I recently spent a week at the Marc Adams School of Woodworking, teaching two three-day courses. I believe this was an experiment on Marc’s part, road testing some new scheduling concepts such as a three-day workshop during the week as opposed to only on weekends.
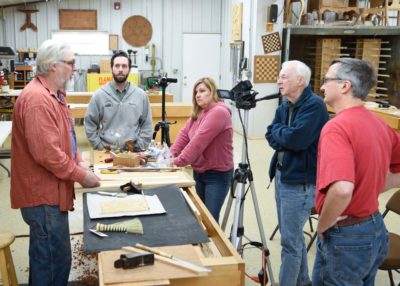
The Parquetry workshop had three enthusiastic attendees (plus a most excellent teaching assistant), a number the Marc told me precludes any repetition of the topic. This is an entirely fair conclusion on his part as he has a huge footprint to support. With several classrooms in simultaneous use I’m guessing he needs somewhere between 35-50 attendees every day for six months to make it work.
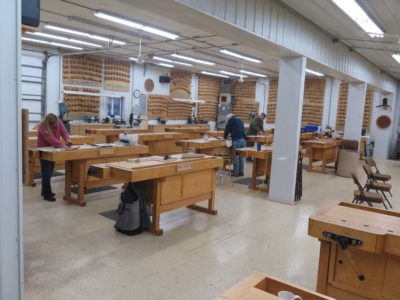
In fact our merry little band was in a huge, well equipped classroom with twenty (?) workbenches. The spaciousness was both unnerving and delightful as the students could spread their projects as widely as they wanted.
This workshop is somewhat unusual for me in that there was a finished project at the end, while I tend to prefer teaching a skill-set rather than a project.
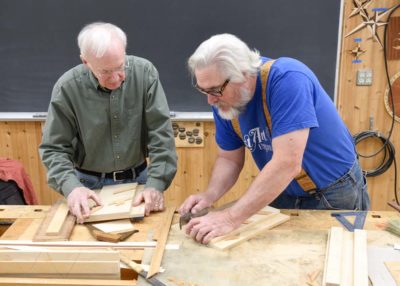
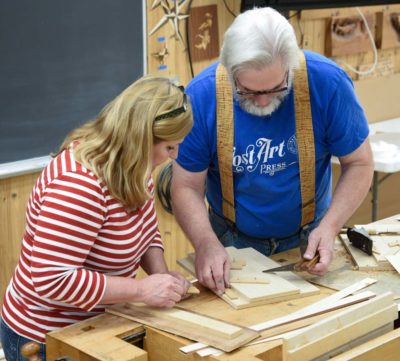
But skills and processes were taught and practiced, including the making of sawing and planing jigs,
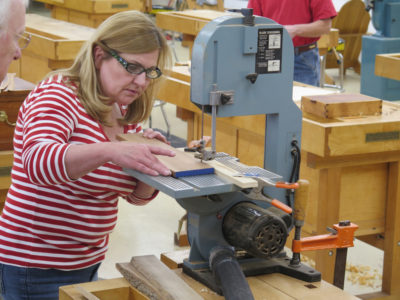
sawing veneer stock for making the patterns,

