Yesterday brought the close of the Workshop Era at the Barn on White Run, due to my previously recounted business insurance cancellation. We had a grand time working in the world of historic finishing.

The students undertook my now pretty-much-locked-in-stone curriculum for the three-day class, a syllabus I settled on many years ago. It involved lots of surface preparation with pumice blocks and polissoirs, brushing shellac varnish, melting beeswax, scraping, pad polishing, rubbing out, and making some hand-made sandpaper.
I believe a good time was had by all, with much learning, fears overcome, and confidence instilled. The results are a feast for the senses.
I will be teaching the same workshop in a few weeks over in the Charlottesville area at Wood and Shop.
It’s been a while so I thought I’d take a minute to catch up on the doings at donsbarn.com/shop, the product page of the undertaking (all of this — blog, writings, and store — are an amusement/ hobby).
I have enacted a slight increase on some of the pricing to reflect my increased costs for both the polissoirs but mostly for postage. Those changes are already now in place or will be very shortly. If these modest increases make my products un-sellable, that information feedback loop will be instructive to me to discontinue the enterprise. I hope that is not the case but the future will tell.


The product line itself will remain unchanged for the moment until I can get some new things finished (see below). NB: for those of you who care about and base your purchases on such things, my products are provided by hetero-normative cis-gendered folks of European ancestry and hillbilly inclinations; we use brown polyester or tan linen bindings on the polissoirs based on my original work with the Roubo translation project (I do not deal in the books themselves, you can get them directly from Lost Art Press), non-recycled paper and standard printer ink for the labels. I am resolutely idiosyncratic/redneckian in every aspect of my life, and if that disturbs you, well, I cannot fix that issue.

The beeswax is commercially obtained as raw wax (I’ve been told the slang term of art for what I buy is “slum gum”) which is then hand process purified. All the bees involved in the production are now dead; the bodies for a great many of them are part of the contaminant that must be removed. The shellac wax is obtained directly from a purifier in India. Mrs. Barn and I (42 years this summer!) do 100% of the wax product purifying, formulating and packaging. I have received several requests to create some paste waxes of differing formulations and I am doing some explorations of that.
I think I have solved the problem I was having with Mel’s Wax, the archival furniture care polish we invented at the Smithsonian (Mel was my friend and co-worker who is the patent holder), and that may be available for purchase in the immediate future. Stay tuned on that one. I still won’t ship it to California. At one time I thought it would be the cornerstone for my post-retirement activities, but it never caught on.
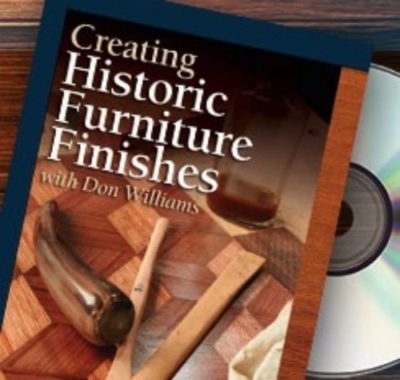
Until now the videos have been purchased wholesale from the folks who made them at Popular Woodworking, but they no longer produce physical DVDs. They are strictly a streaming platform from whom you can obtain the video directly. However, with their permission we will begin the production of the physical DVDs for sale and mailing. That endeavor is imminent, I just have to forward a couple of graphics files to Webmeister Tim who will be doing the actual DVD burning and packaging. Good thing on that as at the moment I am out of the Wood Finishing video.

Another video undertaking is to finally wrap up the editing of the “Make A Gragg Chair” video (I now know why there is an Academy Award for movie editing), and to finally get some videos up on a Youtube page. I have several, from presentations I have made over the years, and hope to begin shooting some less formal shop videos once I get a handle on the whole process with the help of videographer Chris, who is so busy I may have to execute the filming and production process without him. I am also working on a set of full-scale drawings of the chair for sale on the site.
If you come to Handworks please stop by to visit. The booth will have lots of stuff.
For the home stretch of the jam-packed three-day workshop the final set of exercises involved the giant panel. It had already served its first purpose, getting the students comfortable with laying down an exquisite brushed shellac surface over a large area. Since the panels were roughly half the size of a dining table, I’m thinking any hurdles of intimidation have been overcome.
At this point the panel was subdivided into four quadrants, each of them to be treated in a unique manner. The first quarter was easy — just leave it alone as an example of laying down an excellent base of three-inning shellac.

