While many artisans are content to work alone, as I am almost all of the time (an mp3 player loaded with podcast lectures and such is about all the social interaction I need during my work day), there are those magical interludes of fellowship around the workbench with a like-minded soul. Such is the case with my pal Tom, whom I first met by chance at a flea market ten years ago (he was selling, I was thinking about buying). That led to hundreds of Wednesday nights in his first-rate shop where a multitude of tools were sharpened or made, mountains of shavings were made then swept out into the yard, and on occasion, the world’s problems were solved.
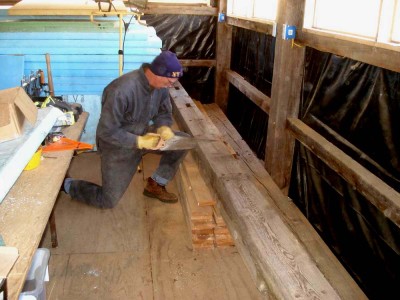
Tom even accompanied me frequently on working weekends to the barn, where what we were working on WAS the barn.
Tom visited recently, and is often the case, he tossed out an offhand comment that was a thunderbolt.
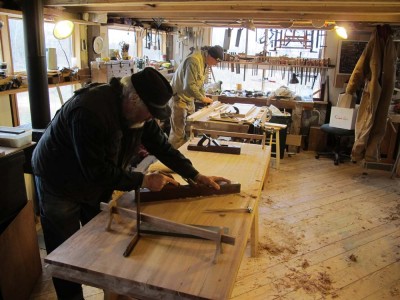
While he was making some tapered octagonal legs for a dressing table I had been wrestling with my HO Studley workbench top replica for the upcoming exhibit of the workbench and the accompanying tool cabinet. The grain of the bench surface, African “mahogany,” was just being, in the words of my ever foul-mouthed 98 year old mom, “A real stinker.”
Rob in Lawrence KS had offered his helpful observations, namely that I could use a high angled smoother tuned to a fever pitch. When I mentioned this to Tom with the regretful statement that I did not own such a tool, and that I was going to set things up to make one for myself, he casually remarked that there was a simple way of making a high angled smoother that might serve my purpose. When I tried it, I had to smack my forehead. Hard. The solution was both brilliantly insightful and mindlessly simple and best of all, easy. Coordinated problem solving like this is what woodworking fellowship is all about.
The solution? why, flipping the blade, of course!
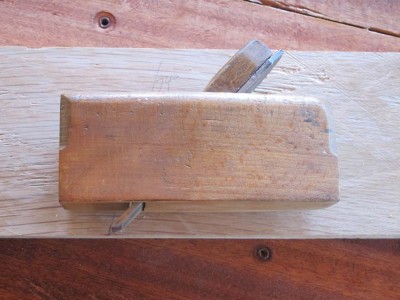
I first tried it on a tiny coffin smoother that I had, which was set up to cut at 49 degrees, but when the blade was flipped the new cutting angle was a bit too steep at 74 degrees. Yeah, a bit too steep.
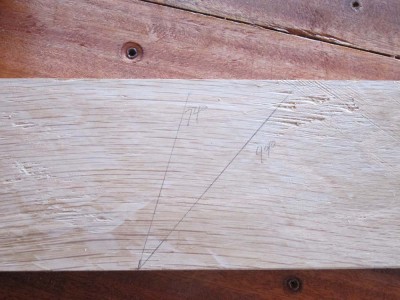
I then looked through my collection of bench planes to see which of them might be a good candidate for this modification. I had a nice little coffin plane with a very shallow angle on the blade bevel. It is set up to cut at about 45 degrees, and simply by flipping the blade over I got a 62-degree cutting angle. Not the perfect setup, but way better than I had before.
