Ninety miles from the Studley-era piano maker’s workbench was the finest Studley-inspired tool cabinet I have seen. No, it wasn’t Studley, nothing else is, and it is not yet finished as there are still many tools destined for it, but I cannot imagine any serious woodworker not wanting this hanging on the wall above their bench.
The maker is a tremendously skilled fellow whose other projects revealed that like Studley, he enjoyed making intricate and complex things.
Oh, and all the screws are clocked. He wouldn’t bite on my suggestion that this revealed he was anal-retentive/compulsive, he merely replied that it was attention to detail. He was a great sport about the whole thing, and I truly enjoyed my time with him and hope he will make it to the exhibit next spring.
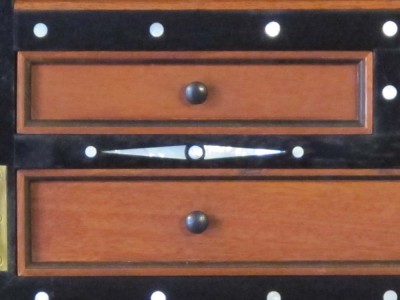
Yup, it’ll be in the book too, in far greater detail and length.
Back home now, and finishing the first rough draft of the whole book tomorrow!
This will be our first full winter in the Virginia Highlands, where it gets “upstate New York cold.” For the past few weeks the sound of chainsaws and log splitters has been a constant drone in the background of the valley atmosphere, as the locals are getting ready for intense global cooling. Me too. In addition to the firewood already stacked in the storage shed next to the cabin, other piles of split wood are growing around the homestead.
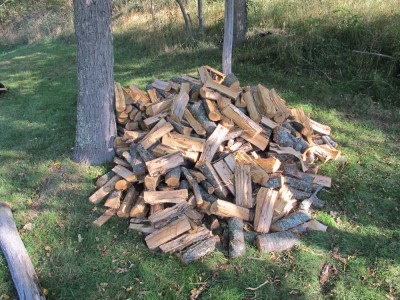
Last winter was perhaps the coldest in a century here, and the woolly worms, walnut trees, and Farmer’s Almanac are all projecting an even colder winter this time around.
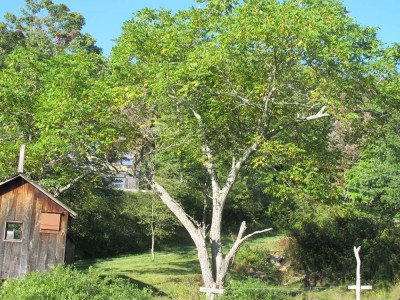
Walnut trees? Yep, by mid August they were already turning yellow and the leaves are now falling in a constant wave. Hence, concerns for an even worse winter. That would be pretty brutal, as at least on three occasions last winter the dusk to dawn temperature here in the holler was 20 degrees below zero.
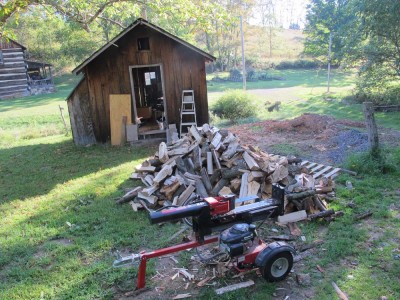
Given the cold-nature of my bride the need for firewood and lots of it is riding high at the moment. Yesterday was one of those times when I hunted and gathered firewood. In the morning I went to my friend Mike’s farm and he cut down two trees, one maple and one beech and helped me load my truck to the gills. I’ve never bottomed-out my 4WD s10 before, but it was yesterday.
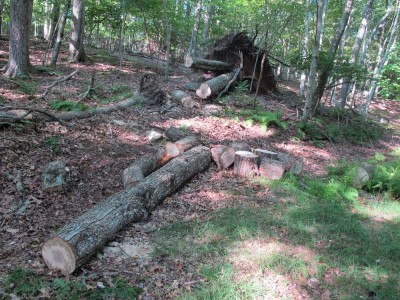
When I finished splitting that (our altitude lets split wood dry really fast!) I went up the hill to work on a giant maple that fell last winter. So far it has yielded two truck loads and will probably get another two by the time it is all done. For scale, the log on the ground is 16″ by about 15 feet long, and the larger of the two trunks still on the root ball is about 24″. It’s stretching my 14″ Stihl chainsaw to the limit. It might be time to get another, larger one. But for now as long as I keep the chain sharp it is doing okay.
