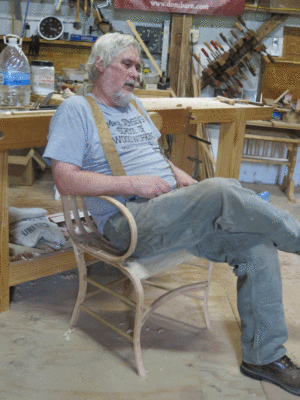
After completing the assembly of the chair structure I moved on to the sculpting of its elements with a variety of gouges, rasps, knives, spokeshaves, spoonshaves, and more, until it was elegant and comfortable (It is. Very.). In another eight hours or so I had it ready to begin painting with a shellac-based primer. This allowed me to see any lines that did not flow as I wanted, and to re-address them with my edge tools. Further, it identified any areas where fills were required.
I make my own fill putty similar to Gragg’s beginning with an oil-based primer and thickening approximately 1:1 with pulverized limestone from the garden center (he used lead white as the filler). Applying that into holes or joints as needed, I actually do not sand the fills, nor the shellac primer for that matter, until after I apply the subsequent heavy oil primer layer. This gives me plenty of body to cut into with sandpaper. My goal at that point is to yield a smooth-yet-faceted surface revealing the tool work that goes into making the chair.
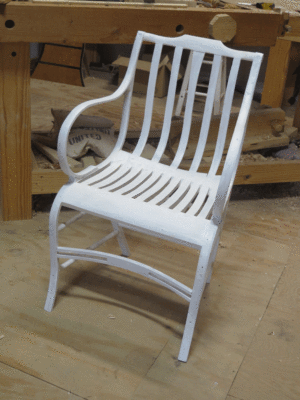
Soon I hope this chair will be ready for me to deliver to my friend and colleague Daniela to paint the peacock feather. Then for me it will be on to new adventures in the World of Gragg.
Stay tuned.
If you are interested in participating in the August 2021 six-day workshop to fabricate a Gragg chair, drop me a line via the “Contact” or “Comments” sections of the web site. At this moment there is one spot remaining. If it is successful I will undoubtedly schedule another for August 2022, 2023, 2024, to infinity and beyond.

Today I wrapped up (mostly) three of the “rubbed through” boxes and have put two to work to hold some of my smaller Gragg sculpting tools.
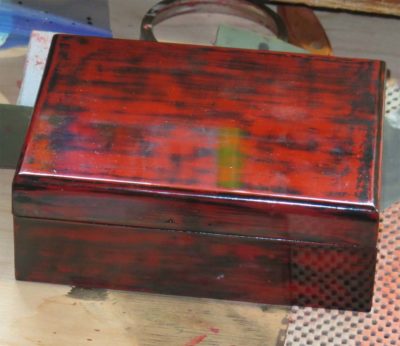
This one is black-over-red.
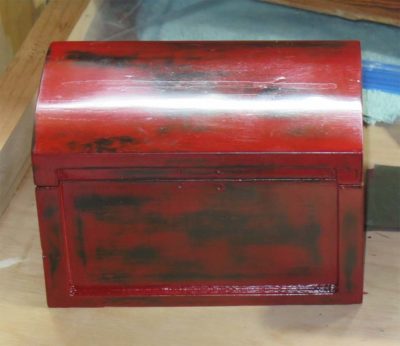
This one is red-over-black.
I did both of these with pigmented shellac with lemon shellac as the film forming component. I added Bone Black and Vermillion Red powders to taste, then three or four clear coats over the top after composing the pattern with wet sanding. Since these will get jostled at least if not outright “beat up” I have no plans to bring them to a mirror surface. I might rub them out with some Liberon steel wool and Mel’s Wax once the surfaces get really hard in a few weeks.
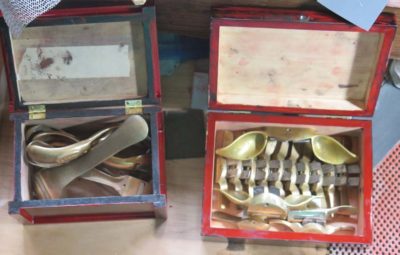
It is nice to have most of my smallest brass spokeshaves in the same box. I bought four sets of the ones offered by many tool merchants 35(?) years ago and am delighted to have them on hand. With duplicate sets I have total freedom to modify them as needed. These tiny tools are amazingly productive but it takes strong finger tips and a good “feel” for using them. Fortunately Mrs. Barn lets me massage her feet for a couple hours most evenings so my hands are up to the challenge.
After almost a year’s interruption Chris and I were able to synchronize our calendars and schedule the final three sessions for getting the raw video shot for the Gragg Chair video. It will probably come as no shock to some of you that the timing of my Gragg Chair Challenge was coincident with this development. I was able to use some of the work during the Challenge for the live filming also. When calculating the hours for the Challenge I had to take into consideration the pace of work on the video versus the pace of work when I am by myself.
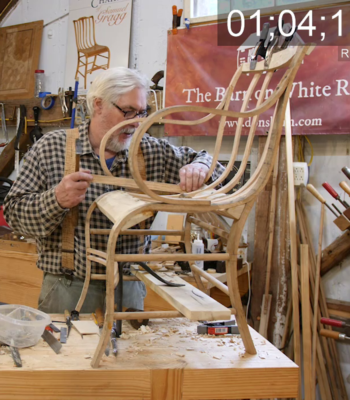
In this pre-penultimate session I spent all the time fitting the short seat slats, by far the largest segment for the entire project. It takes me about 90-minutes per slat, or 9-10 hours for the six, I do think that time will drop a bit as I get more familiar with exploiting the fishtail chisel even more aggressively. I’m also thinking about changing to birch for the seat rails; tulip poplar is a bit too weak for all that short grain in between the slat pockets and the necessary caution slows me down quite a bit.

