Been Lookin’ For This
One of the thrills of incursions into the Evilgoogle Empire via the satellite of Youtube is coming across an instructional or demonstration video that was at the very least unexpected or unknown. Sometimes it is the result of a long search, that search can be keyword or descriptor directed. But when the subject and title are not English or even Western alphabet but rather Eastern in character it becomes a matter of sheer luck as YouTube cycles through videos of related topics for referral. Sometimes it leads to new videos, sometimes it leads to videos posted years ago that I had no way to know existed such as this one linked below.
For the most part urushi lacquerwork is applied to a wooden substrate, either wooden boxes or trays or turned bowls, with the occasional foray into furniture pieces, for example in the work of Gonroku Matsuda.
For I’ve long been searching for video about a peculiar lacquerwork technique that fascinates me, the analog to sculptural papier mache’, using urushi instead of oil or paste to assemble the creation. I have long held this candy dish (above) to be one of the most beautiful objets d’art I have ever seen, unfortunately not in person. It was made with this urushi-laminate technique, albeit using fine linen cloth instead of paper. Classically this method involves draping urushi impregnated fabric (or paper) over a previously sculpted (unfired?) terra cotta core, then excavating the terra cotta once the form is achieved.
The technique demonstrated in this video uses sculpting clay and plaster for moldmaking steps in a manner I find both fascinating and fully do-able.
A Housekeeping Treasure (?)
A component of my routine in the shop these days is surveying, sorting, and dispensing of the tools laying here, there, and everywhere. Now that I am in my 70th year and have two handy sons-in-law and soon to be two grandsons I am either dispensing or dispersing many of the tools immediately or presumptively. Genuine tool sets for L’il T and the soon-to-come Baby T (for Baby Tyrannosaurus, the moniker for L’il T’s baby brother in utero, I suspect the final name will be different) are well underway.
One of the treasures(?) I came across was yet another infill plane, a truly challenging project for the future. As near as I can tell none of the adjunct components belong together with the original chassis so I can assume great latitude in the restoration of the tool. It’s raggedy but solid, so the end result should be solid but less raggedy once I get around to bringing it back to life.
Phenomenological Elucidation
I spent a day steam bending the conditioned dry wood with very instructive results. Not success, per se, but definitely instructive about the pathway to success.
I’ll backtrack to review the protocols for conditioning the dry wood.
Using some PVC from the stash I made three 40-inch-long tubes into which I placed two serpentine pieces, two arm pieces, two uni-splats, and two rear legs from the mini-Gragg. In the first one I created a 1% surfactant solution with distilled water, in the second a 1% ethanol solution with distilled water, and the third was a 1% fabric softener solution with distilled water. All pieces were fully submerged for the duration.
I let these sit for seven days and fired up the steamer.
To accentuate any effect of the conditioning I steamed the pieces for 1-1/2 times longer than might be expected for steaming green-ish wood, then bent them as quickly as possible. This meant 30 seconds of intensity after 35 minutes of steaming for the thinner components, and 75 minutes for the rear legs.
The results were instructive but not particularly encouraging for the extremely bent pieces, namely the arms and serpentines. That said I could definitely feel a differences, it just wasn’t enough for complete success.
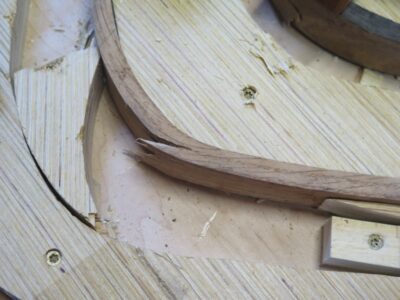
Somehow, I missed this excessive run-out on the side when I was toothing the faces. This piece was never a good candidate under any circumstances.
In each protocol the uni-splats worked almost perfectly, with the only failure being due to a wood grain flaw that I somehow missed during the preparations.
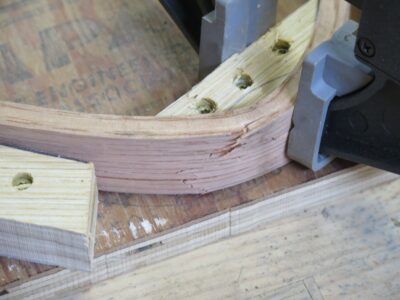
This bend was “this close” to making a successful bend, but at the final instant let loose with enough tension to break. It is possible that this piece could be salvaged with epoxy impregnation.
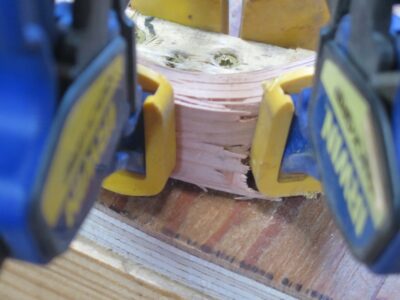
This one busted right away…
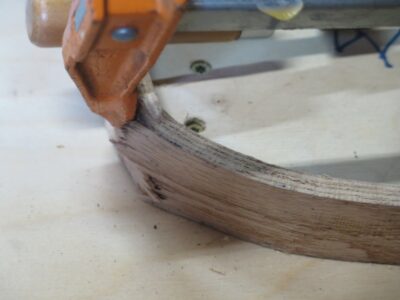
… while this one flat out ‘sploded.
In bending the twelve extreme pieces – 6 arms, 6 serpentines – the failure rate was 100%. The pieces felt very plastic, bending nicely until an instantaneous catastrophic failure. It was abundantly clear that the fabric softener worked the best of all the conditioning approaches.
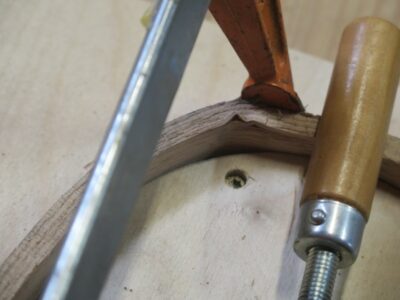
I did have one instance of compression buckling. Why this one? I got no idea.
The takeaways were indisputable and I will tinker with these further. 1) use fabric softener to condition the wood, and 2) the serpentine and arm configurations cannot be accomplished without compression straps. For the full-size Graggs I have used plumbers straps screwed to the bending stock but for these I will make compression straps from aluminum flashing, then tack them with aluminum tacks to the stock prior to inserting the pieces into the steamer. That way when the wood is cooked I can remove them and bend them instantly. The reason I am taking this approach is that I need for the compression straps to be exactly the width of the bent element and plumbers straps are narrower than the components. And, I do not need to keep the surfaces of the bent elements pristine since they will be painted once the chair is assembled and thus any tack holes will be filled with primer.
Stay tuned as I dive in again.
Recent Comments