
My original work on artificial tortoiseshell was presented in Amsterdam almost exactly twenty years ago. I think the conference publication was about eighteen months later.
Here is the link for the PDF on my “Writings” page:
Don_Williams_TDS_Amsterdam_+2002_larger_file.pdf
One of the outcomes from my current developments will be an updated and more detailed monograph to be posted in that same directory. I’m also noodling a video on the whole process. My videographer Chris is now much harder to schedule, with a full-time job, a new/old house, and a wife and two tiny kids, so I will probably try to figure out how to do two-camera filming in the studio. My digital SLR has a microphone port so I think all I need to do is start figuring things out.
Stay tuned.
P.S. I will probably make some full blown tordonshell in the coming fortnight based on my latest results.
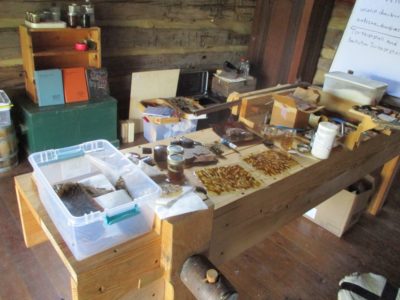
Many years ago, when I was Director of the Smithsonian’s Furniture Conservation Training Program, I was meeting individually with each student in preparation for their fourth-year fellowship, during which they were required to undertake a project that would result in their Master’s Thesis. The students had great latitude in their projects, some were purely historical aesthetics, some were about historical technology or craft, and some were analytical.
After our conversations I would arrange for each student to have a “mentor” to help them with guidance along the way. For those projects reliant on analytical data I brought in a highly respected statistician with a specialty in experimental design and data analysis to advise the students in designing their project, gathering data, analyzing that data and formulating the conclusions. One of the great beauties of DC is the abundance of research institutions and their scholarly communities. (The stories the statistician told me sotto voce about “research” shenanigans made me distrustful of any “science” ever since, even before the anti-“science” of the past three years. One tale literally revolved around a “researcher” bringing in a box of lab notebooks and dropping them on the statistician’s desk the with the instructions, “My conclusion for this project is XYZ so you need to review this data and arrive at this conclusion.” As the experimental designer told me then, “science” is not a thing, science is a process, and if the process is corrupt then the outcome [data and conclusions] is worthless. From that perspective I can barely withhold laughter when public luminaries now tell us to “follow the science.”)
Back to my student. The topic proposed for the thesis project was an evaluation of shellac properties, the particulars are lost to me at the moment. I only remember that the number of variables combined with the number of identical samples required for a statistically valid set of results would have require formulating and preparing approximately seven million samples. Needless to say, the student changed their project rather fundamentally.

Which brings me to work I am undertaking in the studio right now and probably for weeks or months to come. I am not the trained experimental scientist in this household — that would be Mrs. Barn — but I am fairly able to harness and focus my curiosities from time to time. My demonstration of making my artificial tortoiseshell several weeks ago has re-lit that fire for me and I have been working on refining the formulation and process ever since. Although my paper from two decades still stands up well, it only gets about >95% of the way to a really good imitation vis-a-vie the physical properties of genuine tortoiseshell. >95% is not the same thing as ~99%, which is where I want to go.
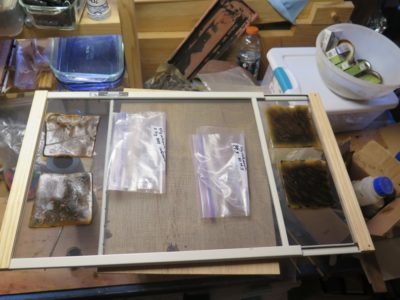
Like my student’s those years ago every variable change requires a group of samples to be formulated and made. Unlike the putative shellac researcher I am NOT weighing each variable as random and equal. I am not making the number of samples that might be required if the variables were purely random; I am testing one variable first, then applying the second variable once the first spec is established, then the third once the first two are established, etc. Even so I am creating hundreds of samples to assess for their properties based on a menu of options I must consider.
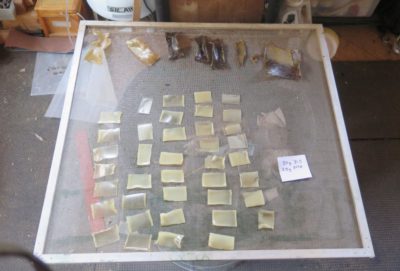
What grade of collagen should I use?
What concentration?
Which plasticizer (if any)?
At what concentration?
Which protein reaction catalyst to use?
In what proportion?
In solution or infused ex poste?
How long to cure?
At what temperature?
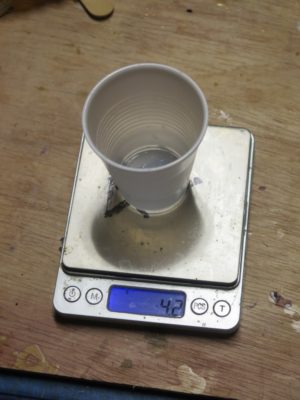

