… to wear this corduroy hat I got for my birthday this year. It is so hefty that it makes my brain boil when the weather is too mild. My daughter bought it at my (and her) favorite chocolate boutique. I will carefully wear it only occasionally in order to preserve it as long as possible.

Coolest logo ever, with the ribbons of dark chocolate curling up out of the joiner’s plane! I’ve toured their facility and they really do have cast slabs of chocolate awaiting further processing. And that chocolate, while a bit pricey, is to die for.
A couple weeks ago I spent several days working on the old house, first replacing some degraded decking on the front side of the house. There’s is a lot of decking on this house, somewhere around 1900 s.f. which needs replacing periodically, especially that which is exposed to nature directly. Such was the case her, as the decking in front of the living room and the platforms for potted plants across the front porch had been in place almost 3-1/2 decades, and were looking all the more shabby alongside the newly installed cedar shingle siding.
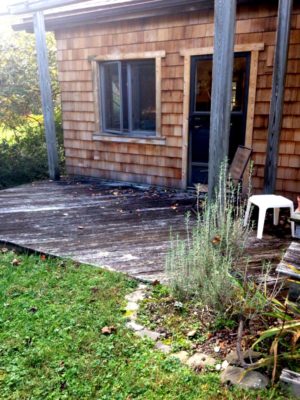
Dottir has a friend from church who is temporarily out of work due to Covid insanity so I was able to hire him for the week of work.
My plan was to replace the old SYP decking boards with synthetics so I would not have to address this problem any more in the lifetime. The only downside to using this material was the cost, which was $4/l.f. So, these two small sections of decking cost more than my first purchased domicile, a very nice 12×60 mobile home in 1975.
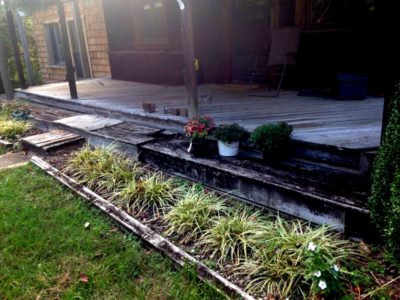
I also planned to re-use the sub-structure if it was in good enough shape, which was true for everything except one of the front platforms. Taking the old decking off required patience and care as the original screws had become subsumed by the wood expanding and contracting innumerable times over the decades. Two days of this and we were ready to roll with the fancy new plastic boards.
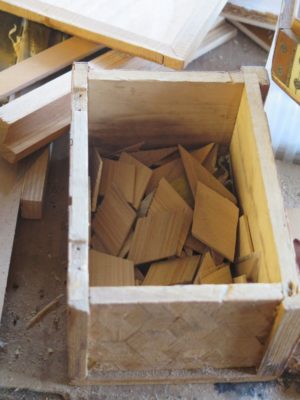
With the slim plywood “box” done for my new Kindle case it was time to move on to the tricked-out phase. That involved the assembly of a parquetry pattern from my inventory of 60-120-60 parallelogram lozenges.
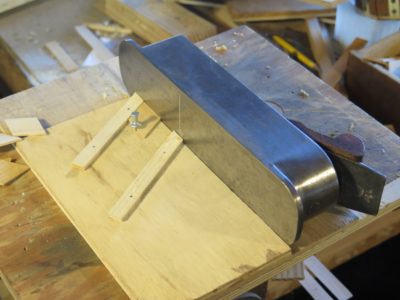

I knew right away that I did not have enough lozenges cut and trimmed to complete the job so I took some of the wood strips from my selection and sawed another bunch, enough to fill my little box to the top. I then shot the edges on my dedicated shooting board, fist shooting one pair of adjoined edges then rotating the lozenge onto the upper station, first planing one edge then flipping the lozenge and planing the adjacent one. I find this entire process of building up a stack of lozenges to be extremely calming, an especially respite in this current week. Plus, it let me put my sublime c.1810-50 Robert Towell miter plane to good use (fortunately for me Towell was careless about stamping his planes, otherwise I could not have afforded to buy this uber sewwt tool. Take note of the near-invisible opening in the sole!) I would have used the parquetry shooting plane I made last year but for the life of me I could not find where I put it. Sometimes having 7000 s.f. and several non-adjacent work spaces can be a curse, and this is one of those times.
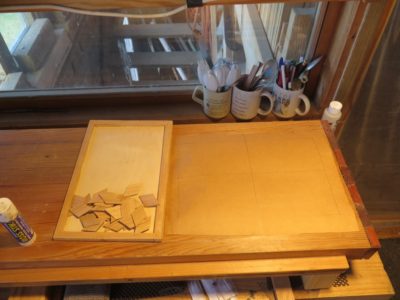