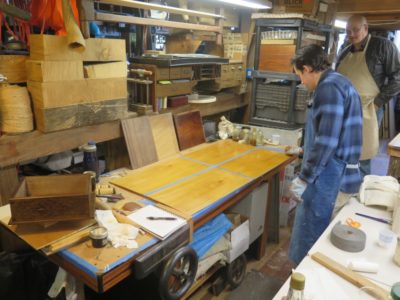
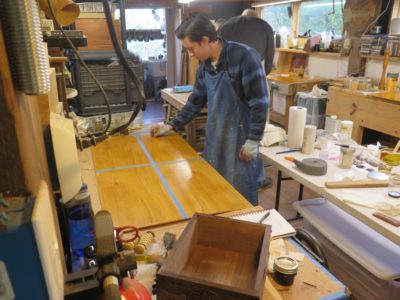
A second quarter was spirit varnish pad polished to a high sheen, demonstrating the option of creating a not-grain-filled padded surface.

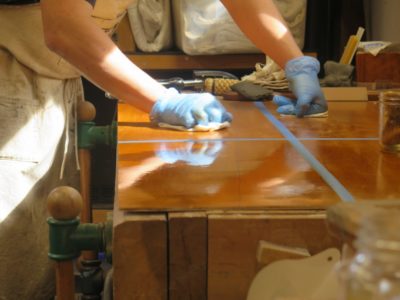
The third quarter was hand polished with abrasive powders, first 4F pumice then rottenstone in mineral oil, using a polishing pad identical to the spirit varnishing pad. This was followed by a light application of paste wax and buffed when the wax was firm.

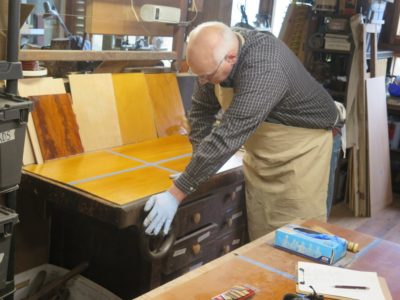


The final quarter was burnished with Liberon 0000 steel wool saturated with paste wax, and as with the rottenstone polishing, rubbed until you just get tired. When the paste wax was firm ex poste it was buffed with flannel to a brilliant glow.
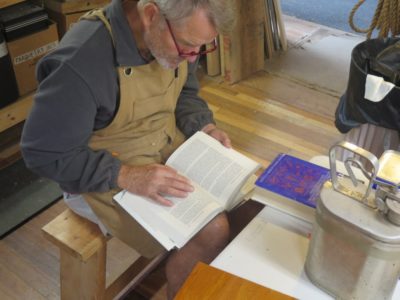
As always there is at least one somebody who gets seduced by my library.

When we wrapped up the event it was clear that they had all mastered the techniques wonderfully, and departed with confidence and a set of sample boards to guide and inspire them for decades to come.
If scheduling a workshop identical to the one these fellows completed, drop me a note. I will no longer “schedule” any workshops but only host them on request.

The next world changer to emerge from the mists of the far distant past was to equip each student with a 1-inch polissoir and turn them loose burnishing the surface of smaller sample panels. The instructions were to press as hard as they could and rub with the grain until the entire board had an even sheen.
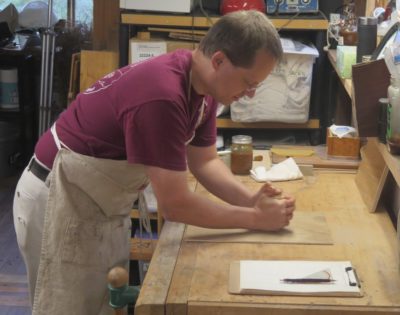
They did this to two panels; they set the first aside then scrubbed the second one with cold beeswax before wailing away on it with the polissoir, rubbing hard enough to turn the wax buttery and press it down into the grain interstices.
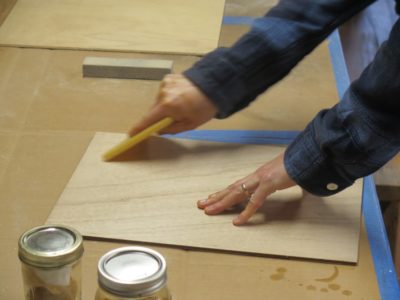
This was followed by second round of polissoir rubbing, followed by scraping off the excess and buffing out the final surface. Though this technique was often used simply for filling the grain, in this case I just had them remove the excess with a Roubo-esque scraper and then buff it out with a piece of linen.
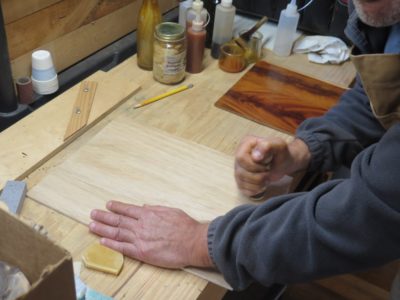
Even this simple exercise resulted in the first of many sumptuous surfaces for the weekend.

