Exactly ten years ago I was experiencing the most exhilarating and exhausting week of my life, the culmination of years of research, writing, and travel; it was Studley Exhibit Week.
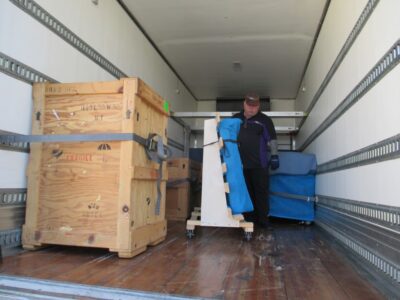
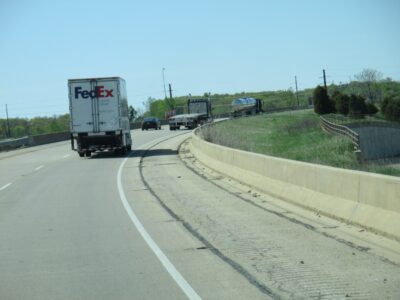
It started with packing up of the Studley Tool Cabinet and Workbench ensemble at its home, loading it onto a dedicated truck with armed driver and escort, and unloading it at the end of a long day’s driving in Cedar Rapids, Iowa, just a few miles from the Handworks event in Amana.
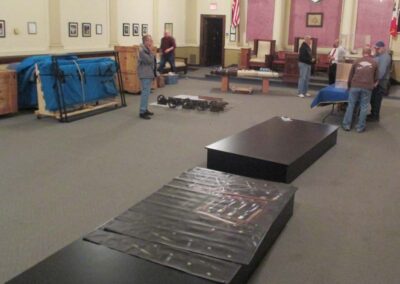
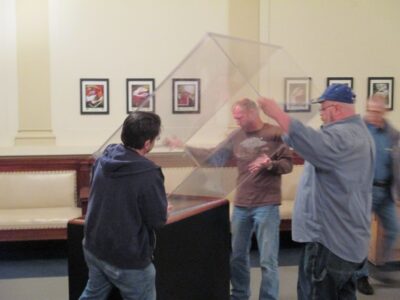
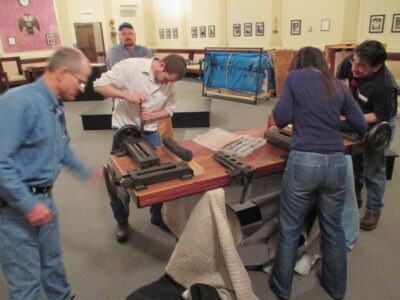
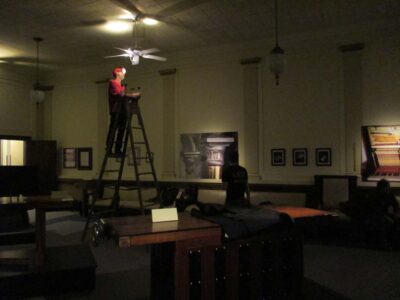
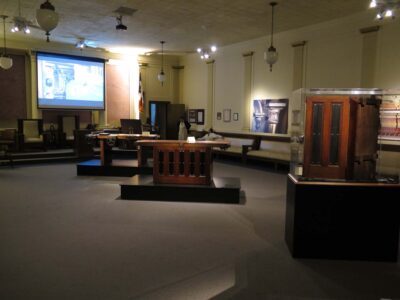
A dedicated team of volunteers (and vendors; the original lighting contractor bailed on the project three weeks before the opening) made the whole thing possible as the installation came together.
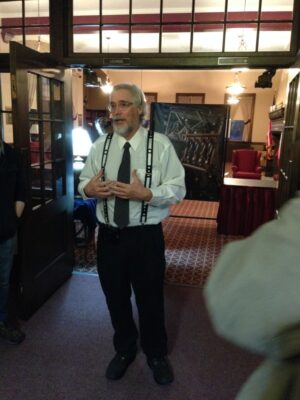
That evening I hosted a special reception for all the Handworks vendors who would be otherwise unable to see the exhibit.
