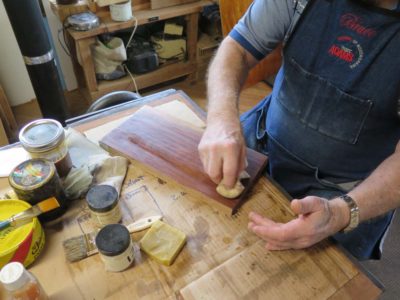
In keeping with my current “marketing” (non-) strategy for workshops, a while ago I was approached by a group of fellows commissioning a Historic Wood Finishing weekend workshop at The Barn. Once we set the schedule it turned out that there would be two slots open for anyone else who wanted to take the open places. If this interests you let me know. As always, the emphases will be on shellac and wax finishing for three days. The schedule for the workshop is October 9-11, 2021, and the tuition is $375.
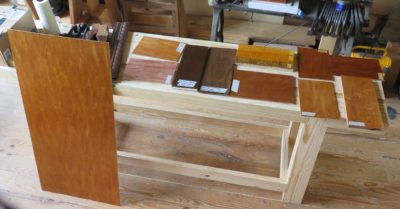
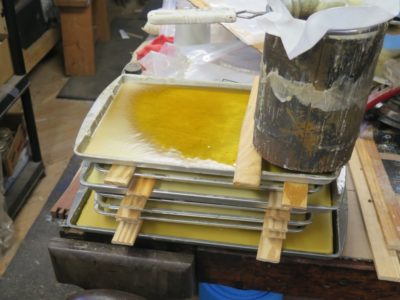
One of the activities that imparts an immensely pleasant atmosphere in the shop is refining a batch of the raw beeswax that I buy by the quarter ton. Since it does not require much work time on my part, I am relying primarily on the time-labor function of heat via crock pots and deep fryers, I occasionally start a batch in the morning (especially on days when I have full sun feeding the PV bank) and wind up by the end of the day with a stack of dedicated cookie trays filled with cooling molten gold. The last step is especially delightful as the insect carcasses have been long dispensed and the crystal clear purified beeswax cools, with its exquisite fragrance permeating the air.
And that, combined with making shavings at the other end of the space, just might be the definition of a wonderful day in the shop.
BTW these sheets of processed beeswax go into oversized zip lock bags awaiting Mrs. Barn to remelt and purify one last time as she casts the blocks in the kitchen during our cold winter days, thus mixing that fragrance with the faint sultry smokiness of the wood stove combined with whatever home made stew she is whipping up.


After not making any Mel’s Wax for nearly a year I finally ran out and needed to make another batch. It is an enjoyable process for me, requiring careful lab protocol weighing, heating, melting, mixing and decanting. The laser thermometer is a godsend.
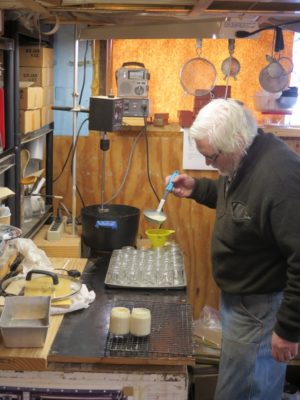
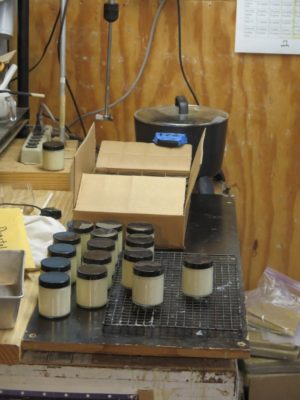
It’s been an interesting phenomenon watching the product go nowhere. I had thought that making and distributing Mel’s Wax would be a major component of my retirement activity but that has not materialized, and at this point I am not sure what to do (if anything) about it. Apparently I do not know how to market a cutting edge product to the people who need it. Last year en toto I sold 14 units, so even if sales double this year this latest batch should get me through 2021. Oddly enough I have had half as many orders for Mel’s Wax in the past fortnight than in all of 2020.
Perhaps this year will be the one where I can answer Mrs. Barn’s question, “So when are you going to act like you are retired?” I will soon be 66 and perhaps ease off the gas just a little bit.
2020: “Top that!”
2021: “Oh yeah? Hold my beer.”
On the other hand my mom was almost 104 and fully lucid when she died, so I expect a lot more good years of woodworking, writing, metalworking, fuming about the collapse of Western Civilization, chopping firewood…
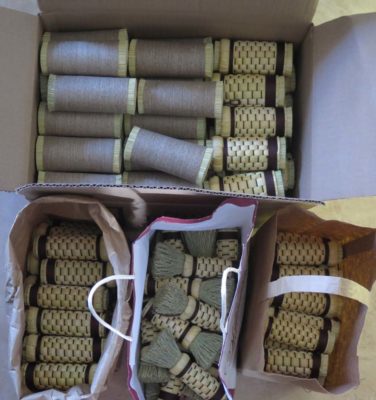
On my most recent visit to the Post Office to mail some family packages I was informed that they are no longer projecting packages to arrive before Christmas due to bottlenecks throughout the system. That’s good to know, so if you were planning on sending any of my wax or polissoirs for Christmas I can mail them immediately but do not expect to receive them before Dec 25th. Early December is the only time of the year where I regularly go to the post office more than once a week to mail packages.
Much to my surprise I made it to this date with a bit of my dwindling inventory remaining, I had my doubts. It’s been a few months since I received any new polissoirs since my broom maker has been dealing with some serious health issues and has not had the strength to sit and make brooms or polissoirs. At this point I am down to about a dozen of each model in stock (way fewer than in this picture). I’ve got plenty of wax blocks and can always process more, ditto Mel’s Wax.
I spoke to the broom maker last week and he is determined to get back into his shop this week. I hope it is true because that means his healing will be nearly complete. That will be great as we can start building excess inventory to prepare for Handworks 2021 on Labor Day weekend.