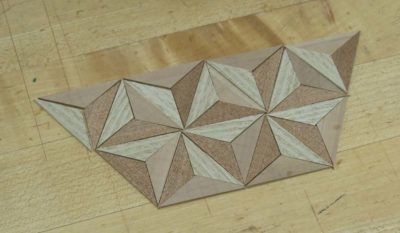
the assembly of the patterns,
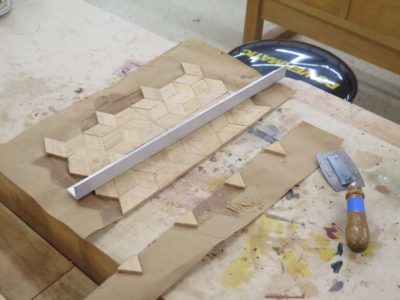
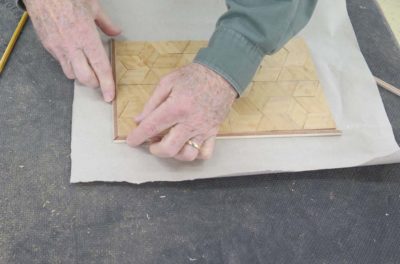
fabricating and integrating simple bandings,
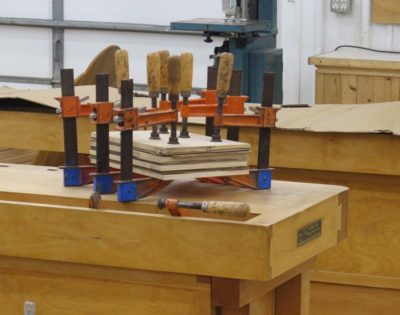
and gluing them down to a substrate.
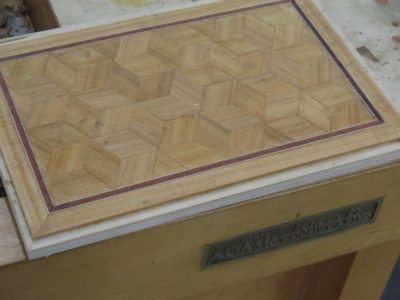

In the end they were cleaned up with toothing planes, files, and scrapers making them ready for the finishing process.

Though I will not be teaching this workshop again at MASW, I will not completely set the general topic aside. I am hoping to have a workshop on knot-work banding perimeters there in 2019.
After long and careful consideration, I have concluded that I simply cannot host any workshops at The Barn this coming summer. The combination of the Studley book and exhibit, brutal winter aftermath with a mountain of things to do on the homestead, projects that have languished in the studio, and the need to wrap-up Roubo on Furniture Making (almost twice as large as Roubo on Marquetry) leaves me with no time nor energy to dedicate to workshops at the barn. I had planned on a historic finishing workshop in late June, but that will have to wait until net year. In September I will host a week-long workbench build for my friends of the Professional Refinishers Group web forum.
This is not to say I will be entering my long anticipated hermit phase. My presence and teaching elsewhere over the summer will be evident. Check these out.
Henry O. Studley Tool Cabinet and Workbench exhibit – May 15-17, Cedar Rapids IA
Making New Finishes Look Old – Society of American Period Furniture Makers Mid-Year Conference, June 11-15, Knoxville TN
Gold Leaf and its Analogs – Professional Refinisher’s Group Groopfest, June 24-26, Pontoon Beach IL
The Henry Studley Book and Exhibit (breakfast banquet address) and Roubo Parquetry (demo workshop) – Woodworking in America 2015, September 25-27, Kansas City MO
Last Friday on my way to the annual banquet of the Society of American Period Furniture Makers at Colonial Williamsburg I took the opportunity of my foray into “civilization” (or is it “out of civilization?”) to make a number of stops purchasing materials and supplies for ongoing and upcoming projects.
Perhaps the most important of these stops was at Virginia Frame and Builders Supply in Fishersville, just a hundred yards or so from I-64. Virginia Frame is renowned for having large, long, and lovely lumber in stock. I bought some 24-foot long southern yellow pine 2x12s, mostly clear and some even select. Since my pickup has a 6-foot bed, the folks at Virginia Frame cut the 24-footers into 8-foot sections and we stacked and strapped them into the bed for the long ride to Williamsburg then back to the mountains.
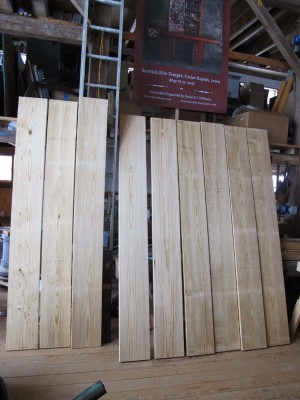
This September I will be hosting ten members of the on-line forum Professional Refinishers Group, a treasured mostly-virtual community to which I have belonged for many years, for a week of workbench building. The lumber from Virginia Frame will serve as the raw stock from which I will make a Roubo prototype and a Nicholson prototype, to work out all the bugs in the fabrication process. Once I do I will order the same lumber as necessary for all the workbenches being built in September.
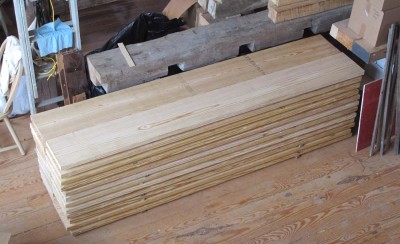
There was rain on my trip, so when I got back Saturday afternoon I spread out the boards to let them dry, then yesterday morning I stacked them to allow them to sit properly before I build the benches in February and March. I love working with southern yellow pine, and these boards are magnificent.
But first I have to make a replica of the Henry O. Studley workbench top for the upcoming exhibit.
The day began with the excitement of seeing the glued-up panels. We had slightly oversized 1/2 baltic birch plywood for each of the panels so that they could be trimmed precisely to size one the project is complete.
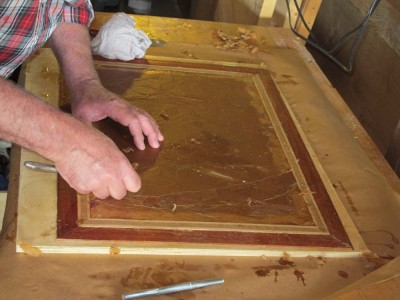
The first step to getting finished from this point was to moisten and peel off the kraft paper that served as the support for the assembling of the pattern, banding, and border.