How much wood do we need to keep the home fires burning non-stop for five-plus months? We will find out, but the other night at Bible Study one of the fellows indicated that he had put up 19 cords of wood. I certainly hope he needs a lot more than we do. Otherwise I am only about 1/3 of the way there. Fortunately(?) I want to clear more space on the south side of the barn for more winter light, so a bunch of trees will be coming down next week.
Monday just after dawn I hit the road for a longish drive into the Heart of Dixie to see a workbench. The owner had contacted me through the Lost Art Press web site indicating he had a really fancy Studley-era piano makers work bench. So of course I had to go see it.
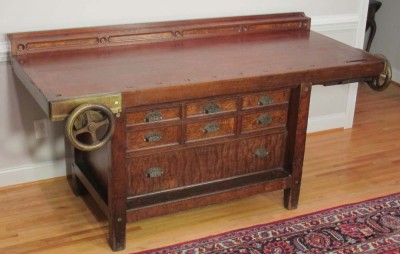
He was right. It was spectacular. Other than Studley’s, all the other piano maker’s benches I had seen were at least in part “store bought.” Not this one, it was all craftsman-made. By a mighty good craftsman.
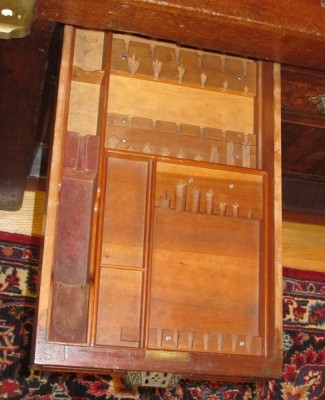
With its burled veneers on the drawers, delicate a whisper tight dovetails, superb cast drawer pulls, and the really neat tool rack, it was a work of art.
And yes, it will be featured in the book, in a Gallery of Piano-maker’s Benches.
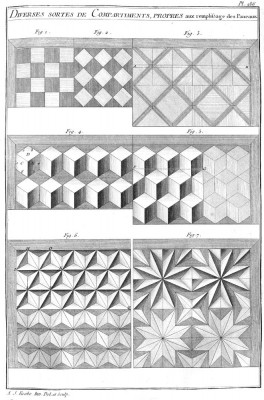
Once you have sawn a great pile of equilateral parallelograms with the jigs from the last post, you need to arrange them into the final pattern. Next post will go through the nuts and bolts of assembling a finished parquetry panel to adhere to a substrate, but for this post I want to diverge for just a few minutes and talk about the pattern layout itself. I feel justified in doing this because I have yet to teach a workshop where everyone does not make some layout mistake that has to be undone, often with great damage to the glued up pattern or at the very least loss of a lot of time and a raised level of frustration.
The key is to remember that in most instances, this exercise included PARQUETRY IS A REPEATED PATTERN. In fact, this simplest exercise is really about a dozen patterns superimposed on each other, and you must be mindful of their construction in order to avoid catastrophic mistakes that might deter you from finishing or continuing.
The pattern Roubo illustrates in the plate above, Figures 4 and 5, is simple and to my aesthetic taste, garish. I prefer to adapt it to my own preferences by using all the same wood for all the lozenges, and establish the shimmering pattern only through the changing grain patterns of the lozenges via laying them out.

The simplest unit of the design is the cubic die. It is repeated ad infinitum until the panel is complete.
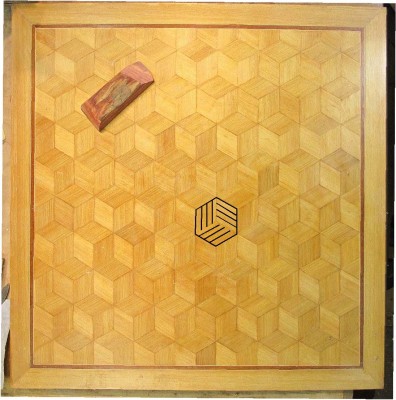
All you have to do is make sure you lay out each and every one of them with the grain pattern like this.