Two more sessions and all that will be left is for me to review every minute of the almost 40 hours of video we will have in the compewder, and instruct Chris on the edits, chyrons, and segmentations.
The distribution plan is evolving but at this point my desire is to have the project divided into 15-20 episodes (the exact segmentation will depend on my review of the raw files), and they would be available to purchasers at a rate of two per week. Still noodling all that stuff.
Stay tuned.
I reached the 40-hour mark of the Gragg Chair Challenge with the construction phase of the chair more than 99% completed. The only construction yet to address is the fabrication of the glue blocks at either end of the arms. These will take another 90 minutes or so as they are tightly fitted into the irregular curved shapes to fit the spaces where the top of the arm fits against the serpentine back-seat-leg element at the top, and underneath where the arm swoops around and is attached to the serpentine element at the seat rail.
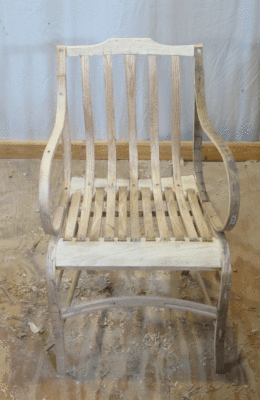
So, I am going to call this experiment a success. Indeed there were steps I could have been a little more fussy about (read: slower) but there is the unmistakable structure in place.
This is not to say that the chair is a finished work of art, no where close. There are still the 10-15 hours of sculpting and shaping all the elements into their final elegant form. And the 10-15 hours of laying down the paint foundation for the decorative scheme that is one of Gragg’s hallmarks. After that comes the days of decorating, I would estimate the peacock feather and pinstriping will take about four days. Taking all that into consideration it is fair to say that the finished chair is a little more than 1/3 done. Nevertheless I was heartened to get to this particular finish line with “victory” in sight.
With that, I will confirm and announce a “Construct a Gragg Chair” workshop for late August of 2021. By then the heat of summer should be in the rearview mirror (there are no 80-degree days in the forecast even now, with the warmest day upcoming being today’s 78 degrees), so this six-day class should be one of cool mornings and warm afternoons. I can accommodate four students and together we will work alongside each other, each of us constructing a chair.
Now I just have to figure out how to get four workbenches up into the attic workshop.
And put together the tool list.
And combine all the time lapse segments into one whole video to post on youtube.
And figure out how to even post videos on youtube.
And, and, and…
Things are progressing smoothly, at least in those moments when I am not distracted by and intriguing conversation via podcast. At the 32-hour mark I’m up to my eyeballs in dropping in the short seat slats. I should finish them in another few hours of work, and it is looking like the construction will wrap up around Hour 42.

