You might be getting tired of HO Studley posts, but it is all I am working o these days so it’s pretty much all I have to talk about. It will all be over soon.
On my final visit to the Studley tool cabinet last October, with the owner’s permission I made a number of silicone rubber molds from the details Studley created and integrated into his masterpiece. My access to the elements was not perfect, it was an intact artifact hanging on the wall after all, so I chose two part silicone molding putty from Hobby Lobby. In the past I have used food grade molding putty by the bucketful, but for this project I needed just a bit and the hobby store package was just fine.
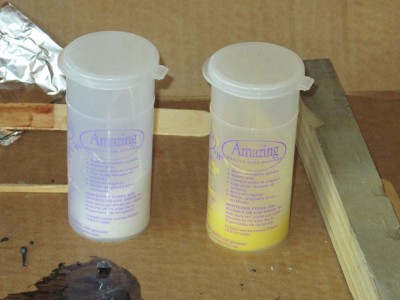
Using it is simple, just take equal parts of the two putties and knead them together until the color is uniform. Then, in the next 15-20 seconds press the wad against the surface you are trying to mold, sit back, and remove a finished and cured mold in a few minutes.
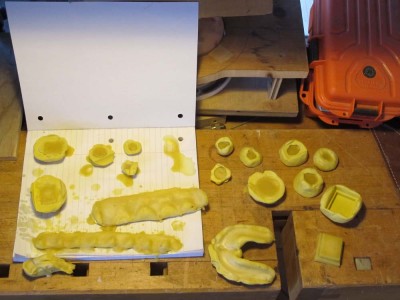
Given the spatial logistics of taking impressions from the tool cabinet, the molds were not perfect but they were useful. Once I got into the swing of producing the elements for the exhibit “The Henry O. Studley Tool Cabinet and Workbench” (tickets still available) I made some first generation beeswax castings from those molds just to see what was needed to come up with something exhibit worthy.
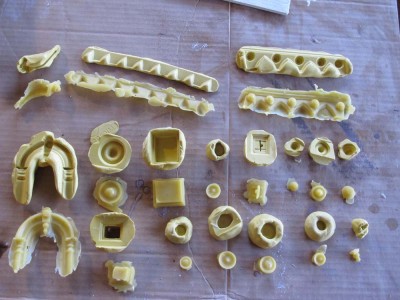
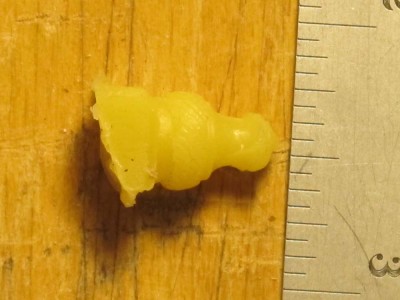
It’s fair to say that all of the castings in the upcoming exhibit were the result of several generations of molds and castings, with many hours spent in refining the representations of the elements under the microscope. On a project with more available time I might spend a week per element, but in this case I was lucky to carve out a day per element.
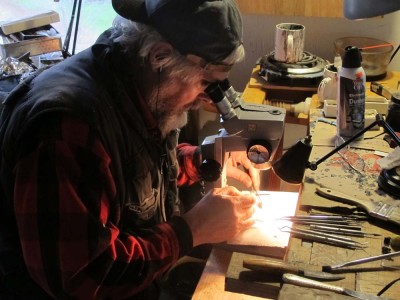
Much like picture from the Mars Rover, the whole is often a composite assembled from the disparate pieces. Even so, these are not perfect but they will allow the exhibit visitors to get a better sense of what Studley made to embellish his masterpiece.
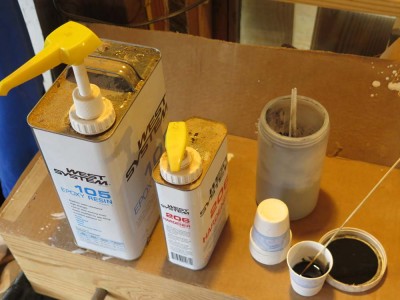
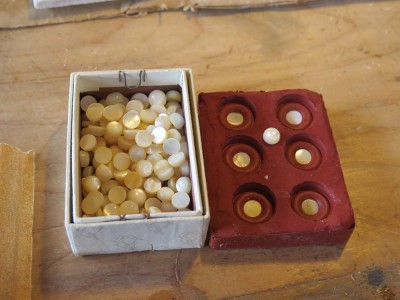
In the end, using the molds for casting some pigmented West System epoxy and some mother-of-pearl I got results that will convey the grandeur of these elements up-close-and-personal for the exhibit patrons as this panel will be sitting on the replica workbench for touching and examining closely.
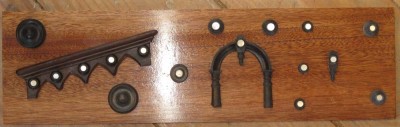
As time allows I will detail the process of refining specific elements, with observations about both moldmaking and casting materials useful to the decorative artisan.
Integral to the in-production book Virtuoso and the upcoming exhibit on the same topic, I am striving to make it more than just a tool peepshow. You are gonna learn something even if you do not want to!