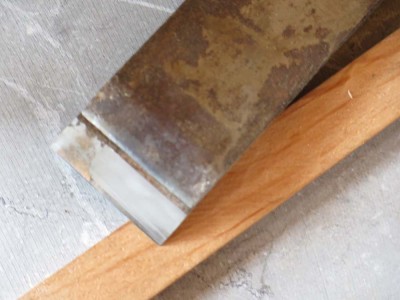

The new orientation turns the plane from a double iron bevel-down tool into essentially a single iron bevel-up plane. Yes indeed, I transformed one of my bench planes into a pretty nice high angle smoother in less than 30 seconds. For zero dollars.
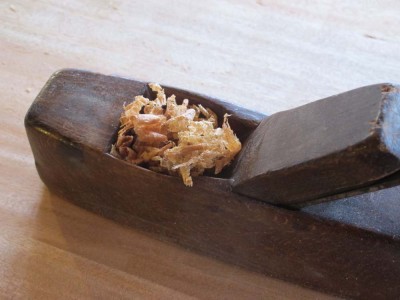
A couple minutes to touch up the blade on my 12000 water stone and the tool began its work. It wasn’t pulling off long, gossamer wisps, but did I mention I was planing African “mahogany,” a/k/a braided broom straw?
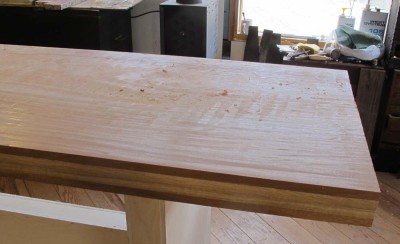
The result in the lower right corner of the image speaks for itself. Following the smoothing with a bit of scraping yielded an outcome that was acceptable, especially since after the exhibit I will be surfacing the bench top with a toothing plane. I remain committed to avoiding African “mahogany” in perpetuity, but for this one problem the result is in the right direction.
Yes, I am “all Studley exhibit, all the time” for the next month, but that tedium (?) was punctuated by a banner week at the Post Office box.
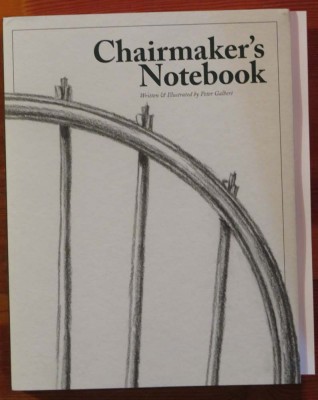
First came the brilliant Chairmaker’s Notebook from Peter Galbert. It arrived just in time for one of my periodic days at the ophthalmologist’s office (the periodicity depends on which of my eye diseases is acting up, and how severely) during which I had time to read a good part of it carefully and browse all of it to the end. The book is only partly about making Windsor chairs. In truth it is really about the way to think about, and the way to do almost anything of real consequence.
I am not a Windsor chairmaker and unlikely to become one other than as an amusement, my chairmaking runs from Point A, Gragg chairs, to Point A’, making slightly different Gragg chairs. Still, Peter’s eloquence and deep understanding, and the exasperatingly skillful manner of conveying them, made me smack my forehead repeatedly with the silent exclamation,”But of course!” while simultaneously silently muttering, “Man, I wish I had written this.”

I also received the printer’s proofs from Virtuoso, and to tell you the truth, the combination of the sumptuous imagery contained therein combined with the realization that almost five years of work are nearing the end made a sizable lump in my throat. It has been a project of passions — sometimes love, sometimes hate — as are most such undertakings, but it it noteworthy to celebrate its conclusion.
Finally, my good friend of three decades Dr. Walter Williams just send me a signed copy of his latest book. A collection of scores of columns, it will make for enticing bite sized bits of common sense wisdom.
All in all, a good week at the post office.