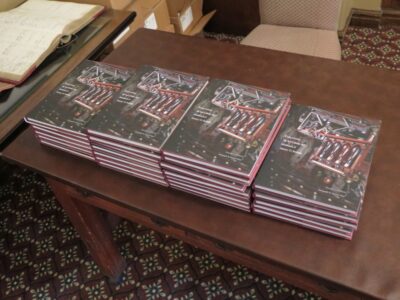
On top of everything else the Lost Art Press crew arrived with cases of the book, almost literally hot off the presses and straight from the bindery.
The event garnered favorable feedback except for those who were miffed that there was a ticket price for the small event. Apparently, they were unaware of budget items like the cost of dedicated, secured transport ($6k), insurance (a thousand dollars a day), facility rental, exhibit fabrication (almost $2k just for the tool cabinet exhibit case alone), and much, much more, all of which I was paying out of my own pocket. Thanks to the unbelievable generosity of a friend of the project the books all balanced in the end.
Despite the frenetic pace of those days, robbing me of many of the memorable moments, I still get warm-and-fuzzies reflecting on those moments I can remember.
Ten years! Goodness, how time flies.
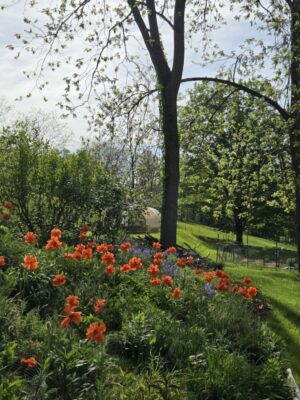
As I continue working on the multitude of details getting the greenhouse ready, Mrs. Barn’s flower garden, carved out of the rocky hillside next to the cabin, has erupted in an explosion of colors as the poppies have burst onto the scene. In a couple months the daylilies will emerge, and in between will be a host of other rainbows of flowers I know nothing about beyond appreciating their beauty. To say that she revels in the beauty of nature and especially flowers would be an understatement. Today is our annual Mrs. Barn’s Birthday Safari to Millmont Gardens to load up with beautiful plants. She has free reign to get whatever she wants, the space in the back of the CRV being the limiting factor.
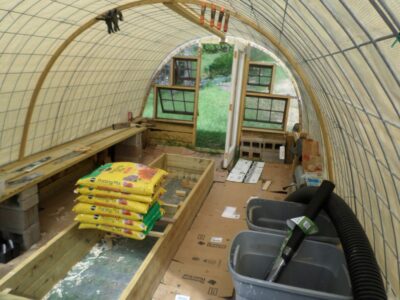
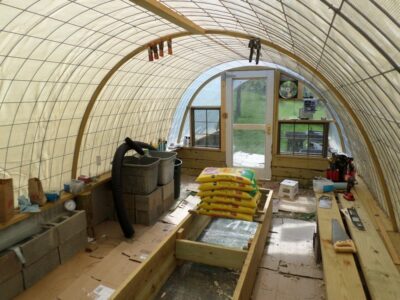
As for the greenhouse itself, we have begun to finalize the interior layout and some seedlings are underway. I have removed much of the construction supplies and tools, bringing a sense of order to the space. Lately we have been scouring the University of Youtube to garner the best information on building self-watering planters.

We have passed through asparagus season, having freshly-picked shoots with almost every meal for more than a fortnight. The bed is now proceeding to the “bush” phase and in short order the asparagus bushes will be 8-10 feet high. She says this is the key to an established perennial asparagus bed, and since it has worked here for two decades I rely on her judgement.

I can just now glimpse returning to the workbench on the horizon. First project is to make a new, sturdier cover for the hydro capturing trough that a bear (?) tore up last autumn.