It was lovely.
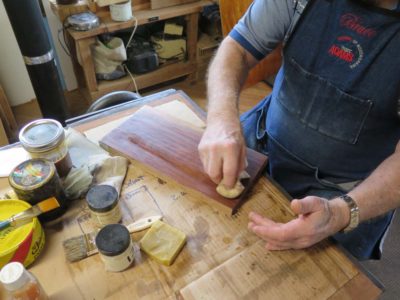
In keeping with my current “marketing” (non-) strategy for workshops, a while ago I was approached by a group of fellows commissioning a Historic Wood Finishing weekend workshop at The Barn. Once we set the schedule it turned out that there would be two slots open for anyone else who wanted to take the open places. If this interests you let me know. As always, the emphases will be on shellac and wax finishing for three days. The schedule for the workshop is October 9-11, 2021, and the tuition is $375.
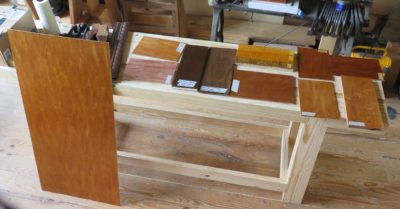
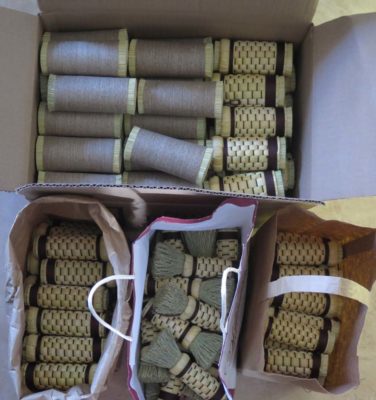
On my most recent visit to the Post Office to mail some family packages I was informed that they are no longer projecting packages to arrive before Christmas due to bottlenecks throughout the system. That’s good to know, so if you were planning on sending any of my wax or polissoirs for Christmas I can mail them immediately but do not expect to receive them before Dec 25th. Early December is the only time of the year where I regularly go to the post office more than once a week to mail packages.
Much to my surprise I made it to this date with a bit of my dwindling inventory remaining, I had my doubts. It’s been a few months since I received any new polissoirs since my broom maker has been dealing with some serious health issues and has not had the strength to sit and make brooms or polissoirs. At this point I am down to about a dozen of each model in stock (way fewer than in this picture). I’ve got plenty of wax blocks and can always process more, ditto Mel’s Wax.
I spoke to the broom maker last week and he is determined to get back into his shop this week. I hope it is true because that means his healing will be nearly complete. That will be great as we can start building excess inventory to prepare for Handworks 2021 on Labor Day weekend.

I am delighted to report that after a few weeks of being out of stock, as of ten minutes ago I am now replenished with Model 296 polissoirs and they will begin shipping again immediately.