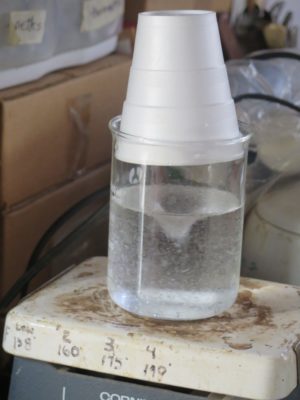
My tools for this undertaking are fairly simple and non-specialized; an analytical digital scale, disposable pipettes, disposable cups, a old microwave, an ancient ebay stirring hotplate, a rice steamer (most samples curl when they dry and need to be steamed flat), drying screens, and a desiccating chamber, a/k/a a Gammo pet food storage unit filled with conditioned silica gel. By far the most time for the sample involves drying them to the lowest moisture content possible, at which time the most extreme properties become manifest. Yes indeed, most of the time is watching samples dry.
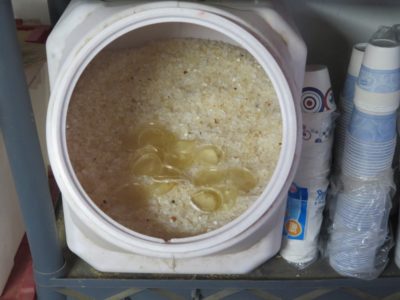
There is simply no point in ongoing daily blogging about that, or in changing formulations by a hundredth of a unit proportion, but I will report back when I have results that I find encouraging in directing my final minute adjustments. In the meantime when there is radio silence on the blog, you can assume I am either splitting firewood for next winter and beyond, or tinkering with formula minutiae.
One of my real headaches at the moment has to do with a German chemical component that has a) become unavailable, or b) become unaffordable. My current dwindling inventory was a 100g jar given to me by the president of a chemical company almost twenty years ago, and in the intervening years I have seen the price go from a couple hundred dollars a kilo to several hundred dollars per kilo to a few thousand dollars a kilo to a quote yesterday of almost $100k per kilo. I’m really wishing I’d bought a big bucket of it fifteen years ago. Obviously, I am doing my best to work around that headache.
Stay tuned.
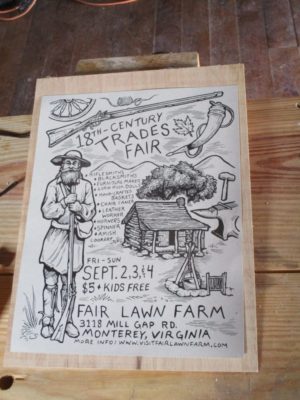
Some months ago I was approached by my friend TimD, who was organizing a “Historic trades” weekend at his place with fellow gunsmiths, horn workers, blacksmiths, weavers, etc. Tim is an accomplished craftsman, primarily making flintlock rifles and associated accessories like powder horns. So, he was gathering a number of friends and acquaintances for a weekend shindig open to the public and he asked me to demonstrate making my Tordonshell to the crowds. It was a peculiar technology to include but I was delighted to participate. I spent three days on display and explained Tordonshell to literally hundreds of attendees.
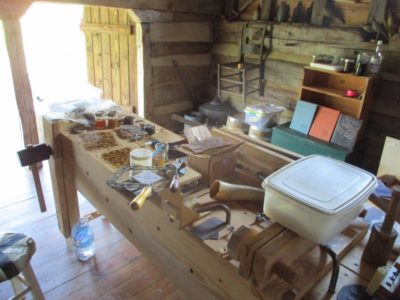
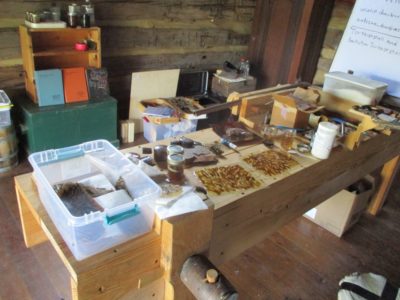
I was set up to occupy Tim’s gunsmith shop, a reconstructed late 18th/early19th log structure, using the partner’s workbench I built for him a few years ago.
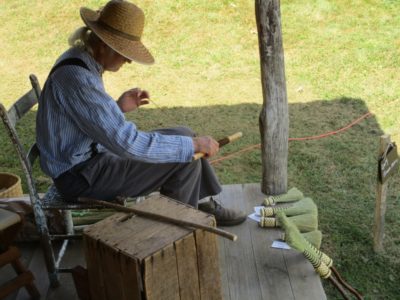