After long and careful consideration, I have concluded that I simply cannot host any workshops at The Barn this coming summer. The combination of the Studley book and exhibit, brutal winter aftermath with a mountain of things to do on the homestead, projects that have languished in the studio, and the need to wrap-up Roubo on Furniture Making (almost twice as large as Roubo on Marquetry) leaves me with no time nor energy to dedicate to workshops at the barn. I had planned on a historic finishing workshop in late June, but that will have to wait until net year. In September I will host a week-long workbench build for my friends of the Professional Refinishers Group web forum.
This is not to say I will be entering my long anticipated hermit phase. My presence and teaching elsewhere over the summer will be evident. Check these out.
Henry O. Studley Tool Cabinet and Workbench exhibit – May 15-17, Cedar Rapids IA
Making New Finishes Look Old – Society of American Period Furniture Makers Mid-Year Conference, June 11-15, Knoxville TN
Gold Leaf and its Analogs – Professional Refinisher’s Group Groopfest, June 24-26, Pontoon Beach IL
The Henry Studley Book and Exhibit (breakfast banquet address) and Roubo Parquetry (demo workshop) – Woodworking in America 2015, September 25-27, Kansas City MO
Just for fun, I want to walk you though the steps you will be taking when you attend the Henry O Studley Tool Cabinet and Workbench Exhibit next month. Some of the details are yet to be resolved, but I have a general idea of what the experience will be like.
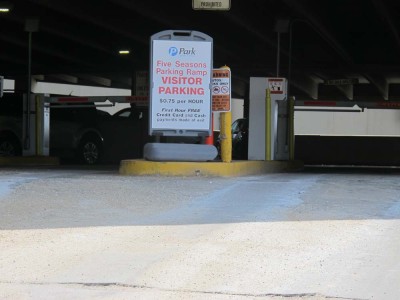
The first thing you are likely to do is to park in a lot either across the street from the Scottish Rite Temple, or a parking garage on the corner of the next block (but still visible from the SRT).
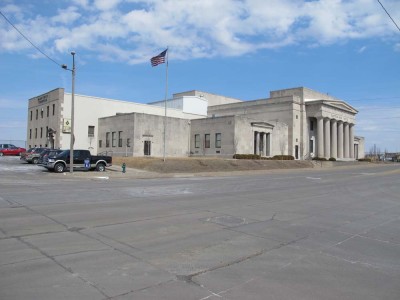
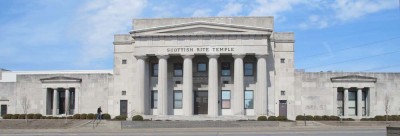
Then, walk through the front door at the center of the main facade.

Once in the lobby, turn to your left.
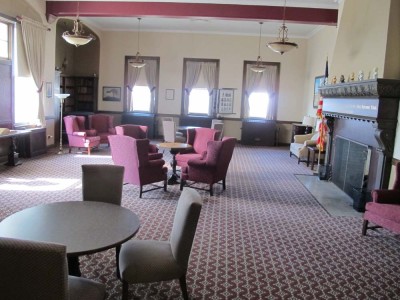
You will see the Library, and walk into it. We may have the tickets and books there, or they may be in the exhibit hall itself. Stay tuned on that.
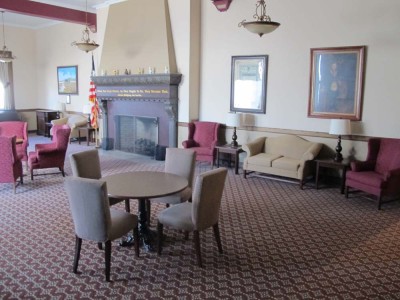
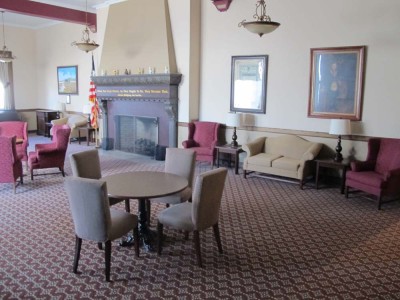
Once inside the Library, turn right and walk through the doorway.