Part of that learning experience will be the exposure to the remarkable Studley workbench and vises (above), including a display of similar contemporaneous vises that have been loaned for the exhibit.

To carry the weight of these six vises (somewhere in the neighborhood of 500 pounds) I built a fairly faithful replica workbench top, sitting on a base made for the exhibit but which will be swapped out for a cabinet base at some point.

About the only semi-tricky part of the bench build was dropping the end vise dog slot with my 3-1/2 hp plunge router, the only power tool that makes me nervous.
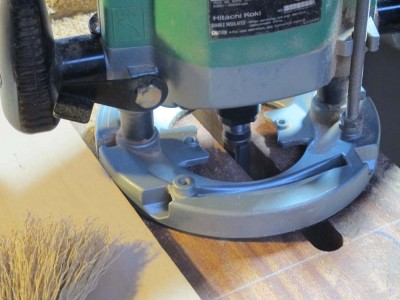
With multiple measurements and confirmations, I cut the channel from above and below, and the vise and its dog yoke dropped into place cleanly.

Now I can put the router beast away until I need it again in several more years.
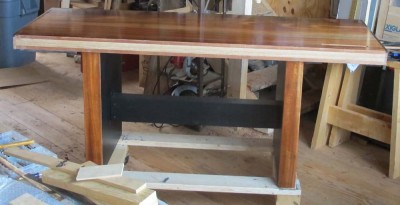
To increase the didactic function I left the front edge of the replica bench unfinished so you can see the core construction. As soon as the unit is back home the already-constructed front edge will be installed. Another thing to occur after the exhibit will be to dispense with the glossy finish applied for the display (four coats of Tru-Oil, then buffed) through the vigorous use of a toothing plane to leave the surface I prefer.

I don’t have any pictures of the finished bench with all the vises on it. I mounted them when it was upside down, but could not budge it to flip it right side up until I had removed all the vises. So, you will just have to wait on that visual for the exhibit itself.

photo courtesy of Narayan Nayar
It might be the fact that I am in the midst of what could be called Studley Silly Season, wherein my time and energies are focused entirely on getting the exhibit of the Henry O. Studley Tool Cabinet and Workbench done and over, but it seems that I see everything in the light of what old Henry had in his tool cabinet. One of his tools was this set of ultra precise measuring calipers (above).