With enough of the finished lozenges in-hand I started setting them down on kraft paper after first drawing right angle bisecting lines to guide the work.
…a/k/a When Sears Tools Were a Real Thing
Like almost all Testosterone-Americans of my vintage I began my journey into the inexorable gravitational universe of Toolism at the local Sears store, buying Craftsman tools when they were the standard of excellence,
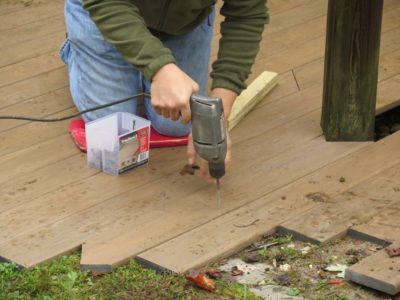
My very first purchase at Sears was my black Cub Scout folding knife (I did not last even a year in Cub Scouts due probably to my antipathy towards organizational authoritarian constructs, but I’ve still got the knife) when I was 11 years old. It was $2.95 if I remember correctly.
My first power tool, purchased with yard work/handyman money was this hand drill when I was 14, for$19.95 (I got the “Best” from the Good/Better/Best delineations you may remember) , a princely sum to a kid from a poor family making fifty cents or a buck for mowing the neighbors’ yards or helping to clean out a garage.
In the intervening years the only service/improvement the drill ever received was replacing the original keyed chuck with a keyless chuck about 30 years ago.
While working on some new decking at our daughter’s house we needed two drills so that we could both be productive, so I pulled this old beauty out of semi-retirement. Still works like a charm, but I probably need to replace the brushes and lubricate everything inside.
51 years, people, for an ordinary off-the-shelf hand drill. 51 years. Are you listening, Makita/DeWalt,/Craftsman/Bosch/Ryobi?
51 years.
I cannot deny that our spirits were vexed at the end of the second day when we had a nearly 100% failure rate bending the seat/back slats. We re-thought our process and examined the broken elements. It was then that I noticed ex poste all the failed bends were in kiln dried stock that I had planned for a different used and they accidentally went into the “bend” barrel. D’oh! We enacted a couple of minor ex ante revisions and combining these with the proper selection of wood we had perfect results and reveled in a couple days of almost 100-percent success (I think we had one failure and that might very well have been my impatience, bending the piece faster than it could stand).
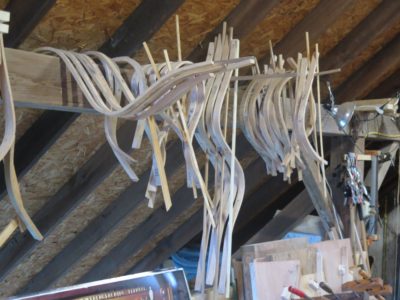
I’ve had good and bad streaks of steam bending, but these were the most stark examples of the challenges inherent in taking wood to the brink of what it can be forced into doing. We rejoiced as the inventory of chair parts grew into that which was needed for next August.
For now the chair parts are just hanging off the beam, seasoning until used by the workshop students. I have some more Gragg projects of my own to work on so there will undoubtedly be more experience interacting with wood, steam, and forms.
During our recent days of work preparing for next August’s “Build A Gragg Chair” workshop my friend John and I prepped a lot of wood sticks, and bent them to the forms required to become Gragg chair parts.