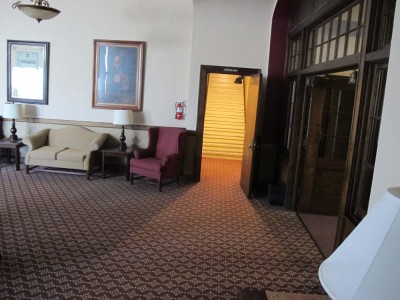
After about six feet, turn left into the entryway for the exhibit hall.
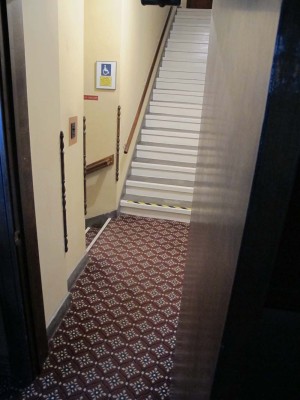

Come on in!
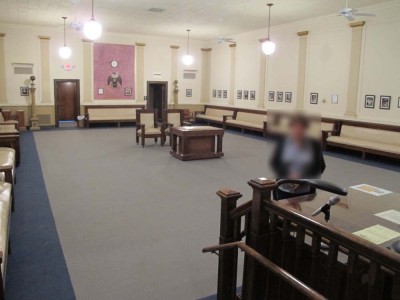
The exhibit hall will be drastically different once the exhibit is installed, as there will be dramatic theatrical lighting (no overhead lights at all), a black drapery backdrop, and large graphics and didactics on the walls.
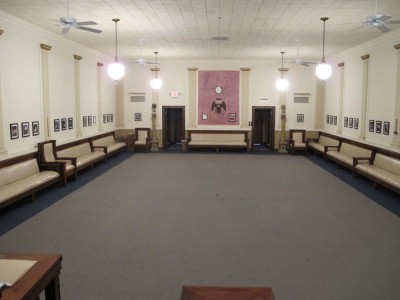
Along the center axis of the room will be the three main components of the exhibit. First will be the replica Studley workbench festooned with a half dozen vintage vises for your entertainment pleasure, along with castings from the original decorative Studely-made details in the cabinet. This will be the “You Can Touch This” part of the exhibit. Next will come Studley’s own personal workbench, and the culmination being the third station, that being the tool cabinet itself. These last two stations will be the “Don’t Even Think About It” installations.
In addition, there will be a silent video playing overhead on the projector screen of me emptying and packing the cabinet, video Narayan and Chris shot during our multiple safaris to Studleyville.
I hope you agree with me that the setting is darned near perfect for honoring the legacy of Henry O. Studley, and celebrating the release of the book chronicling his life and labors.
The upcoming Handworks event, essentially the Toolmaker’s Summit for hand tool woodworking, is unfortunately occurring at a time when I will be otherwise occupied. This saddens me, as it is a spectacular time of browsing, fellowship, and alas, covetousness in the realm of woodworking hand tools.
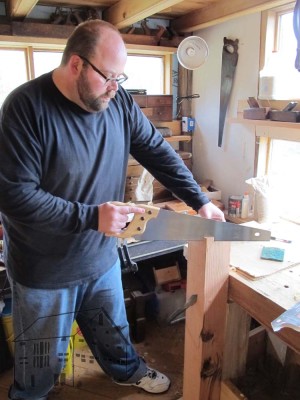
That is not to say that The Barn on White Run will have no presence at Handworks. Jason Weaver has “volunteered” to act in my stead at Festhalle and, thanks to the generosity of Jeff Hamilton, Jason will be haunting Jeff’s booth with wares and perhaps even exhibit tickets. 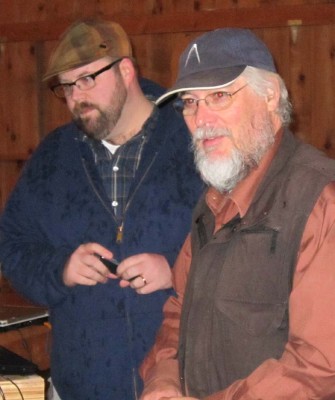
Jason should be easy enough to spot; as you can see by the picture of him standing behind me at Handworks 2013 he is nearly a head taller than most anyone else there. Admittedly, he may not be bundled up like last time when the howling arctic air filled the Festhalle.