Consider this intriguing micrometer I found in a vintage tool store in Connecticut a couple of years ago, and which I have found a useful addition to my tool kit. While it is functionally similar to the Starret vernier micrometer Studley had stashed back in his tool cabinet, this one is a more straightforward micrometer system mounted on a movable bar.
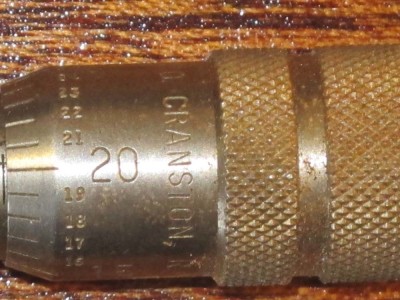
Made in Cranston RI at the Central Tool Co., this is unlike anything I had ever seen before, notwithstanding my years in a foundry/machine shop.
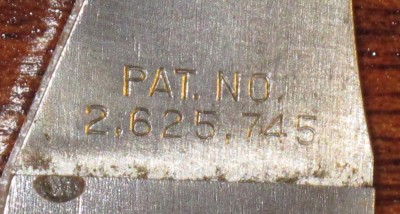
Just something for amusing contemplation on a beautiful spring evening.
My Team Studley compatriot and project photographer Narayan Nayar tells the tale of preparing hundreds of images for the book, which incidentally is about halfway through production. It is scheduled to be released the day before I start the installation of the Studley Tool Cabinet and Workbench Exhibit on May 13.
Am working on getting the exhibit finished all day, every day.
DCW
Yes, I am “all Studley exhibit, all the time” for the next month, but that tedium (?) was punctuated by a banner week at the Post Office box.
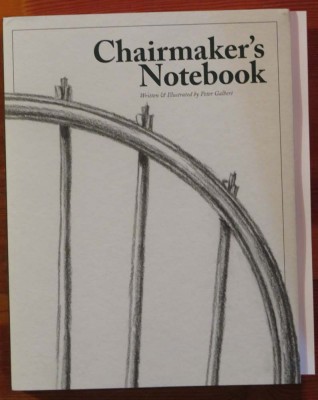
First came the brilliant Chairmaker’s Notebook from Peter Galbert. It arrived just in time for one of my periodic days at the ophthalmologist’s office (the periodicity depends on which of my eye diseases is acting up, and how severely) during which I had time to read a good part of it carefully and browse all of it to the end. The book is only partly about making Windsor chairs. In truth it is really about the way to think about, and the way to do almost anything of real consequence.
I am not a Windsor chairmaker and unlikely to become one other than as an amusement, my chairmaking runs from Point A, Gragg chairs, to Point A’, making slightly different Gragg chairs. Still, Peter’s eloquence and deep understanding, and the exasperatingly skillful manner of conveying them, made me smack my forehead repeatedly with the silent exclamation,”But of course!” while simultaneously silently muttering, “Man, I wish I had written this.”

I also received the printer’s proofs from Virtuoso, and to tell you the truth, the combination of the sumptuous imagery contained therein combined with the realization that almost five years of work are nearing the end made a sizable lump in my throat. It has been a project of passions — sometimes love, sometimes hate — as are most such undertakings, but it it noteworthy to celebrate its conclusion.
Finally, my good friend of three decades Dr. Walter Williams just send me a signed copy of his latest book. A collection of scores of columns, it will make for enticing bite sized bits of common sense wisdom.
All in all, a good week at the post office.
Just for fun, I want to walk you though the steps you will be taking when you attend the Henry O Studley Tool Cabinet and Workbench Exhibit next month. Some of the details are yet to be resolved, but I have a general idea of what the experience will be like.
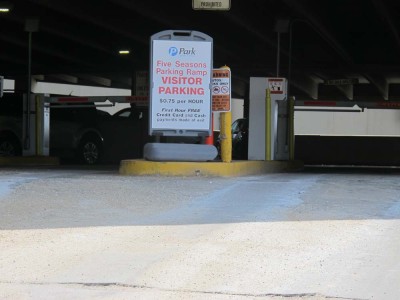
The first thing you are likely to do is to park in a lot either across the street from the Scottish Rite Temple, or a parking garage on the corner of the next block (but still visible from the SRT).
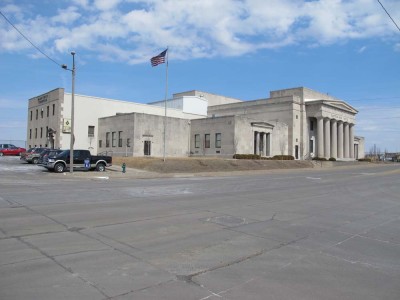
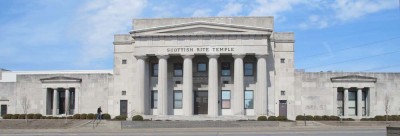
Then, walk through the front door at the center of the main facade.