Recently I have been working with planemaker and friend Steve Voigt to help him create a wax polish for his exquisite new historic-style wooden planes. Well, Steve has been doing all the work, I am just supplying the materials and a few formulations based on the results I’ve had in recent years. His desire was for a beautiful appearance and a non-slick surface so that his planes could be handled with the tiniest bit of tack against the bare hand.
Based on some correspondence and a recent Instagram post, he has apparently arrived at the finish line. He is strongly recommending I make this product for others with similar interests and asked if I had ever made this formulation before, because it was in his words, “Da Bomb.” You can tell he has been a college professor, what with all that hipster lingo. (He is actually a pretty hip guy, especially compared to me being just a lovable curmudgeon shouting at the clouds)
My reply was, “Yes I had, and yes it was.”
It just might be time for a new product in the Don’s Barn Store. I’ve actually been playing with quite a few ideas…
Stay tuned.


Part of my process of refining the raw “slum gum” unfiltered beeswax from the honey factory delivered in a case of roughly 6-inch thick slabs from the bottom of a five gallon bucket, involves a step wherein the coarsely filtered molten beeswax/hot water slurry (removing the bee bodies and gross debris) is poured through fine pasta strainer into a cake pan and allowed to cool undisturbed.


After cooling and decanting the water with any remaining water soluble adulterant, I am left with a big block of beeswax with a fairly uniform layer of sediment on the bottom face of the block. This needs to be removed before moving on to the next step of filtering.
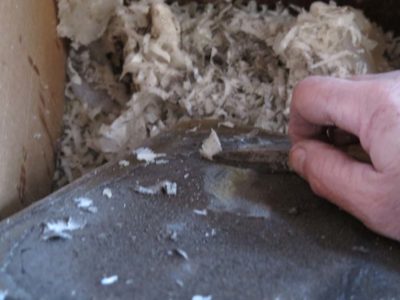
Normally I try to time the scraping off step for when the block of wax has cooled enough to be fairly solid, but still warm enough to be scraped easily with a large knife. There are times, however, when I do not get to this step soon enough and the block of wax with its accretions hardens fully. And with enough cold, it can get pretty hard. Scraping this is not impossible but it is some hard work when I am doing several of them at once.
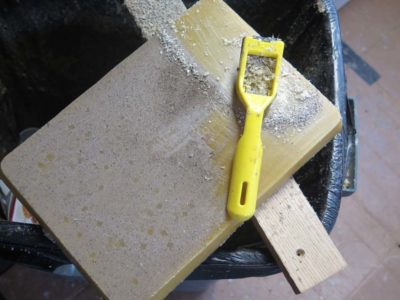
Recently I had a great idea while rummaging through my “Giant Files” drawer and pulled out this little curved Surform tool. I found that for a fully hardened block, even one that is chilled and rock hard, it removes the precipitant easily and quickly.
That smack is the sound of my pam striking my forehead. Usually in just a minute or less the block is ready to be put aside for the next melt during which time it will be getting its final filtering from me before moving into Mrs. Barn’s domain and one final filtering before casting into blocks.
I love it when caprice like this happens.
Handworks is now six months away and we are busily preparing for stocking the booth for the onslaught of the thousands of friends old and new bound by the love of traditional hand woodworking tools.
My broom maker has a standing order for dozens of polissoirs to make sure I have plenty of these magical tools for show and sale. Unfortunately(?) I still get orders almost daily so building up the inventory is going slower than I would like. I go to the post office every week with a bag of packages to send.
The broom maker and his wife have finally moved into their dream house he has been building for the past several years, and is having trouble finding the time to set up his own workshop just the way he wants it. I spoke to him this morning (I had actually run out of the Model 296 polissoirs) and just yesterday he was able to begin using the workshop in the new house. I will be providing a complete set of polissoirs as a door prize for Handworks.