It was a delicate balancing act, moistening the surface enough to remove the glued-down paper, but not so wet as to lift the veneers. Once the paper is removed begins the tiresome task of dampening and scraping off all the glue left behind.

A quick stint on front of the fan to dry them, and then we brought out the toothing planes, scrapers, and small planes to get everything flat and smooth.
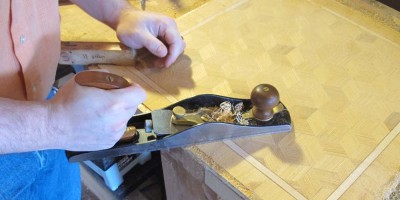
The conditions of the panels,
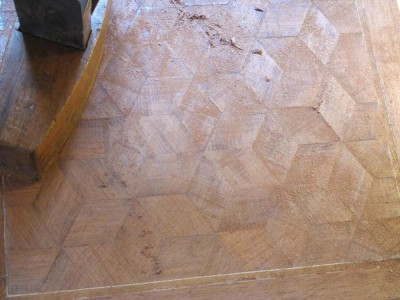


and the floor indicated we were making great progress.

In a normal 3-day parquetry workshop this would have been the final process,
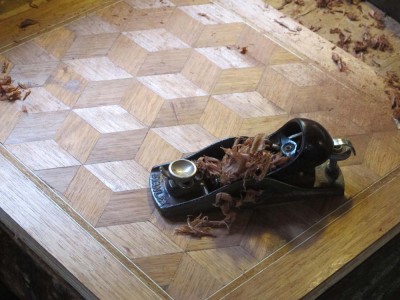
but these guys were working so efficiently we made it all the way through a finished project by the time they left.

Using one of my panels, I demonstrated the simplest finishing approach to the parquetry, and they charged ahead.

Burnishing with polissoirs came next,

and then the molten wax treatment for the final finish. The wax was first dripped on the surface, then trowelled around with the tacking iron. Again it was important to use the iron delicately to melt the wax enough to impregnate the surface, but not to heat the surface enough to lift the veneer.