The front porch of the shop was occupied by other artisans including a wool spinner and my very own polissoir-maker Gary.
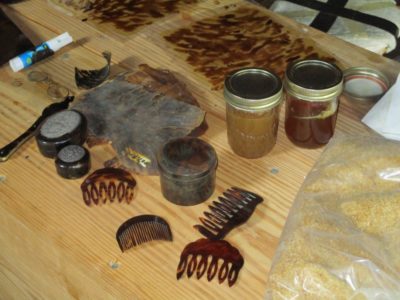
I was frankly surprised by both the number of visitors I had, and the intensity of their interest in both genuine tortoiseshell and my imitation of it.
Next year’s event is already on the books for Labor Day weekend and is expected to have around 30 demonstrators. I am already at work for my demonstrations, as I will be making things out of finished Tordonshell as opposed to making the Tordonshell itself.
I hope you can join u there.
Labor Day weekend will be the inaugural 18th Century Craft shindig here in Highland County, where I have been asked to demonstrate tortoiseshell craft. Events | Fair Lawn Farm (visitfairlawnfarm.com
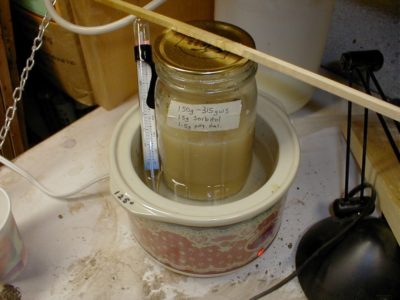
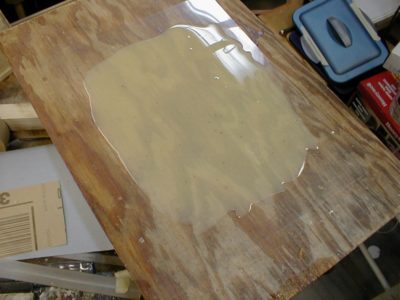
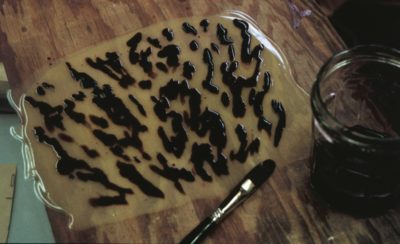
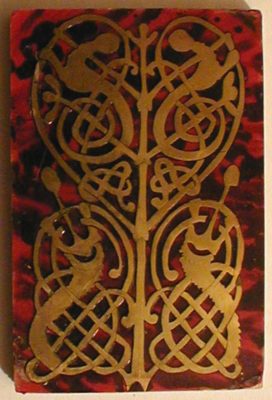
Since tortoiseshell is a restricted material I will be focusing my efforts on the making and working of tordonshell, a convincing substitute I invented many years ago so that I could make Boullework, starting with a pot of hot hide glue and a few select additives. At the time I was contemplating patenting the formula, but then I con$ulted with a patent attorney and found out how much it would co$t to go through with it. Phooey on that, I just published the paper and moved on. (The estimate wa$ for a completed application and patent to co$t $25-50k.)
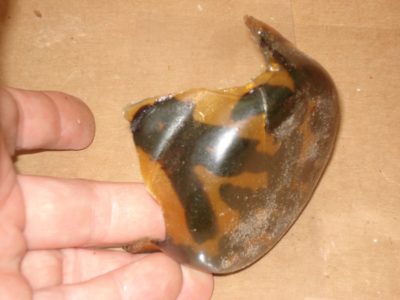
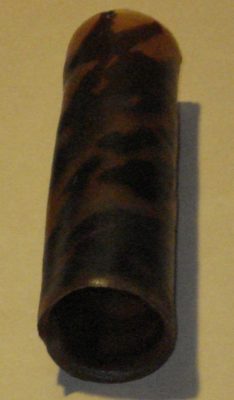
Along the way I made a lot of tordonshell things to make sure it mimicked tortoiseshell accurately, which will be of great interest to the powder horn crowd.
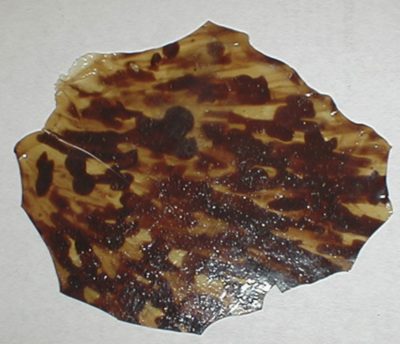
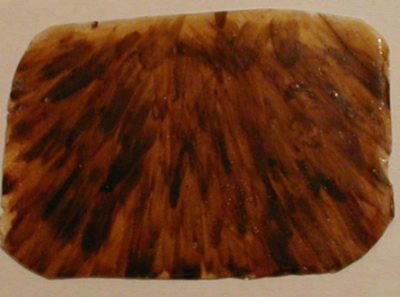
For the rest of this week and into next week I will be gathering the materials and rehearsing the demonstrations, beginning with discussions of the materials themselves and the making of tordonshell so that all the attendees can go home and make it themselves to use in their own craft work. It will also be a dry run for my next video project which I hope to begin filming this winter. I keep telling myself I cannot start a new one until I get the Gragg Chair video edited and posted on line.
After two years of mostly inactivity teaching-wise I’ve got several now on the calendar, all more or less in the vicinity. Over the next couple weeks I will be diligently preparing for my presentation at the SAPFM Mid-Year in Fredericksburg VA, on the topic “The colonial craftsman’s finishing kit,” with a special emphasis on locally available materials. If you are there you can come and see it, if not, not.