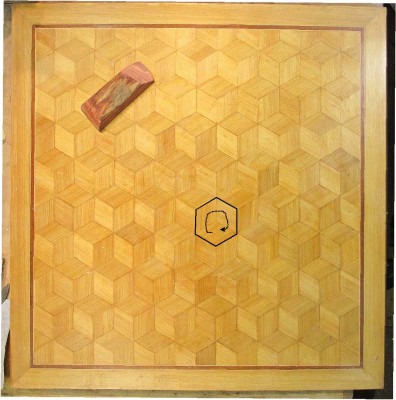
Or perhaps more simply, just remember to make it a whorl like this. But in truth, this is like George Costanza getting hypnotized by a poster on the wall of the bathroom. Hopefully you do not proceed only partially robed.
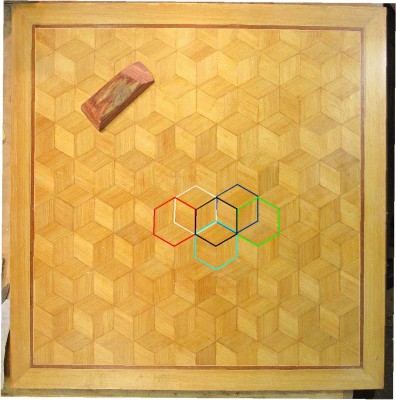
Such would be the risk when you realized suddenly that the dice overlap each other, and your eyes start to spin around. Let’s see if there are other approaches that might help.
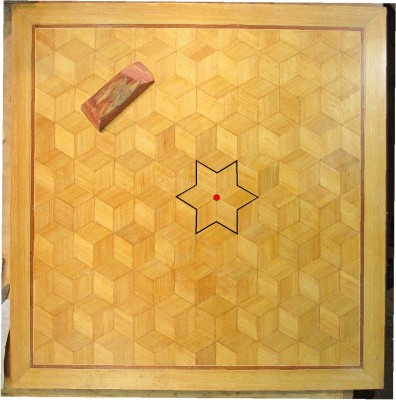
Another, second set of patterns is the pinwheel with a center point.
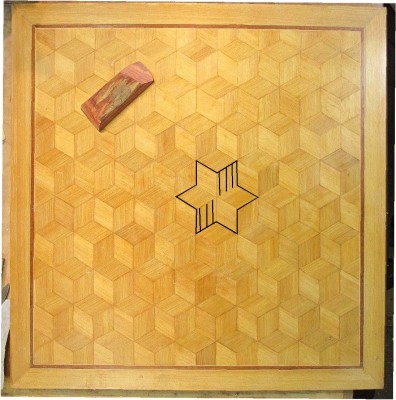
They are simple to lay out, just make sure that each opposing pair of lozenges is aligned to each other and the overall pattern. Like this,
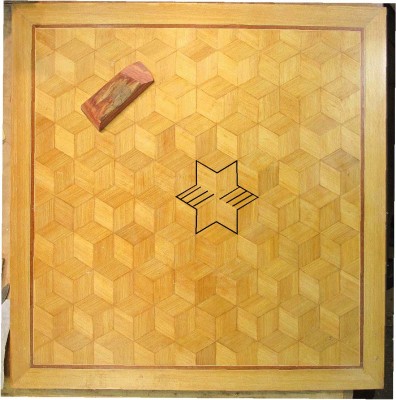
and this,

and this.

Unfortunately, the pinwheels also overlap each otherand there is the risk of visual confusion. Arrrrgh!
There are a third set of simultaneous patterns at work on the panel that are easy to keep in mind, running always in the background like a security system on your computer. It is the most straightforward pattern set, and this is often where I begin, laying out a horizontal row of lozenges tip-to-tip, each with the same grain orientation.
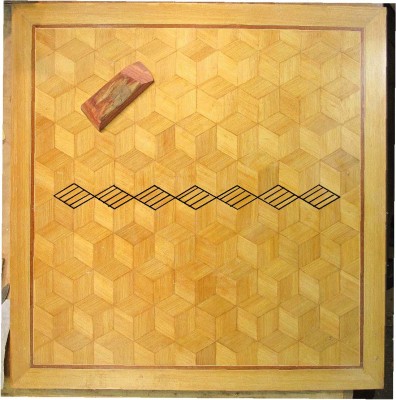
But, since we are working with a six-sided form, there are two additional complimentary patterns identical to the first one, each of these two off-set by 60-degrees.