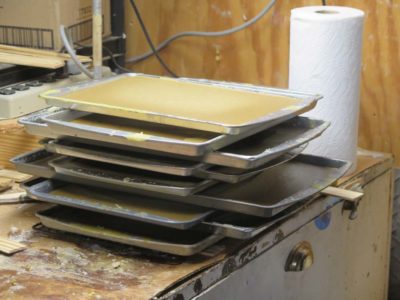
Here on the homestead I have been refining the raw beeswax, known in the apiary/honey/beeswax world as “slum gum”, to provide the purified raw material for Mrs. Barn to make into beeswax bars. There is nothing quite like the beautiful appearance of the amber nectar after the final filtering as I cast it out as molten material in cookie pans.

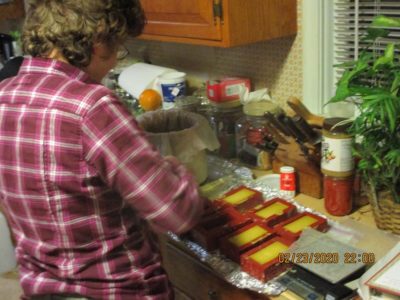
This is a favorite winter activity as it both heats the kitchen a little with her dedicated crockpot going almost 24/7 and imparts the lovely scent of clean molten beeswax throughout the cabin.