Once in the lobby, turn to your left.
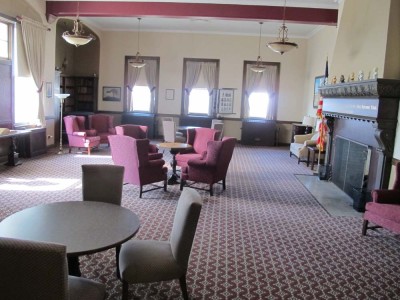
You will see the Library, and walk into it. We may have the tickets and books there, or they may be in the exhibit hall itself. Stay tuned on that.
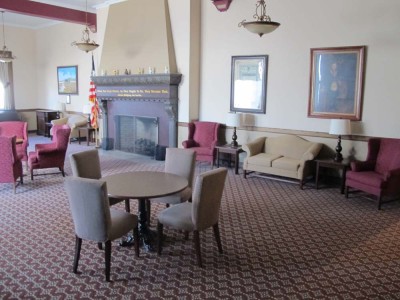
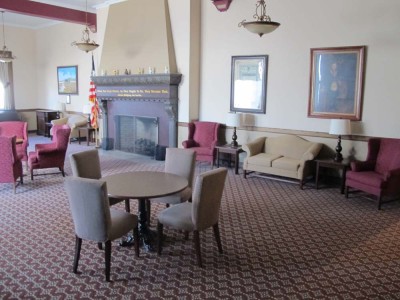
Once inside the Library, turn right and walk through the doorway.
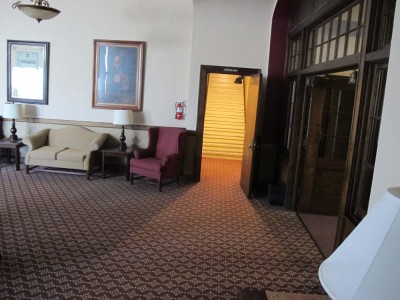
After about six feet, turn left into the entryway for the exhibit hall.
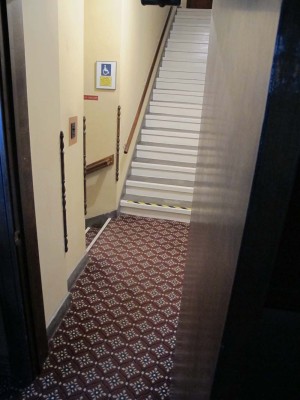