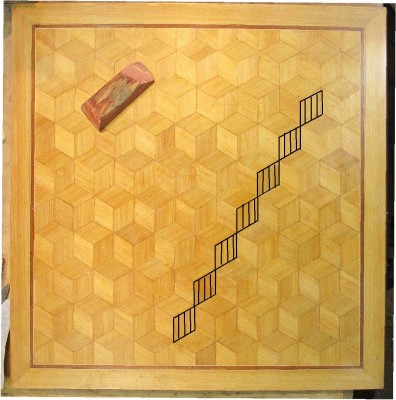
Like this,
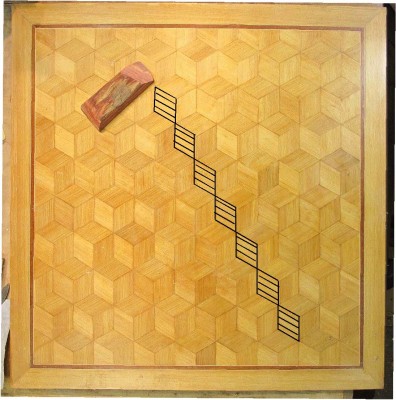
and this.
So, you can see the advantages of thinking about complex complimentary rows.
If you keep all these things in mind while you are assembling your panel, success is at hand.
An announcement from Jameel Abraham at Benchcrafted.
The arrangements have been made. Contracts signed. Wood procured. We’ve even struck a deal with the local meteorologist to all but guarantee comfortable weather.
The French Oak Roubo Project will happen again the week of November 8-14, 2015.
We’ve been working out many details over the summer and can say with assurance the following:
1. The original crew will be back. Chris Schwarz, Don Williams, Raney Nelson, Jeff Miller, Ron Brese, Will Myers, and Jon Fiant will all be back. Of course Bo and I will also be there, although I can’t promise you won’t find us fishing in one of Bo’s ponds for lunker bass.
2. We’re making room for more. There are eight benches in Plate 11. Since this is FORP II we’re going to double that. We’ll have 16 spots available for participants. We actually built 16 benches last time around, but this time the original crew will work on everyone’s benches, in the hopes of getting more accomplished during the week.
3. Another huge bench. Bo complains that one 16′ Plate 11 bench isn’t enough (some people!) So we’ll try to build another one for him while we’re there. We had loads of fun getting Bo’s bench put together last time. Lowering the top onto the base with the fork truck was thrilling on the last day. I want to duplicate that.
4. Schwarz will talk Sunday night during a meet and greet about bench history, the art of the green bean casserole, and how to live without a modern sewage system. There will be refreshments (no casseroles though.)
5. Lunch. Catered lunch everyday from a local chef who studied in France and at the CIA (the other CIA.) Some of you might end up staying at her B&B. Excellent. We may also break out the grills in the evening if we feel up to it.
6. Hardware from Benchcrafted, Lake Erie Toolworks, and Peter Ross. Same as last time.
7. Personalized letterpress labels from Wesley Tanner
8. Pig Candy.
As for price, it will be a little more. Some of our costs have gone up in the past couple years. It won’t be a deal breaker for anyone, promise.
We’ll open registration on Tuesday, September 2 at 10am CST (we’ll do a blog post then to announce.) To register you’ll simply send an email to jameel@benchcrafted.com saying “I’m in” and we’ll send you all the nitty gritty. To be fair, it will be first-come, first-served only.
Periodically to take a break from sitting and writing, I get out of the recliner and hike up the hill to spend a little time puttering in the barn. I am getting much faster at writing over time — I penned the thousand-word introductory essay for the new l’Art du Menuisier: The Book of Plates in about two hours, but still it is simltaneously exhilarating and tedious. Since I know I have to get back to work to stay on track, my times in the barn are short and the activities brief and episodic for several more days.
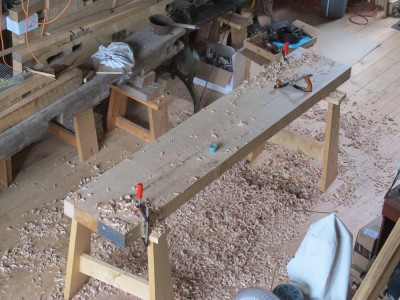
In addition to periodically loading the solar wax melter to purify more beeswax I grab a scrub plane to continue the flattening of a maple slab I glued up several winters ago. It is destined in short order to become a Roubo-hybrid bench in my barn studio, perhaps even under the east bank of windows. The “hybridization” of the bench will be in the form of another Emmert K1 vise, a tool I consider unsurpassed in the bench world.