Once the surface was fully impregnated the panel was set aside to let cool and harden, then the excess was scraped off,

and the remaining surface was buffed with a linen rag.
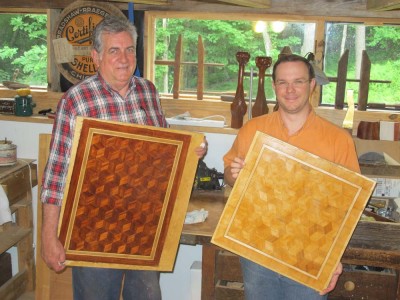
The results were eye popping, and demonstrated what can be done with very little wood in a short while. If you snoozed on this one, you loozed. Joe and Joshua now possess another important tool for their design and fabrication toolkit for the future, and when they get home they both plan to trim their panels and build a small table around them.
Great job, guys!
The goal for the weekend, thus the goal for the day itself as the final one, was to allow each student to leave with a fairly complete Roubo parquetry panel. The pace of the day was then almost by definition a peripatetic of not frenzied one.
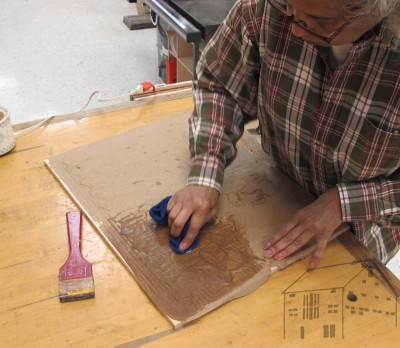
After opening the gluing set-ups each student was faced with a glued-down panel with a heavy layer of brown craft paper on the surface. Gentle work with a dampened sponge or rag combined with scraping with a scraper or knife resulted in a cleaned panel ready for trimming on the edges to allow for fitting of the banding. The trimming was accomplished with a straightedge and a utility knife or veneer saw.
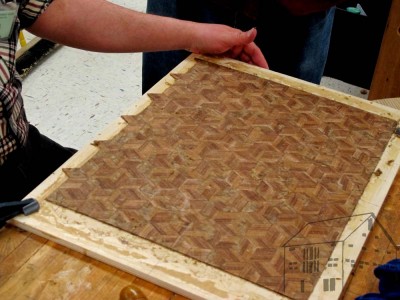
With strips of the banding glued up on day 2 each panel was fitted with the decorative detail.
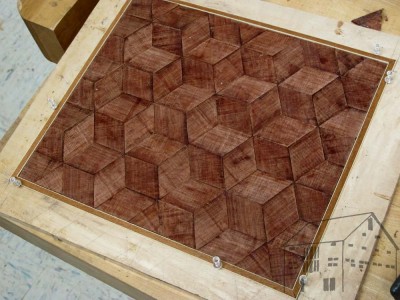
One of the delights of traveling and teaching is the opportunity to learn new things. In this instance, I learned that Utrecht art supplies carries an aluminum-head push pin, a necessary and useful tool for pinning the banding in place while the glue sets. I’ve been making-do with plastic headed pins, but until now had no success in finding the aluminum head ones. I left for home greatly pleased with the new information and source. My great thanks to Ms. S for finding them and bringing some to class, and for letting me buy her stash from her.