Ditto the whisk brooms.
This is not a “happy” bog post. It might be a little too much “inside baseball” but I thought you should know what is going on and what is coming down the pike. It’s probably bad form to discuss openly the costs of running a business, even a hobby one, and I will give that concern all the consideration I think it deserves. Okay, I’m done with that consideration.
It has been almost a decade since rediscovering the amazing surface prep and finishing tool called the polissoir, or polisher, and connecting up with a local craft broom maker to supply me with them. In that period I have sold and shipped thousands(!) of polissoirs and blocks of beeswax etc., and I hope to continue that success and match it with that of Mel’s Wax in the coming months and years. I delight in sharing the polissoir-and-beeswax’s almost magical qualities with the enthusiasts who have joined me in this trek taking a giant leap backwards in wood finishing. To encourage these tools’ adoption by the woodworking world I have kept the pricing stable almost since the beginning, folding the postage into the purchase price and keeping that unchanged since we went “official” with the Shop function on the website.
Unfortunately the postage increases implemented by the USPO over the past two years have affected me to the degree that, all by itself, postage now consumes over 15% of my gross sales revenue (and nearly 25% of the net), a nearly 100% increase in just the past year. This is so far out of whack I can hardly wrap my head around it, but the unavoidable result is that some of the heavier items in the Store will necessarily increase in price to reflect this grim reality as soon as we can edit the page.
(I am not griping about the post office, they provide excellent service to me and are convenient; I do not realistically have any other parcel carrier option out here in the hinterlands. I usually make the five-minute drive to our one-window post office in town once a week with a canvas tool bag full of parcels to mail. Making a three-hour round trip over the mountains to a parcel depot is not in the cards for me.)
To respond to this new cost reality, after long thought I’ve decided to raise the price of hand refined beeswax by $1 to $14, raising the Blend 31 to $17, and the shellac wax to $21.
All three models of the one-inch polissoirs will remain at their current price since they are so light weight and have apparently — thus far — remained below some postage threshold, but you never know with the USPS.
The large polissoirs, the two-inch woven-sheath and the Model 296 wrapped polissoirs, will be going from $47 to $49, and the two-pound bag of shellac flour will now be $75. Postage for Mel’s Wax is also 50% higher per unit than expected but I will leave that price alone for now as a strategic move.
I’m not apologizing for the increases: even though this is a labor of love for me I simply can’t keep selling and shipping products at the previous prices given the rising costs of postage. That is just a plain and simple fact whether I like it or not. I will be sad if these price increases diminish interest in polissoirs and waxes and such, but as the pundit says, “Facts don’t care about your feelings.”
And, given the recent disruptions in the bee hive health I am doubly glad I bought a lot of raw beeswax for us to hand-process into blocks and polishes just before the colony collapse crisis. I’m hoping that the raw material comes back down in price before I need to buy more at the end of this year, but at the moment the prices for beeswax are about double from when I bought some last.
Stay tuned and wish me luck.
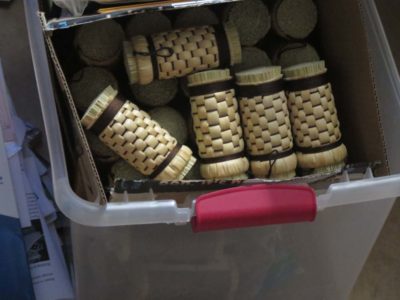
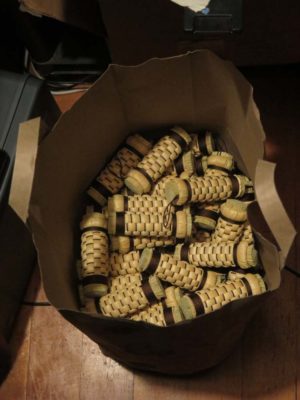
For the past several months just as I have been working feverishly on re-siding my daughter’s house my polissoirs maker has been concentrating on wrapping up his several years’ project building their dream house. They have been moving in recent days, but the broom-making studio is not yet fully installed in the new house, As a result the stream of new polissoirs dried up, and for the past couple of months at least I have been out of some inventory. I am happy to report that as of yesterday I am now fully stocked with all the varieties of polissoirs, with the routine of making new ones back on track. For the next several months we will be building the inventory for next year’s Handworks.
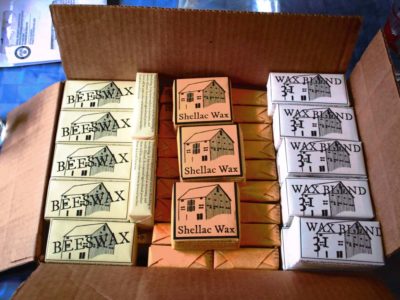
In addition I got the guy who makes the blocks of specialty waxes (that would be me) to get on the stick and re-stock them and Mel’s Wax as well.
I will be spending the next couple of days filling and shipping all the orders I have outstanding, and should be caught up by Thursday. I’ve got a couple trips over the mountains in the meantime or I would get them done tomorrow.

For several months my broom maker has been up to his eyeballs in alligators as 1) his brooms have been selling like hotcakes and 2) he’s been finishing building their dream house on the family farm. As a result my inventory was low at first then gone altogether. Last week I got an infusion of polissoirs so I can now fill my back-orders, which will ship out tomorrow.
Recent Comments