The 18″-wide maple slab was out-of-flat by more than a quarter inch and I do not own a power planer that large and the darned thing is just too heavy to take to a friend’s shop where a planer that large sits. A few minutes of scrubbing here and a few minutes of scrubbing there adds up, and now the slab is flat enough to start laying out the legs.

Ten feet away my old Roubo bench I built for my conservation studio at the Smithsonian, where the climate control was perfect all theim time, developed a 1/2″(!) crown once I moved it to the unregulated environment on the south side of the barn. I will also will be taking a whack at that as a vigorously physical respite from writing.
Another fortnight or less and the first draft of VIRTUOSO will be done.
… but certainly blogging quietness.
I’m in the midst of the critical phase where I am weaving the final threads and honing the organization of the VIRTUOSO manuscript. I spent yesterday and today working into the night on the chapter on Studley himself and the winding path the ensemble took to arrive to us today.
That means I have completed the first draft of the introduction, the biography and provenance, the tool inventory with commentary (well, mostly, I have some questions to answer with the microscope in a couple of months), the chapter on the bench and vises is more than half done, the section on Studley’s Masonic heritage is due in a day or two from Spider Johnson, I have a good start on the woodworking-popular-culture chapter, and the conclusion is finished.
I hope to have the first draft complete enough in a week or so that I can send it to Narayan so we can start 1) picking out the mere multitude of pictures from the book from among the bazillion we have, and 2) outline the photographic and informational needs we have for the upcoming final trip.
Stay tuend.
I’ve been able to build up my inventory of raw beeswax enough to begin planning for processing it by the boat load for sale as 1/4 lb blocks, and to use in the making of Mel’s Wax. In the past I’ve done processing with a variety of electrical cookers, CrockPots and the like, but I wanted to try something else.
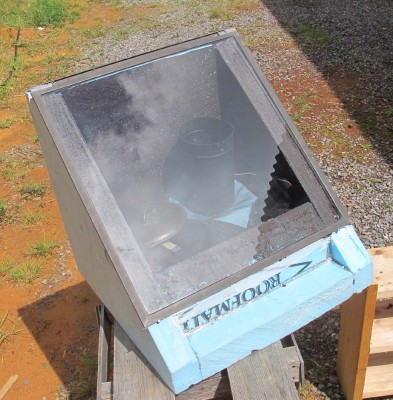
Following the copious information on the internet — and if it is on the internet it MUST be true — early last week I built a fairly typical solar oven to give it a try. Using some of the scrap 3″ XPS rigid foam insulation I’ve got laying around along with a glass panel from a long-dead storm door and some construction adhesive, I built a prototype to give it a try and see if it worked.
Boy howdy, did it ever work.
I took my remote sensor for the thermometer (it’s the unit I place out in the unheated part of the barn to tell me when I am inside the heated part how cold it is “out there”) and placed it inside the solar oven. Before long the interior temperatures were 130F, 140F, 150F. I set up a wax batch and it melted in less than 90 minutes, not a whole lot slower than I would get starting from cold with a Crock Pot. Plus, since the entire volume is at the same temperature the wax flows through the filter much more easily.
I filtered the raw wax through metal window screen to get out the bug parts then a disposable shop towel for tiny particulates, and let it drip into a pan of water to dissolve out any remaining honey or propolis. The resulting wax is beautiful, ready for remelting and casting into rubber molds.
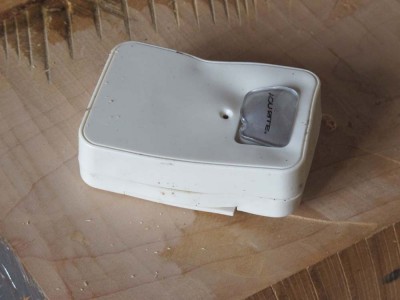
Last Tuesday the sun was bright and mostly uninterrupted. My peak temp was 162F, which was hot enough to not only melt the wax easily but also melt the case of the sensor unit and actually the solar oven began to melt itself! Clearly the XPS was not the ultimate answer.