For this presentation I am creating a set of sample boards to reflect the information I am presenting.
No sooner do I return home from that than I will be assembling all the materials for the three-day Historic Woodfinishing Workshop near Charottesville VA. I’ve done this workshop several times and have settled on a well-defined syllabus to leave the students with greater confidence in the finishing process.
Over Labor Day weekend my friend Tim, for whom I built the ginormous workbench a couple years ago, will be hosting an 18th century craft shindig at his place just a few miles form here. He has asked me to demonstrate historic wood finishing and tordonshell work. Ought to be a boatload of fun.
It’s the best of all worlds in a way. I get to teach and interact with talented people in a range of skilled trades without having to even travel!
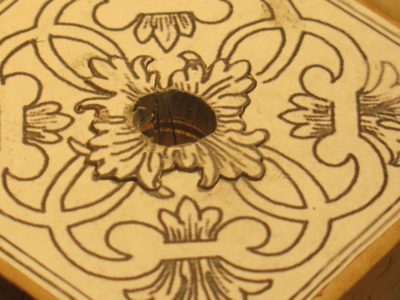
As I continued preparations leading up to last Saturday’s Boullework presentation to the SAPFM Blue Ridge Chapter I was able to make good progress once I discovered the cause of my earlier frustrations. Which was, as I realized once the initial center cut was completed and the material removed, that the first blade break resulted in a small fragment being embedded in the kerf. Every succeeding blade was damaged by encountering this fragment, continuing the sawing difficulties. When you’re talking 0000 blades it does not take much to throw them off.
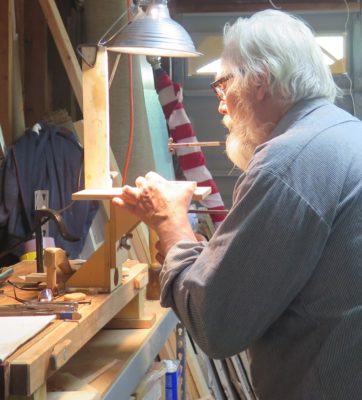