Come on in!
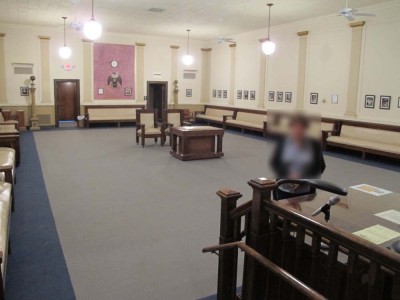
The exhibit hall will be drastically different once the exhibit is installed, as there will be dramatic theatrical lighting (no overhead lights at all), a black drapery backdrop, and large graphics and didactics on the walls.
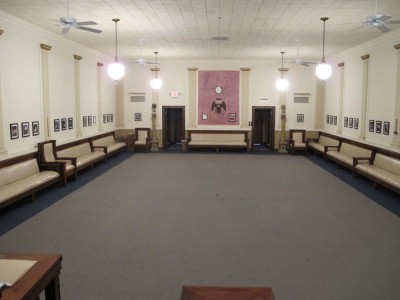
Along the center axis of the room will be the three main components of the exhibit. First will be the replica Studley workbench festooned with a half dozen vintage vises for your entertainment pleasure, along with castings from the original decorative Studely-made details in the cabinet. This will be the “You Can Touch This” part of the exhibit. Next will come Studley’s own personal workbench, and the culmination being the third station, that being the tool cabinet itself. These last two stations will be the “Don’t Even Think About It” installations.
In addition, there will be a silent video playing overhead on the projector screen of me emptying and packing the cabinet, video Narayan and Chris shot during our multiple safaris to Studleyville.
I hope you agree with me that the setting is darned near perfect for honoring the legacy of Henry O. Studley, and celebrating the release of the book chronicling his life and labors.
The upcoming Handworks event, essentially the Toolmaker’s Summit for hand tool woodworking, is unfortunately occurring at a time when I will be otherwise occupied. This saddens me, as it is a spectacular time of browsing, fellowship, and alas, covetousness in the realm of woodworking hand tools.
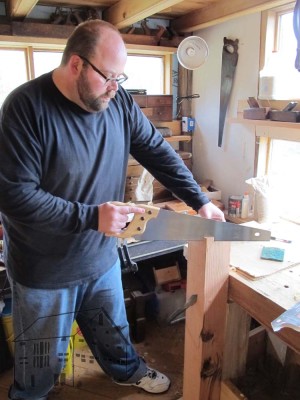
That is not to say that The Barn on White Run will have no presence at Handworks. Jason Weaver has “volunteered” to act in my stead at Festhalle and, thanks to the generosity of Jeff Hamilton, Jason will be haunting Jeff’s booth with wares and perhaps even exhibit tickets. 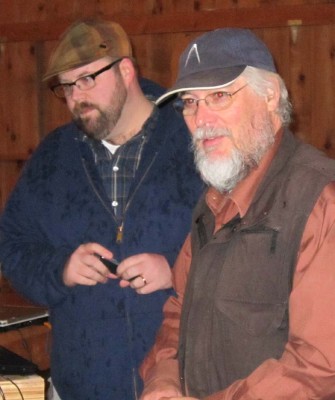
Jason should be easy enough to spot; as you can see by the picture of him standing behind me at Handworks 2013 he is nearly a head taller than most anyone else there. Admittedly, he may not be bundled up like last time when the howling arctic air filled the Festhalle.
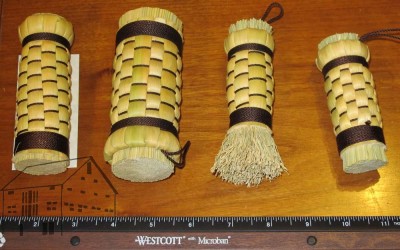
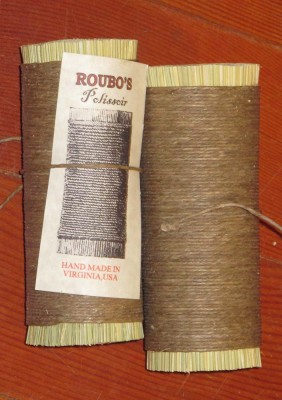
As for wares this time I think we will have only polissoirs and beeswax. To simplify the process I have priced all the 1″ polissoirs at $20 and both of the 2″ polissoirs at $40 (unfortunately despite the “non-existence” of inflation I have recently had to raise the price of the Model 296. On the other hand I lowered the price of the standard 2″ just for Handworks to make it easy on Jason, so maybe it all works out.)
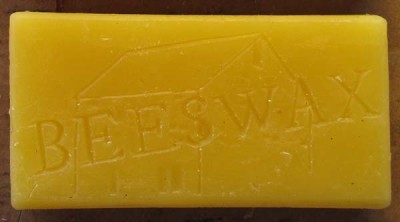
The quarter pound block of hand processed beeswax will be $10.
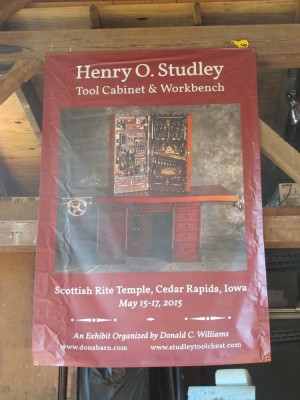
In addition Jason will be able to process ticket sales to the exhibit of the Henry Studley Tool cabinet and Workbench in nearby downtown Cedar Rapids (assuming it doesn’t sell out before then). If you are interested in tickets while at Festhalle, just look for the exhibit banner.
I’m emerging from more than a week of radio silence. I’m not apologizing for it, as I was feverishly selecting, identifying editing, and captioning somewhere close to 500 pictures for VIRTUOSO: The Tool Cabinet and Workbench of Henry O. Studley. This was from an inventory of over 6,000 photos in my computer, which does not include the ton of pictures Chris took nor the ones Narayan was not happy with. I would guess that if you gathered all the files from each time we snapped a picture it would number somewhere north of 10,000. I had begun the process about the time I submitted the written manuscript a month ago, but it resumed in earnest once Chris had the manuscript edited for me to work with two weeks ago.