I’m in the midst of a spate of Gragg postings, mostly because that’s what I’m doing a lot of and I don’t think posting a steady diet about working my way through a book manuscript is all that interesting.
In building a Gragg chair there are two steps that are immensely time consuming. The first is fitting the rear seat rail into the side units, which serves to unify and distribute all the weight stresses. This takes about 4-8 hours for me to do this one element, it depends on how much magic is in my hands and how well my good eye is working that day. The other is cutting 17 open dovetail pocket joints, two on each of the six short splats and the front rail fittings for the five continuous splats. No way to put lipstick on that pig, they are nothing short of tedious. It generally takes me up to two days to finish them.
Cutting the insides of a dovetailed open mortise is just a pain, or at least it’s a pain by the eighth or ninth one. I’ve used a variety of tools and approaches — a saw, bench chisels, a skew chisel, utility knife, and especially a fish-tail flat gouge. The last was especially helpful but store-bought versions were just not quite right. The splay of the tool tip was too modest to really get into the sharp inside corners. I made a custom one for this purpose a couple chairs ago but for the life of me cannot find it now. Instead I decided to make another.
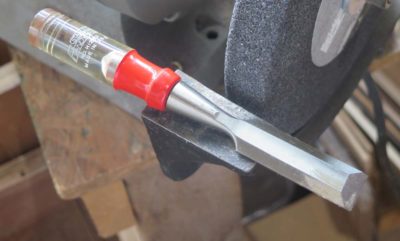
Looking through my box of derelict or disposable tools I found a 3/4″ Stanley “Handyman” chisel. It was a cheap almost cheezy tool of unknown provenance that still had the factory bevel and back. I recall modifying two of its siblings into 1) a dovetail chisel for small corner dovetails and 2) a small, short 3/16″ mortising chisel (this was before I fashioned my set of mini-mortise chisels out of plow plane irons). The thickness of the 3/4″ chisel steel is laughably thin for typical woodworking, but the thickness was precisely what I was looking for.
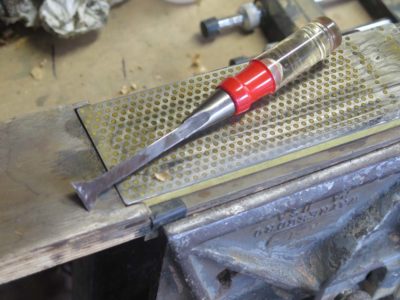
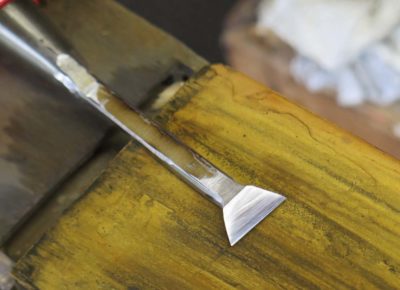
With my stationary grinder I created an extreme splay on the fishtail end of the chisel. Being careful and cutting in from the side I managed to avoid de-tempering the bevel. After running it through my usual sharpening routine I gave it a try.


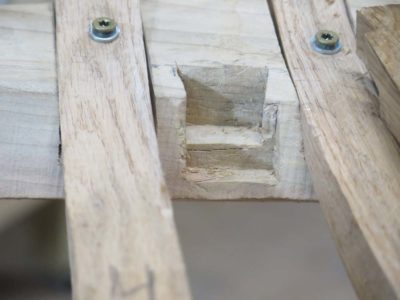
Absolutely splendid!
It is now an indispensable part of my Gragg tool kit, executing the task perfectly. Even better it reduces the time for cutting one of the dovetailed pockets from an hour to 45 minutes or less. Admittedly, since all of Gragg’s chairs are painted thus obscuring the exact nature of this joint I had to reverse-engineer something that I thought seemed right.
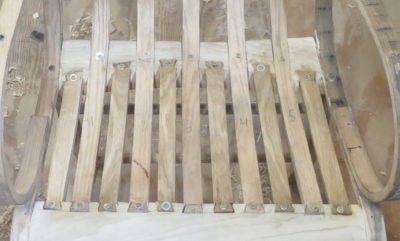
When you have to do 17 of them for each chair, ease and speed count for a lot.
Making this chisel was an extremely well-spent 90 minutes.

So there I was working away during my Gragg Chair Challenge, deep in the midst of the most tedious part of the entire project — fitting the seat slats into their dovetailed open mortises. At that same moment I was completely engrossed in listening to an Econtalk podcast wherein host Russ Roberts was interviewing statistician Nassim Nicholas Taleb on the latter’s observations about Covid-19 (Taleb’s observations cause me to stop and pay attention; I cannot tell sometimes whether he is a man of rare insight or a BS-spewing grifter. As Mark Twain said, “There are lies, damned lies, and statistics.” Taleb himself vacillates between statistics-as-analysis and mathematical-esoterica-as-intimidation).
It must have been a particularly compelling exchange between Roberts and Taleb because I sawed the slat cleanly on the wrong layout line. Try as I might, I cannot seem to stretch the piece longer to fit the space it is supposed to go.
It’ll go into the growing pile of kindling that is left after every Gragg chair.