We got the steam box set up, the forms set out, and set to work.
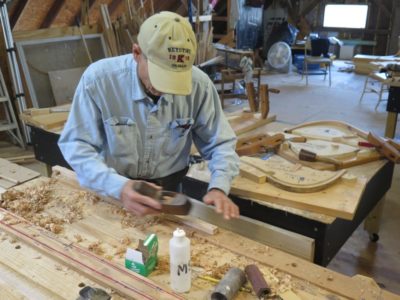
John hand planed dozens of chair pieces to get them ready for the thermodynamic adventure.
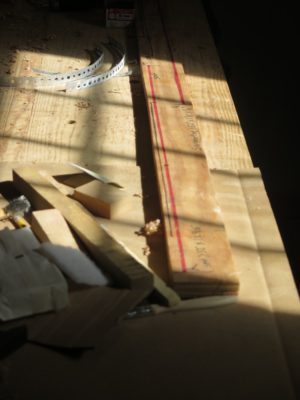
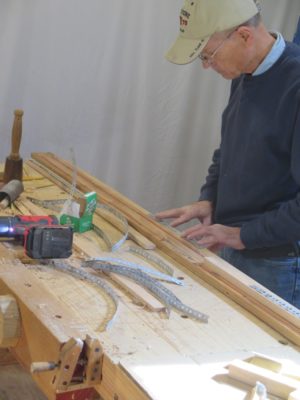
Once he had five or six pieces ready to go, he used the template board I created for this purpose and affixed the bending straps to all the pieces. When you have to execute two 90-degree bends only twelve inches apart in a dozen seconds, bending straps are pretty much mandated. We used flanged sheet metal screws and plumbing straps and attached them BEFORE they went into the steam box because the brief time to get the bending done after steaming does not allow for the straps to be put in place afterwards. And since the chairs get completely painted, any staining or screw holes can be dealt with.
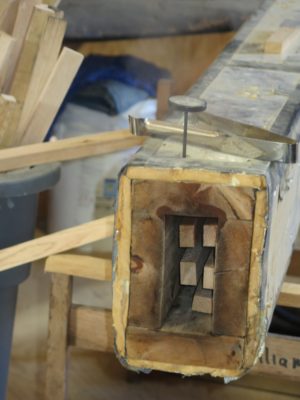
I placed them into the already heating box and waited for them to reach maximum temperature, which in my set-up is about 200 degrees.

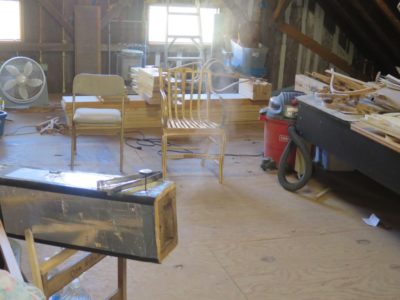
Using a state-of-the-art steam box seal we set the timer and waited the requisite time, 25 minutes for the arm and serpentine pieces, 45 minutes for the bent seat/backs.
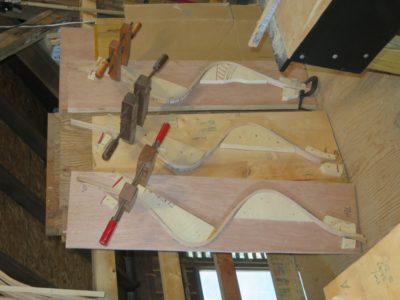
On the first day we had good success especially with the thin pieces, only one failure out of eight or ten attempts, but on the second day we had a string of failures approaching 50% when bending the continuous seat/back slats.
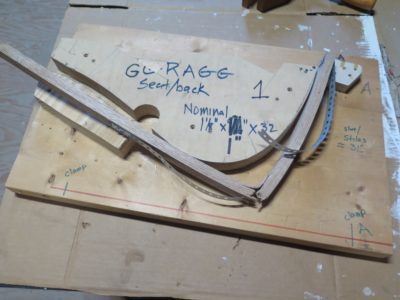
At that moment we could discern no reason for the degree of failure We needed to re-think our process.
Every now and then I get a nice note regarding my efforts to lead us into taking a giant step backwards, or at least move forward confidently with personal skills. I don’t really need the validation, but is is certainly pleasant to receive.
====================================================
Don,
Just wanted to give you an update (and some evidence) on how your historic finishing course alumni are doing. I built a new kitchen table to my wife’s spec; had to be smaller than the old “teak beast”–but big enough to seat 6–and it had to look “farm-house-ish.” See attached. Finish is four coats of Waterlox (Medium Gloss). Leaf-stowing design is from a Tommy McDonald Fine Woodworking article. Any confidence I felt on the finish work is from your course. BTW; Mel’s Wax performed very well on this piece.
Recent Comments