The folks at The Babylon Bee did it again. When you contemplate the difficulty of consistently creating great satire in this clown-show world, you know these guys are the best.
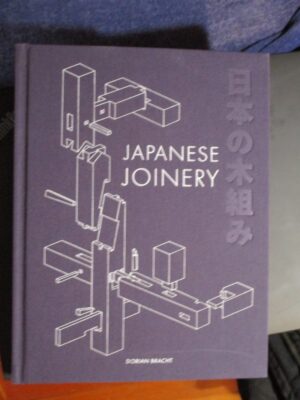
I have long been a fan of Dorian Bracht’s Youtube page, following as he makes mind blowing joinery exercises. Now his book is out and sitting on my pile of stuff to read, having arrived during our recent eon of travel or I would have taken it along to read. The time will come when I can spend time at the bench and reproduce his work. Unfortunately that time is not yet here.
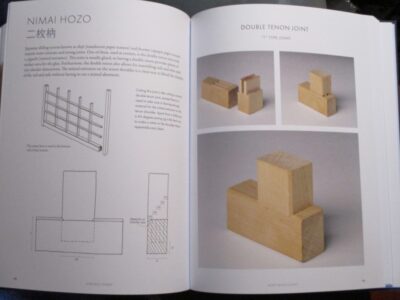
After what seems like a century we are back in Shangri-la, having logged thousands of miles in traveling for the past two months. We were home twice to swap out luggage but otherwise we were elsewhere.
It began with our arrival in DC for the very birthing day of Grandson #3. Three weeks later we went to Alabama for the third birthday of Grandson #1 and first birthday of Grandson#2. Then back to DC for GS#3’s baptism, a grand week we got to spend with our co-in-laws. My co-father-in-law and I are twin sons of different mothers.
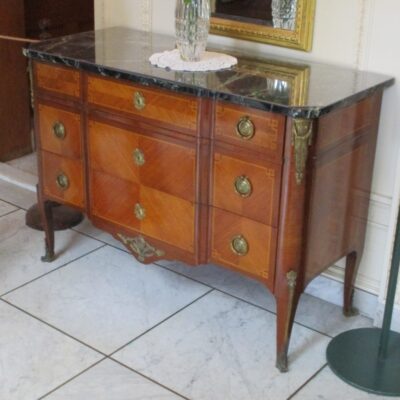
While in Rochester our hostswe squeezed in a visit to the Eastman House museum. This was a charming veneered French-style chest, although almost certainly late 19th or early 20th century (I did not take it apart to confirm that thought). I was especially taken by the “knotted banding” pattern.
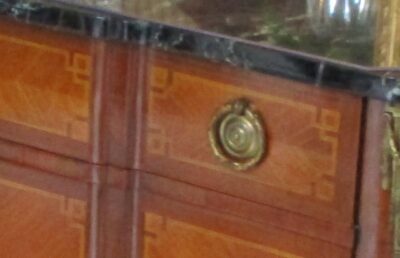
After another brief stop to swap out more laundry we wrapped up our journeys with a trip to Rochester NY where I made six presentations to the Rochester Woodworkers Guild — Principles of Furniture Conservation, Case Studies in Furniture Conservation, How Furniture Conservation Affects My Current Furniture Making, demonstrations of various conservation techniques, a review and demonstration of parquetry techniques, and finally a conservation/restoration clinic based on the pieces the attendees brought with them for that purpose.
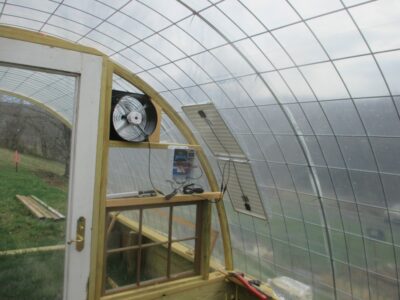
Now back home with summer trying to ramp up we are back at it big time. Mrs. Barn is feverishly working on her gardens and I am hard at work on the greenhouse, finishing the installation of a greenhouse fan, draping the structure with a shade cloth our newest son-in-law gave to us when it turned out to be too large for their patio space, and sealing up the perimeter to protect from the voles that are the bane of Mrs. Barn’s gardening life.