This summer has seen a frenzied pace on the homestead, with summer lawn and garden activities, family comings and goings, working on the book manuscript and photography, and now, the final sessions for recording the Gragg Chair video. Chris my videographer has been even more occupied than I given that last year he started a new, full-time job, he and his bride bought a new (to them) house with all the attendant time sunk into that as required, and just recently a brand new baby. All that to say it has been almost a year since we were able to get an intersection between our two calendars, and that intersection occurs tomorrow.
Combining my preparations for that with my ongoing Gragg Chair Challenge I’ve been spending a lot of time up in the attic studio workshop, just as we have been experiencing our summer heat wave with many consecutive days up in the mid 80s. The locals are griping about the heat whenever they get together to chat about anything. One implication of the warm sunny weather is that the attic workshop is crowned by almost 3000 square feet of uninsulated roof, the material of which is heavy corrugated asphalt panels. So, if the sun is shining the overhead ceiling becomes a high temperature radiating panel. My thermometer indicates that the static room temperature is often well over 100 degrees.

To mitigate this effect and make the space useable I have a three-foot low speed exhaust fan. When it is running and sucking cooler air from lower volumes of the barn, the space is a congenial working environment. Then, last week the motor burned out for the fan. Since that motor was one of a group of motors I rescued from a dumpster 25 years ago I was not overly distraught that I only got a dozen years of service from it. I immediately grabbed another, identical motor off the shelf and installed it. Only when I threw the switch did I discover that I had failed to confirm the motor’s rotation before the installation, and the fan was blowing outside in rather than sucking inside air out, the way an exhaust fan is supposed to be set up.
The happy ending to the story is that the fan running “backwards” renders the space even more comfortable than running properly! The robust flow of cooler, outside air flowing over me while working makes my time there even more joyful than I was expecting. I just might leave it that way.
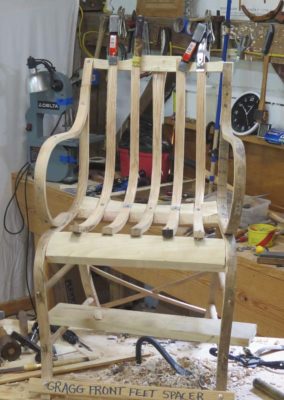
I’ve hit the 24-hour mark of the Gragg Chair Challenge with completing the fitting of the uni-piece bent seat/back elements into the rear seat rail. I’m expecting to finish fitting these into the front seat rail and crest rail somewhere around hour 28, and then chop the mortises for the front and rear rungs. The next big step after that is to disassemble the chair and glue everything together stretchers. After that the only major elements to add are the short seat slats. Then the real sculpting begins.

I’m getting a very good feeling of optimism about a Gragg Chair Workshop in late August 2021. If this interests you, let me know.
I remind you that the goal for the workshop would be the basic construction of the chair. Completing the chair would take at least another week of time. Still, my goal a couple years ago was to get the time expended to complete a chair from raw sticks to delivery at under 150 hours. I’m pretty sure I can get there easily. My next goal will be 120 hours.
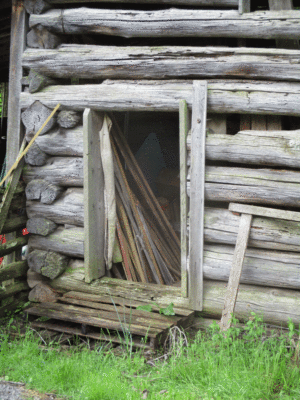
When we acquired Shangri-La in 2001 I was especially delighted that there were standing outbuildings suitable for a variety of purposes. The largest of these was a small-ish chestnut log barn that had previously housed livestock. For our use as a storage facility the original tiny doorway was a hurdle, it being only about 5-feet high. In short order I sawed the next higher log section to open the entrance to one that was not an undue burden to use, even though it was still not large enough to pass through without ducking.
After opening the doorway I had a piece of chestnut log about 3-1/2 feet long by a foot wide and perhaps eight inches thick. It had been notched with edge tools when originally built so that log scrap had a flat side from the git-go. Some time around then I saw The Woodwright’s Shop with guest chairmaker Don Weber who described what he called “a bodger’s shave horse.” John Alexander’s 1978 Make A Chair From A Tree, was already a long-time part of my personal library, and his infectious evangelism for primitive woodworking inspired me even though my own work was not centered in this direction. Those two paths intersected with the chestnut log chunk and it wasn’t very long before I took that and a bunch of other pieces from the scrap box and made a short length three-legged shaving horse. I used it for many years as a traveling demonstration tool.
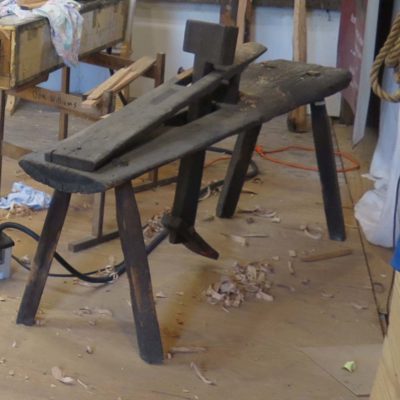
During the ongoing video project to document making a Gragg Chair I was vexed at being unable to locate and use this small shaving horse and instead had to use my gigantic one (6′ long), another almost-castoff I bought cheap at auction since the pivot rod housing was busted. I fixed it in an hour. It is a fine tool but not my favorite.