This does not include the glamor shots or other photographs that will be employed as galleries or visual punctuation as Chris Schwarz, Wesley Tnnner, and Narayan Nayar hammer out the final design and layout for the book. It would not surprise me in the end if the book has up to 600 illustrations. I’ll have to look it over one last time, but we have had enough conversations that I am certain they know what I want it to look like.

For tomorrow afternoon I have a handful of photos to shoot (literally, less than a dozen) then I will let the manuscript sit unstirred for 24 hours and read it one final time before washing my hands of the whole thing as I send it to land on Chris’ desk with a plop on Monday.
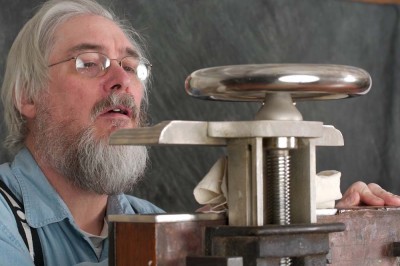
Good riddance, I say. Come next week I will be free from my chair to work on the firewood pile, the new door for the root cellar, trying to impose some sort of order in the barn, continue reviewing Roubo 2, working on the preparations and marketing for the exhibit of the Studley collection…
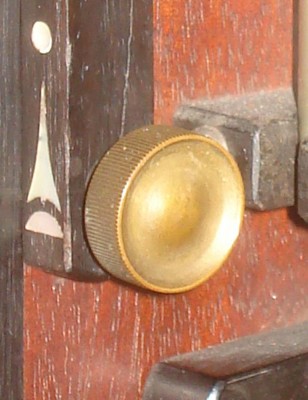
Ninety miles from the Studley-era piano maker’s workbench was the finest Studley-inspired tool cabinet I have seen. No, it wasn’t Studley, nothing else is, and it is not yet finished as there are still many tools destined for it, but I cannot imagine any serious woodworker not wanting this hanging on the wall above their bench.
The maker is a tremendously skilled fellow whose other projects revealed that like Studley, he enjoyed making intricate and complex things.
Oh, and all the screws are clocked. He wouldn’t bite on my suggestion that this revealed he was anal-retentive/compulsive, he merely replied that it was attention to detail. He was a great sport about the whole thing, and I truly enjoyed my time with him and hope he will make it to the exhibit next spring.
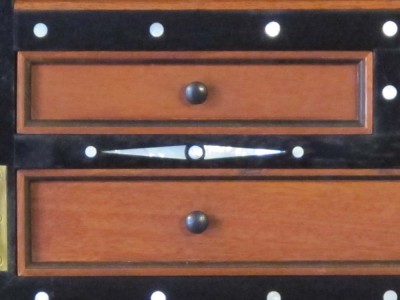
Yup, it’ll be in the book too, in far greater detail and length.
Back home now, and finishing the first rough draft of the whole book tomorrow!
… but certainly blogging quietness.
I’m in the midst of the critical phase where I am weaving the final threads and honing the organization of the VIRTUOSO manuscript. I spent yesterday and today working into the night on the chapter on Studley himself and the winding path the ensemble took to arrive to us today.
That means I have completed the first draft of the introduction, the biography and provenance, the tool inventory with commentary (well, mostly, I have some questions to answer with the microscope in a couple of months), the chapter on the bench and vises is more than half done, the section on Studley’s Masonic heritage is due in a day or two from Spider Johnson, I have a good start on the woodworking-popular-culture chapter, and the conclusion is finished.
I hope to have the first draft complete enough in a week or so that I can send it to Narayan so we can start 1) picking out the mere multitude of pictures from the book from among the bazillion we have, and 2) outline the photographic and informational needs we have for the upcoming final trip.
Stay tuend.
Recent Comments