The shade cloth was something we had been wondering about as the inside temps were in the 80s when the outside temp was in the 20s. Now that the sun and outside temps are much higher the issue came front and center. I do not like high temperatures anyway, but when I was working inside the greenhouse in 110-degrees I broke out the shade cloth and affixed it in place. Combined with the fan that lowered the inside temps to a manageable 85 degrees.

Even though the 1/4″ hardware cloth covers the entire floor out to the walls, I made a second hardware cloth “flashing” to be ground-stapled on top of the continuous layer then crown-stapled to the walls. The tricky part is forming it to the posts, which usually required another piece or two to be cut and fitted. If voles get past this a number of Rat Zappers will be awaiting them.

As for vole-proofing the space, that began at the very beginning of the construction phase several months ago. I covered the entire inside space with 1/4″ hardware cloth, and now was the time to tie it all together with new pieces at the bottoms of the walls and posts. One more day of that and it will be time to move on the laying out the inside configuration.
I hope we get to stay home more from now on, but that may be a vain hope. In two months the family of GS#1 and GS#2 will be moving to live within five miles of GS#3. I’m guessing that Grandma and Grandpa will be burning up the roads between here and there.
I am anxious to get back into the shop to work at both the bench and in my writing chair, but that might have to wait a little longer.
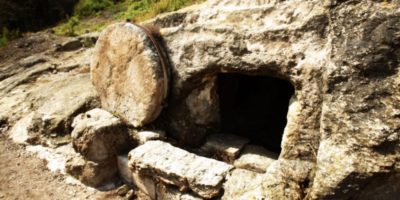
My most recent conversation with long-time friend “retired” broadcaster Brian Wilson is now posted on his Substack Brian Wilson Writes or his podcast Now For Something Completely Different.
It’s a pungent discussion of the social/political status quo. You have been warned.
Enjoy. Or not.
DCW
If I am known for anything in the realm of shop work it is that I am an enthusiastic advocate for two arcane tools; the polissoir at the finishing bench, and the toothing plane at the woodwork bench. I find myself grabbing one of my dozen toothing planes almost every time I am preparing a board for whatever comes next, as toothing planes are magnificent for the task of making a board flat/planar (but not smooth).
I have long asserted that we are living in a Golden Age of hand tool makers, and one of them is my friend Steve Voigt. Sometime last year I asked Steve to make me a custom toothing plane. As a result of our correspondence about the plane, I sent him three of my favorites to use as guides for his work.
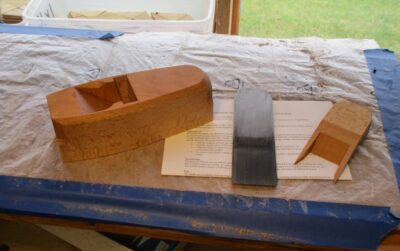
A few days ago I received two packages from him, one with my three and the other with his new one. I’m like a kid on Christmas morning, anxiously awaiting the time soon when I can really take it for a test drive.
Stay tuned.
Our Mondo March Marathon of Travel is now in the rearview mirror, we are back home in Shangri-la where Spring has definitely sprung. Were home exactly two days last month in between visits to grandsons old and new (and their parents, of course), an exhausting trek for these two geezers. The final push of 700 miles in one day was just about enough to put us in traction.
But now we are home and (mostly) recovered and the chores of spring are in full bloom. Flowers are popping up all over the place and Mrs. Barn is feverishly getting all the garden beds ready for her ministrations. This is her version of being “in the shop.”
I, on the other hand, have gone to the shop only long enough to package up my Donsbarn.com store orders. This will likely continue for another fortnight.