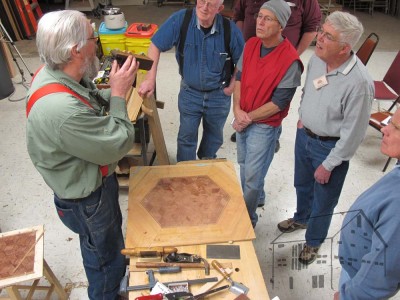
Once the students had their banding glued and pinned, while that was setting I took the opportunity to demonstrate flattening the surface of a parquetry panel with a toothing plane, smoothing it with a scraper, and finishing it with molten wax and water-wax. The students did not get to try all of these methods, but the techniques are simple and the students promised to finish them at home.
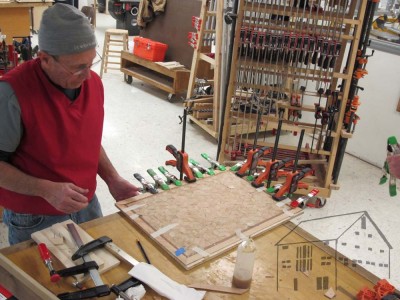
Once the banding was set, borders made from strips of the veneers used for making the original lozenges were fitted and glued as a longitudinal border around the perimeter of the panel.
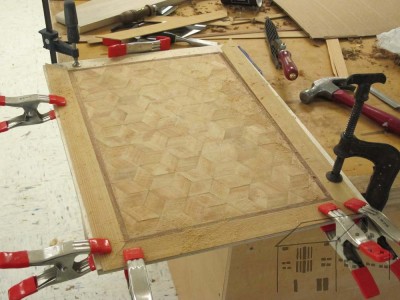
By the end of the day, everyone had their panel in “take home” condition, now equipped with a new technique to apply to new projects. Several of the students indicated that those new projects are either underway or in the planning stage.
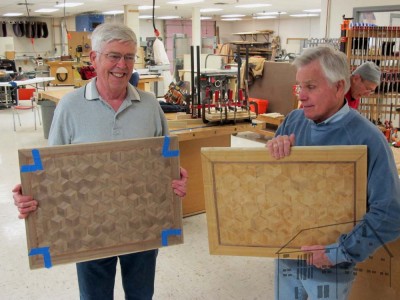
If this workshop interests you, you can sign up for the July 18-20 rendition of the identical project at The Barn, by dropping me a line here. I look forward to seeing you soon.
As is often the case for the second day of a three day workshop, the atmosphere was one of quiet work and little instruction or lecturing. Since the objective for the day was to get everyone’s parquetry assembled and ready to glue to the plywood base, there was lots,
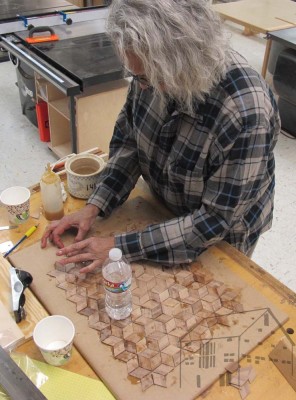
and lots,
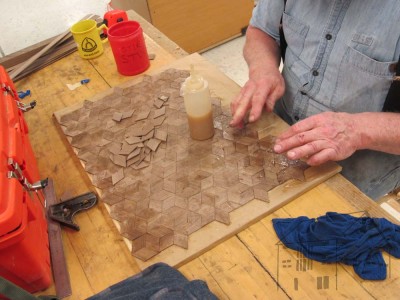
and lots of gluing parallelogram lozenges down to the kraft paper.
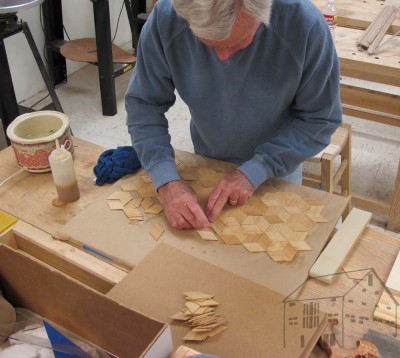
As usual, whenever somebody got theirs ready to go they jumped in to help the next person get theirs ready.
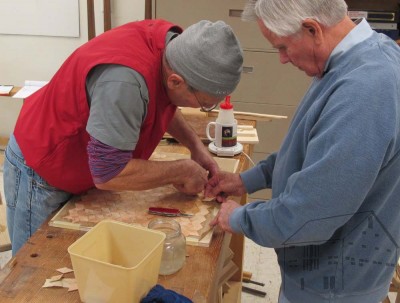