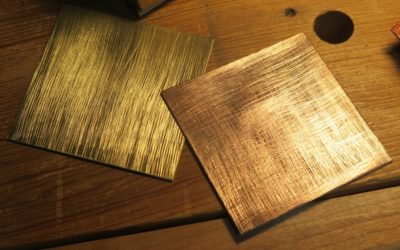

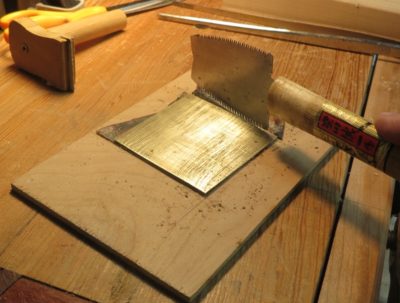
Getting a little more sawing done and assembling the demo materials was pretty straightforward.

I even made a scute of tordonshell. Fun, fun, fun.
PS Since I am on the home stretch for reviewing the Gragg chair video (probably about a dozen finished half-hour-ish episodes plus a bonus episode or two) and creating the edit sheets for the project, I am casting my brain forward to next winter. I am thinking about a shorter series on Boullework, Don-stye. Or at least revising and updating my original monograph from my presentation in Amsterdam.
It’s been quite a while since I 1) did any Boullework and 2) made a public presentation.

The last week or two I’ve been going through the exercises I’m demonstrating this coming Saturday to the SAPFM Blue Ridge Chapter, everything from making tordonshell to cutting some new Boullework panels.

When I assembled the metal and tordonshell packet and set about to sawing, the magic just wasn’t there. On a normal day once I get in the rhythm I can go for an hour or longer per saw bade, sometimes even half a day. But not this particular day. Sigh.

I was snapping blades like I was trying to break pasta. It took me four hours to saw a 1/2″ circle (and a pretty raggedy one at that) and I broke more than two dozen blades in the process. When I swept up the pile was truly impressive, but my camera was not handy.

Bad posture? Bad lot of blades? (it really does happen some time) Packet too thick? Rusty antiquated shoulder? Vision problems? (well, that is a given)
Some days are just like that. I’ll aim to get the bear tomorrow.
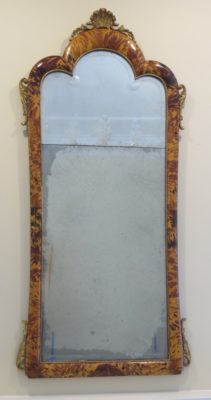
Recently I had some time to spend working on a pair of early 18th Century Italian friends near Mordor. As is almost always the case with wooden objects veneered with tortoiseshell, the delamination problem is never really solved as the wooden substrate and the mostly thermoset protein polymer veneer react to moisture changes at different rates. In this particular case that problem has been exacerbated in the distant past by the traditional housekeeping practice of slathering tortoiseshell with olive oil and linseed oil. The practice is deleterious is every way, especially over time.

This time there were two sections of tortoiseshell that had become fully detached like this one, they were reattached with 192 g.w.s. hot animal hide glue after cleaning the substrate.
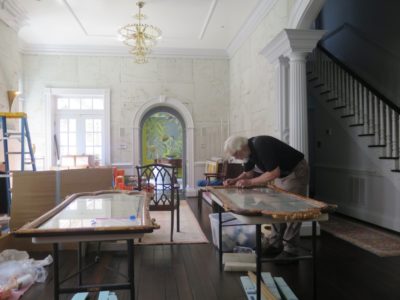