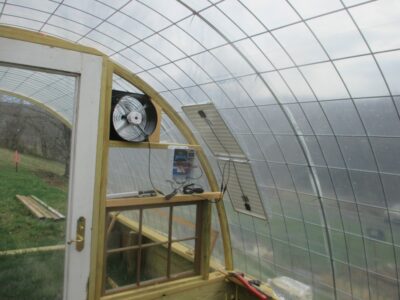
I have spent a couple days working in the greenhouse installing the new thermostat controlled solar powered ventilation fan. We’ll see if it is adequate to the task; the day before I started working on it the space was well over 100 degrees. Yesterday the fan brought it down to the mid-70s, but it was a cloudy day. I’m thinking I will have to augment the fan with a shade cloth. I’ll now spend a couple days finishing up the window framing before proceeding to moving in mulch and soil and building the main raised bed. I am looking forward to now getting fresh vegetables year-round.
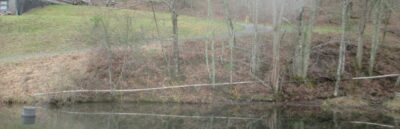
Being Spring time it has been my time to re-activate the hydroelectric system. Every year I check the line to repair any winter damage which results from trees falling on the 2” PVC penstock. Normally this occurs at the beginning of March but since Grandson #3 was born on February 28 and Grandsons #1 and #2 have birthdays in mid-March… This year there is much less damage than normal but I am taking the opportunity to reroute a few stretches of pipe in order to flatten out the inclined line of the pipe. Near the bottom and alongside the pond I disconnected, pulled out, then rerouted a 150-foot section, moving it up about three feet but weaving it in behind several trees. Ever try to “sew” with a 200-pound piece of thread? I am very pleased with the result but that one little step took more than two days and my shoulders still ache.
Next week I will do the same thing for three sections before reconnecting it at the top and harvesting the watts. If I can get the incline straight enough, with no swoops and swails all the way to the top, I can (theoretically) keep the system running almost all year long. Maybe all year long in reality. The final project in the coming weeks will be to construct a Coanda cover for the penstock intake.
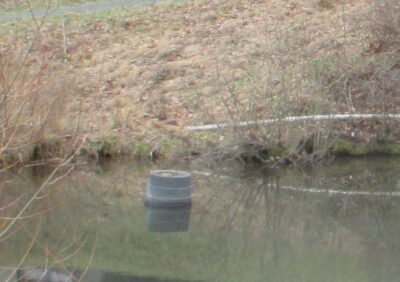
One problem to be solved this year involved re-setting the debris catcher on the top of the pond drain stack. Heavy ice in the pond this winter pushed it aside (sorry, no picture of that) leaving it sorta in place but pretty womperjawed, hanging off to one side. To set the strainer on its axis I had to strip down to my skivvies and shoes and venture neck-deep into the 50-degree water. Brisk. But, I got ‘er done.
That all said I can hardly wait to complete these necessary tasks and get back into the shop with the multitude of projects awaiting me there. Tool cabinet parquetry and fittings, full and 3/4 scale Gragg chairs, writing, editing, writing editing, and more of the same.
Stay tuned.
Although I have yet to see and touch it in person, my long time friend Jersey Jon sent me this picture of his new copy of the new Roubo on Furniture.
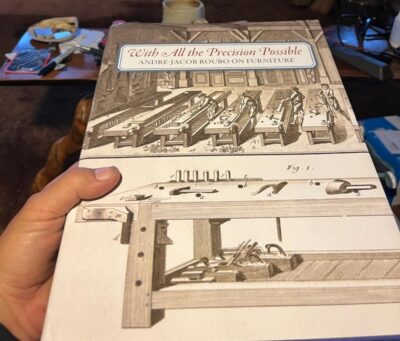
It’s not R2D2, it is R2V2.
As always. it is available over at Lost Art Press.
Recent Comments