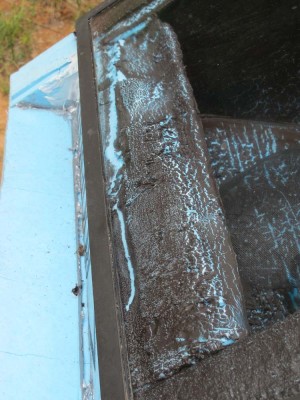
I grabbed some 2″ foil faced polyurethane sheet insulation and built another one. That should do it. If not, I’ll switch to foil faced fiberboard insulation, but the idea is definitely solid. From now on I expect that every bright sunny day will find the solar wax purifier hard at work.
Now I just have to wait for a warm sunny day. It’s been grey and cold(!) the last several days, but I have hope for this afternoon.
Stay tuned.

It’s hard to believe that Woodworking in America 2014 is only a month away!
Once again I am honored to be a presenter. My main frustration is that there are so many great presenters that I will be unable to see nearly as much as I want.
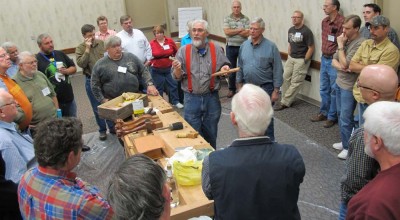
On Friday afternoon I have the remarkable luxury of having four solid hours to talk about and demonstrate historic finishing. I have presented this at WIA several times before and it always seems to be a crowd-pleaser.

Last year the audience was especially enthusiastic; the facilities crew tossed us out sometime close to 7PM.
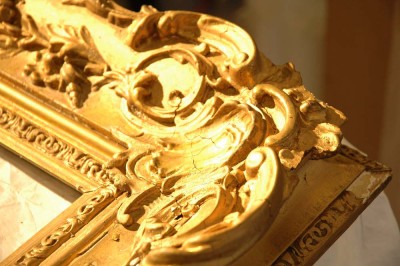
Then, mid-day Saturday will be a new WIA topic for me, Gilding. I don’t do much large scale gold leafing anymore, but I do use it a fair bit in my japanning work.
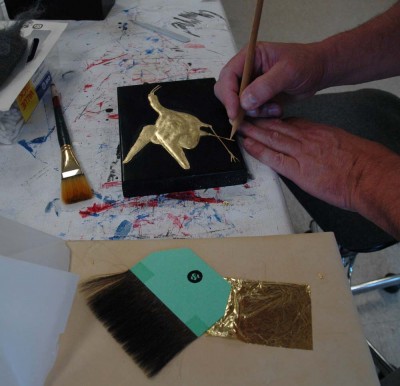
I hope to see you there.
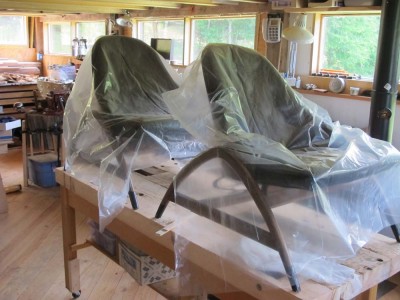
After a lengthy hiatus due mostly to the upheavals of moving, writing several books simultaneously, planning and hosting a gathering of fifty people at The Barn…, I am resuming my practice of conserving furniture and decorative arts, with the primary activities now being conducted in The Barn.
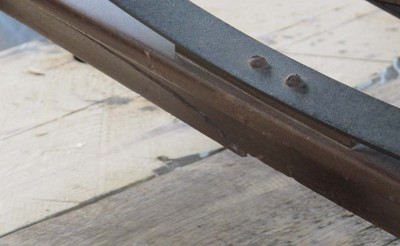
With likely projects including a pair of mid-century modern chairs, 19th Century tortoiseshell boxes, an 18th century long rifle, a 17th century Italian sculpture, a pair of mirror frames., a 19th century gilded French clock… I expect to be busier than ever soon enough even though R2 is off to editing and out of my consciousness for a moment and the Studley manscript will be off my plate in about three months.
Provided my clients give their consent, I will be posting about these in-studio projects as they unfold.
Recent Comments