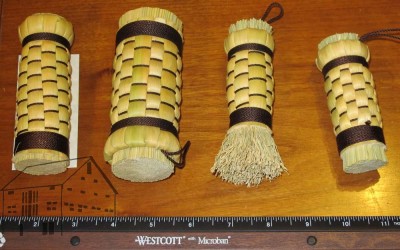
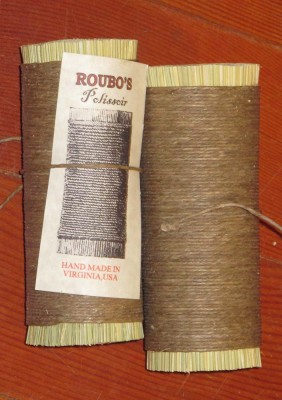
As for wares this time I think we will have only polissoirs and beeswax. To simplify the process I have priced all the 1″ polissoirs at $20 and both of the 2″ polissoirs at $40 (unfortunately despite the “non-existence” of inflation I have recently had to raise the price of the Model 296. On the other hand I lowered the price of the standard 2″ just for Handworks to make it easy on Jason, so maybe it all works out.)
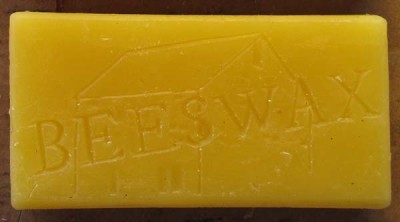
The quarter pound block of hand processed beeswax will be $10.
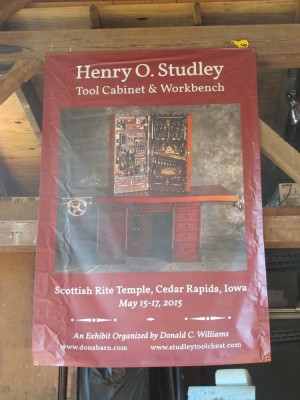
In addition Jason will be able to process ticket sales to the exhibit of the Henry Studley Tool cabinet and Workbench in nearby downtown Cedar Rapids (assuming it doesn’t sell out before then). If you are interested in tickets while at Festhalle, just look for the exhibit banner.
The final steps for conserving the tortoiseshell mirror frame were to make sure all the excess glue was cleaned off and the surface was given a final gleaning and polishing with the incomparable Mel’s Wax.
As I mentioned earlier, the tortoiseshell veneer was very fragile in general, and the simple gentle tasks of cleaning and polishing caused three new areas to pop up, so I had to deal with them immediately as well, exactly as described int the previous post.
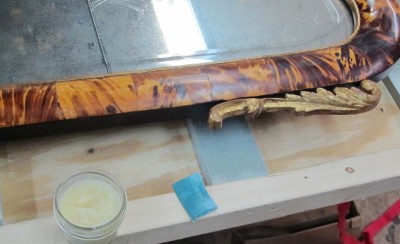
Mel’s Wax goes on effortlessly, and in the end yields a near-flawless archival protective surface. It goes on like sunscreen lotion, then goes dull as it dries, and buffs perfectly with almost anything. Paper towel, flannel, linen, cotton rags, anything.
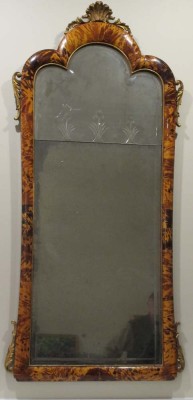
As always, the very last thing was to strap the mirror to its litter, take it back to the client’s house, and hang it up. I must say, it does look pretty good.