Over the days the pile of finished bars grows and grows, eventually becoming wrapped and placed in their storage boxes.
Meanwhile up in the Waxerie I’ve added casting more shellac wax and Blend 31 bars to my mix of activities. This is a nice punctuation to my other ongoing projects in the shop as it does not need my immediate attention all the time.
I plan to have a full inventory of polissoirs and waxes and stuff and will schedule hourly demonstrations at my booth at Handworks, and will expound on these as things come together.
This is not a “happy” bog post. It might be a little too much “inside baseball” but I thought you should know what is going on and what is coming down the pike. It’s probably bad form to discuss openly the costs of running a business, even a hobby one, and I will give that concern all the consideration I think it deserves. Okay, I’m done with that consideration.
It has been almost a decade since rediscovering the amazing surface prep and finishing tool called the polissoir, or polisher, and connecting up with a local craft broom maker to supply me with them. In that period I have sold and shipped thousands(!) of polissoirs and blocks of beeswax etc., and I hope to continue that success and match it with that of Mel’s Wax in the coming months and years. I delight in sharing the polissoir-and-beeswax’s almost magical qualities with the enthusiasts who have joined me in this trek taking a giant leap backwards in wood finishing. To encourage these tools’ adoption by the woodworking world I have kept the pricing stable almost since the beginning, folding the postage into the purchase price and keeping that unchanged since we went “official” with the Shop function on the website.
Unfortunately the postage increases implemented by the USPO over the past two years have affected me to the degree that, all by itself, postage now consumes over 15% of my gross sales revenue (and nearly 25% of the net), a nearly 100% increase in just the past year. This is so far out of whack I can hardly wrap my head around it, but the unavoidable result is that some of the heavier items in the Store will necessarily increase in price to reflect this grim reality as soon as we can edit the page.
(I am not griping about the post office, they provide excellent service to me and are convenient; I do not realistically have any other parcel carrier option out here in the hinterlands. I usually make the five-minute drive to our one-window post office in town once a week with a canvas tool bag full of parcels to mail. Making a three-hour round trip over the mountains to a parcel depot is not in the cards for me.)
To respond to this new cost reality, after long thought I’ve decided to raise the price of hand refined beeswax by $1 to $14, raising the Blend 31 to $17, and the shellac wax to $21.
All three models of the one-inch polissoirs will remain at their current price since they are so light weight and have apparently — thus far — remained below some postage threshold, but you never know with the USPS.
The large polissoirs, the two-inch woven-sheath and the Model 296 wrapped polissoirs, will be going from $47 to $49, and the two-pound bag of shellac flour will now be $75. Postage for Mel’s Wax is also 50% higher per unit than expected but I will leave that price alone for now as a strategic move.
I’m not apologizing for the increases: even though this is a labor of love for me I simply can’t keep selling and shipping products at the previous prices given the rising costs of postage. That is just a plain and simple fact whether I like it or not. I will be sad if these price increases diminish interest in polissoirs and waxes and such, but as the pundit says, “Facts don’t care about your feelings.”
And, given the recent disruptions in the bee hive health I am doubly glad I bought a lot of raw beeswax for us to hand-process into blocks and polishes just before the colony collapse crisis. I’m hoping that the raw material comes back down in price before I need to buy more at the end of this year, but at the moment the prices for beeswax are about double from when I bought some last.
Stay tuned and wish me luck.
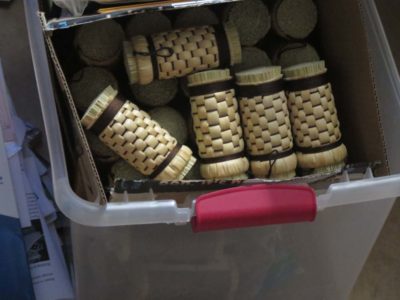
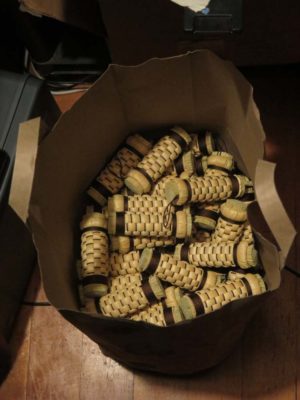
For the past several months just as I have been working feverishly on re-siding my daughter’s house my polissoirs maker has been concentrating on wrapping up his several years’ project building their dream house. They have been moving in recent days, but the broom-making studio is not yet fully installed in the new house, As a result the stream of new polissoirs dried up, and for the past couple of months at least I have been out of some inventory. I am happy to report that as of yesterday I am now fully stocked with all the varieties of polissoirs, with the routine of making new ones back on track. For the next several months we will be building the inventory for next year’s Handworks.
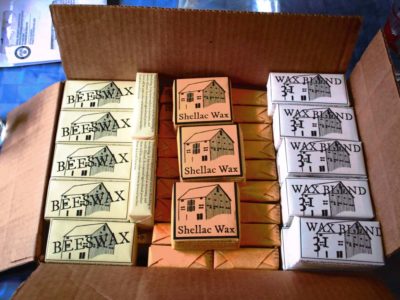
In addition I got the guy who makes the blocks of specialty waxes (that would be me) to get on the stick and re-stock them and Mel’s Wax as well.
I will be spending the next couple of days filling and shipping all the orders I have outstanding, and should be caught up by Thursday. I’ve got a couple trips over the mountains in the meantime or I would get them done tomorrow.
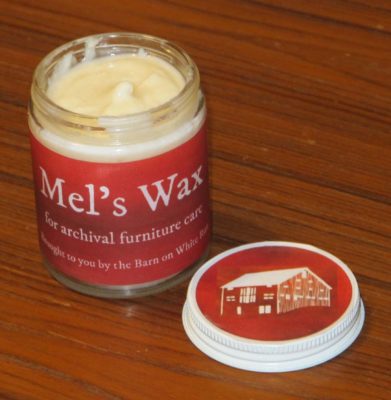
My friend LenR posted this in his Instagram page, featuring his use of Mel’s Wax. It is much appreciated, and prompts me to think seriously about how to market this remarkable product. At this point I am selling about one unit per month, when in reality I should be moving it by the case load. I’ll be turning my attention in this direction imminently. I’m definitely interested in ramping up production, but refuse to sub it out and am not really interested in wholesaling it. Those might be two intractable problems with my plan.
Any thoughts?
Recent Comments