Recently I was rooting around the basement of the barn and came across the remains of the scrap chestnut horse. I do not have any memory of it making the trip from Maryland eight years ago, so I wonder of someone else tossed it into the big rental truck. I say “tossed” because all three legs were missing, and two of them had broken off inside the tapered mortises.

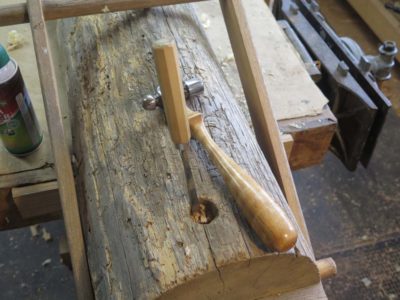
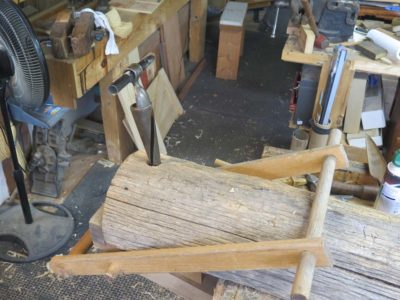
I cleaned out the detritus in the mortises then re-reamed the holes with this sweet tapered spiral reamer I got at a tool flea market for $12. It is beefy, precision-made, and still sharper than all get out. Two or three complete rotations is all it took to get the mortises perfect for new leg tenons.
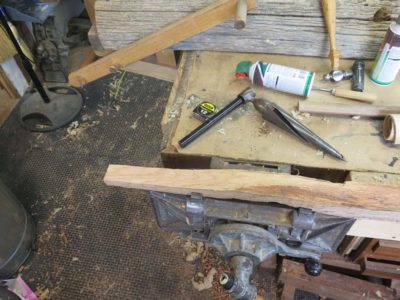
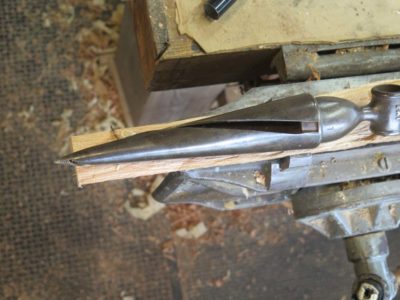
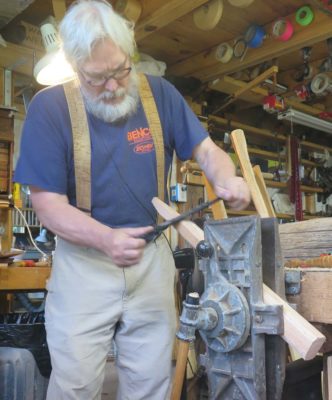
Using the reamer as the pattern I shaved three new legs from waste stock up in the Gragg workshop/video studio up in the fourth floor attic.
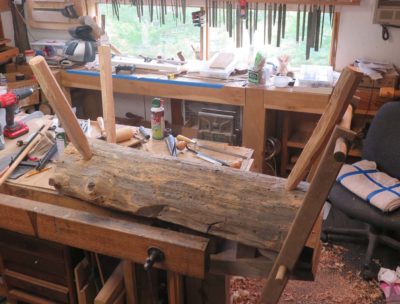
In about an hour of total time I had the new legs cut, tapered, installed and trimmed to length. I flipped it over and it was ready to be put to work.
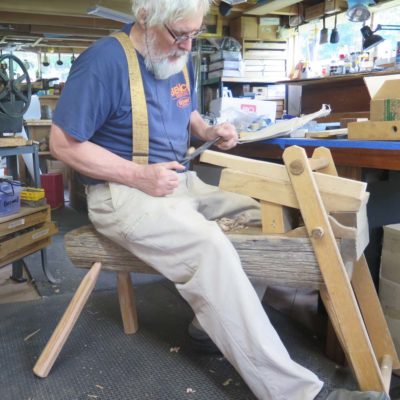
It is good sometimes to have scraps just laying around.
Recent Comments