I will work on the second mirror once the storm of Studley calms down.
Now that Virtuoso: The Tool Cabinet and Workbench of Henry O. Studley is actually in production, one weighty anvil has been lifted from my neck. However, another anvil still sits there for another six weeks, that being the exhibit of the Studley collection. From now until then I am all-Studley-exhibit-all-the-time as I continue work on the exhibit components and attend to the multitude of details that have to all fall in place perfectly.

The replica workbench top continues apace. I got the top smooth enough (more about that in a day or two) to seal it with my preferred benchtop finish of 1/2 tung oil with 1/2 mineral spirits, and about 2% japan drier.

I like this finish as it soaks into the wood deeply and provides a nice robust seal to the wood.

For the exhibit the top will be pretty smooth, but once it gets back home I will achieve my preferred top surface by cross-hatching it with a toothing plane, a technique I learned from my long-time friend and colleague, and Roubo project collaborator, Philippe Lafargue. But for now it is nice and smooth.


I fabricated the exhibit base for the top from three 1/2″ Baltic birch plywood boxes, fitted them to fastening battens, and temporarily assembled it in order to layout all six of the vises going on it for the exhibit.
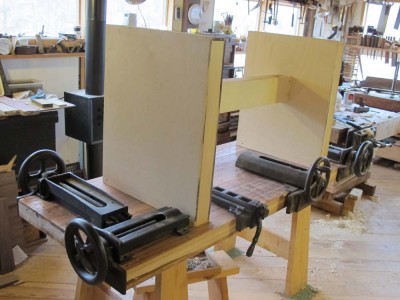
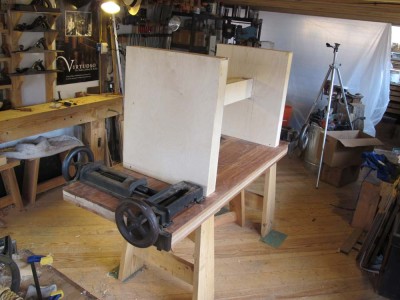
One of the beauties of this exhibit is that it may be the only time in their lives that patrons to a museum-quality exhibit will get the chance to touch and manipulate historic artifacts, namely the six vintage vises hanging from the new bench top.

===================================
If you would like to experience the bench top in person, and oh by the way see the entire Studley Collection, there are still tickets available here.
You can now order “Virtuoso: The Tool Cabinet and Workbench of Henry O. Studley” by Don Williams from the Lost Art Press store. The book is $49 and will ship in mid-May.
Orders received before May 13, 2015, will receive free domestic shipping. The first 1,000 orders will receive a nice commemorative postcard featuring a beautiful shot of the open tool cabinet shot by Narayan Nayar.
When you order, you will have the option to pick up your copy at Handworks in Amana, Iowa., on May 15-16, or have the book shipped to you. All shipping will occur after Handworks.
Retailers for ‘Virtuoso’
While we are certain that many of our retailers will stock “Virtuoso,” we do not know which ones yet will opt to carry it. When we have that information in the next couple weeks, I will definitely post it here.
Why No Digital Version?
There will not be a digital version of “Virtuoso” at this time. We have experienced a significant amount of pirate distribution of our titles, so we have decided that for this book, the pirates will have to manually scan and assemble the book if they want to rip us off. Our apologies to our law-abiding customers for this difficult decision.
Other Studley Products
We will have more news on other Studley-related products in the coming weeks, including posters, a feature-length DVD and toilet-seat covers (oh wait, no, those are for “The History of Wood”).
Thanks for all your patience during the last four years since we announced this project at Woodworking in America. A team of people has poured thousands of hours and tens of thousands of dollars into the research and production of this book. I think that effort will show in the book, and I hope you will be pleased.
— Christopher Schwarz
Recent Comments