightly to remove any fuzz or debris, followed by another five or six coats of the same shellac.


The day was completed with some wax scraping, partly in preparation for processes yet to come.
For the past three weeks I’ve been spending all my available shop time preparing for next week’s Introduction to Historic Woodfinishing workshop over the mountains at Joshua Farnsworth’s Wood and Shop school. If you have ever traveled to teach a workshop you know how involved it can be to assemble and pack all the requisite supplies and syllabus exercises for each student, all the more complicated since you won’t be “at home” and could go into the next room for anything you forgot to have set out.
Workpieces for a dozen exercises, brushes, resins, waxes, polissoirs, solvents, abrasives, scrapers, rags of a dozen different types, cases of jars, etc,, etc., etc. I have not counted them precisely but at this point I would guess I am closing in on 20 bins of materials. Were I so inclined I could create a giant artistic collage in the driveway and crank up Set The Controls For The Heart of The Sun. Unless you are of a certain vintage that last reference is probably just gibberish.

While I have made headway in my battles to find acceptable and affordable plywood to use as exercise workpieces, not great but better (good plywood for class exercises would raise the per-pupil materials cost to well over $200 instead of the ~$75 it is now) so instead this time I grabbed some pieces of mahogany and cherry from my stashes of “pieces too small to really make stuff from” and resawed and planed them so each student could have at least some of each. Pad polishing on inferior plywood just doesn’t cut it.

Tomorrow after church I will load my pickup to the gunwales and head back into civilization to set up, then begin teaching at 9AM Monday.
One of the problems(?) of teaching workshops is that I often get so involved that I fail to take adequate pictures of the goings on. In the case of the recent wood finishing workshop at the barn I failed to take a single picture, but student Pat took some with her phone and forwarded them on to me. So, with gratitude to her I present them to you.

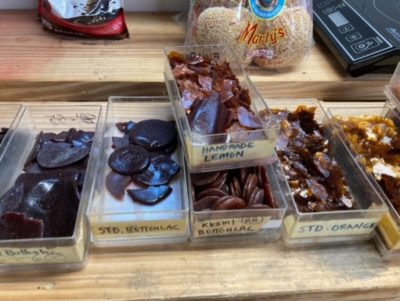
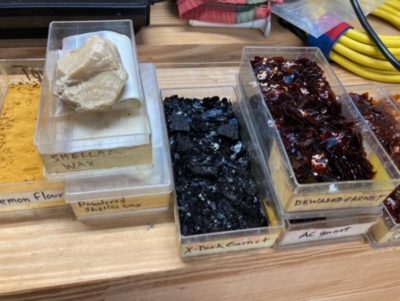

Like almost all those who encounter my collection of shellacs, she was captivated. How could you not be?

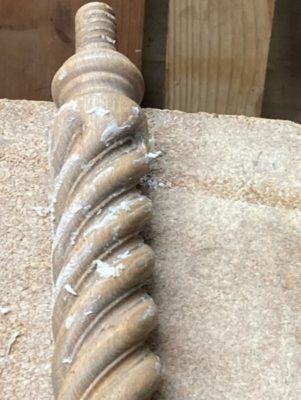
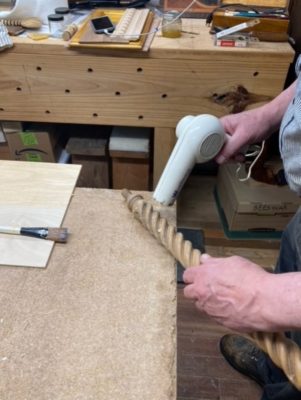
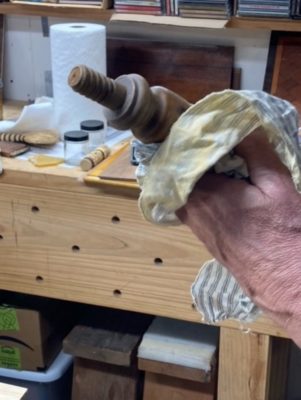

One of my demonstrations was cold rubbing wax onto undulating surfaces, then dispersing said wax by melting it with a hair dryer and buffing it with a rag. (Historically the wax melting would have been accomplished by passing a hot iron over the surface) The result is, to my senses, a pleasing one.
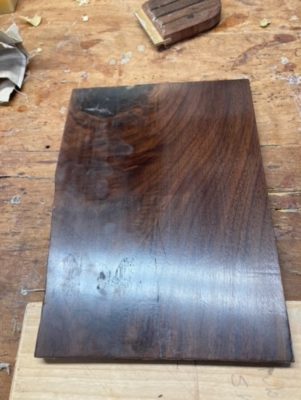

Here is her walnut panel in the early stages of pad polishing, a/k/a/ “French polishing.” The molten wax grain filling has been completed and the first pass of a loaded shellac pad has been applied.

One of the most effective exercises in the workshop is building up an excellent shellac finish on a 24″ x 48″ plywood panel with a 1″ brush, then polishing out each quarter with differing abrasive/wax regimens.
Yesterday brought the close of the Workshop Era at the Barn on White Run, due to my previously recounted business insurance cancellation. We had a grand time working in the world of historic finishing.

The students undertook my now pretty-much-locked-in-stone curriculum for the three-day class, a syllabus I settled on many years ago. It involved lots of surface preparation with pumice blocks and polissoirs, brushing shellac varnish, melting beeswax, scraping, pad polishing, rubbing out, and making some hand-made sandpaper.
I believe a good time was had by all, with much learning, fears overcome, and confidence instilled. The results are a feast for the senses.
I will be teaching the same workshop in a few weeks over in the Charlottesville area at Wood and Shop.
Recent Comments