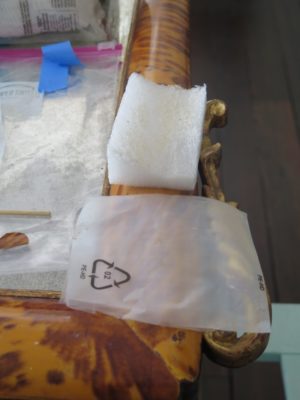
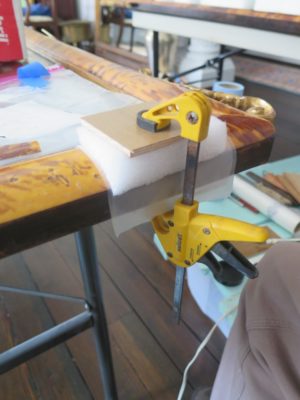

Then I worked my way around the mirror frames and identified a dozen places with delamination but not detachment and laid these back down after working glue underneath.
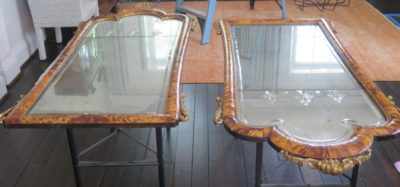
In the end I cleaned up the surfaces and applied a thin layer of Mel’s Wax over the surface.
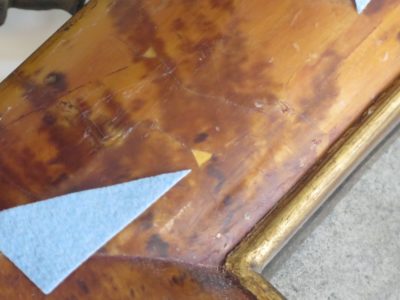
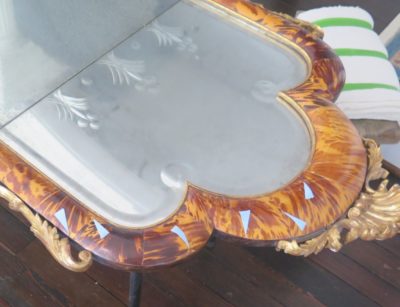
I also documented the two dozen small losses on the frames; these are not detrimental per se and the client may want me to address these losses at some point in the future.
For now they are back up on the wall doing what they are supposed to do – look beautiful. I no longer accept new clients, but expect to care for these old friends as long as I am abe.

I’ve signed on as one of the speakers for a Spring 2022 conference at the Winterthur Museum on the subject of marquetry. Like many other events over the past two years it has been scheduled, cancelled and re-scheduled, to the point where I am not fully informed myself. (In 2020, 13 of my 13 teaching and speaking gigs were cancelled. It was quite delightful to not travel much, hunkering down in Shangri-la instead [“social isolation” is any day ending in “Y” here in the hinterboonies]) I believe it is in late April but don’t hold me to that. I won’t discuss the other speakers yet as I think the Program is still being finalized, but my presentation and subsequent publication will be on the topic of Boullework.
I have already sketched out my presentation/demonstration in my mind, bringing it into realm of reality will occur over the next eight months. That progress will be documented periodically on this screen.
This is a demonstration-heavy gathering, so if the topic interests you it would be a great opportunity to interact with some very passionate and accomplished folks, both on the stage and in the audience.
Winterthur is a few miles north of I-95 in northern Delaware. I worked there while going through college and have many fond memories of it, both the grounds and museum are magnificent.
Stay tuned.
Recently while working to impose order to the library of the Barn I came across a pile of articles needing scanning and formatting for posting to the web. “Tortoiseshell and Imitation Tortoiseshell” was my contribution to a 2002 conference that required travel to Amsterdam for the presentation itself, in complete disregard to one of my personal mottoes, “If I ain’t at home, I’m in the wrong place.”
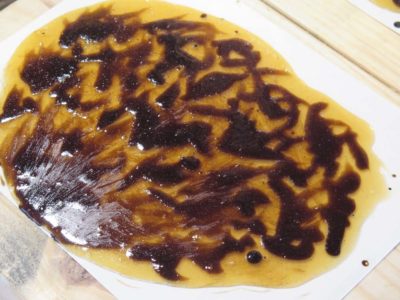
The scanned article is now in the “Conservation” section of the Writings section of the web site. There are two versions, one about 4.5 megs and another about 1.5 megs. I’m still working through the idiosyncrasies of my scanner and compewder, figuring out what settings work best. If I can get this better I will upload that version later.
Recent Comments