In addition, we needed to get the loaves of banding glued up to slice first thing in the morning of the third day.
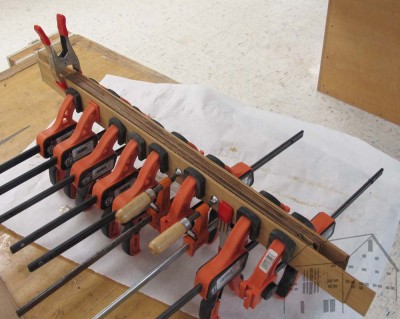
Finally everything was glued up and we called it a day.
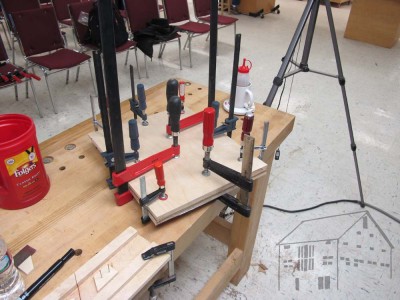
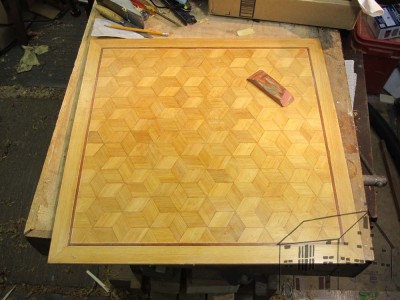
Last weekend I taught a three-day workshop on creating this parquetry panel a la Roubo for the Kansas City Wood Worker’s Guild, a delightful host if ever there was one.
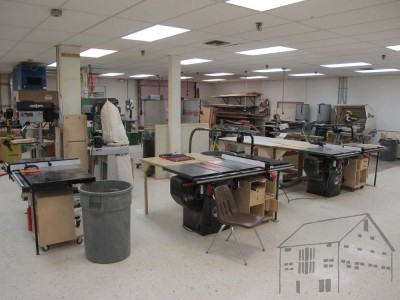
All you’ve heard about the Guild, its membership, and space is true and then some. they are positively at the top of the food chain studio-wise with a nice lecture space, and complete bench room, and a machine shop to die for.
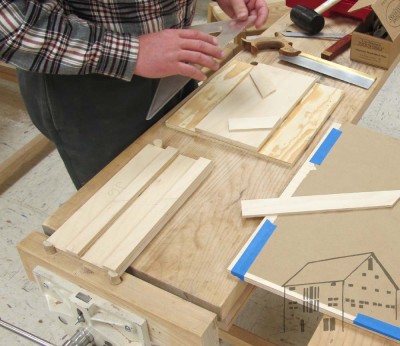
The first day began with a discussion of the project in general, but more importantly several specific tasks to get things started. First was the construction of two jigs necessary for the cutting of the 60-120-60-120 parallelogram lozenges that comprise the parquetry. One of the Guild members had prepared all the baltic birch plywood to make them, so all we had to do was cook some glue and assemble them.
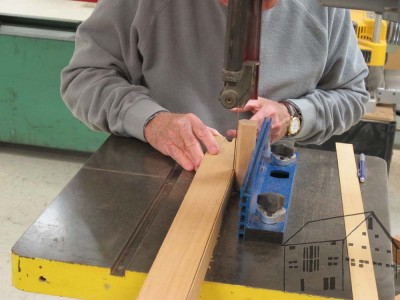
Next came the ripping of the lumber into the veneer strips from which the lozenges were cut.
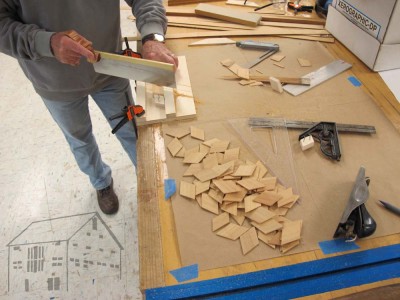
Following that was the cutting of lozenges. By the hundreds.
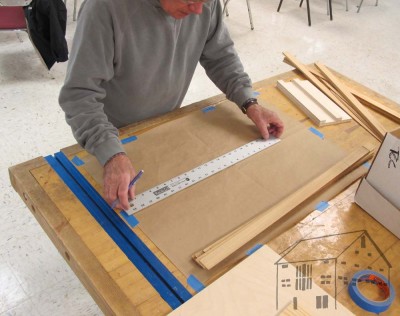
Since the pattern is first assembled and glued precisely onto heavy kraft paper, the needed to be divided exactly on both axes.
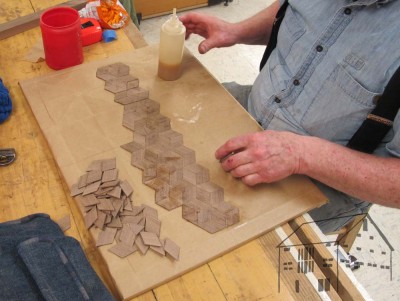
Finally came the assembling and gluing on the paper. this is actually more difficult than it seems and can be quite a challenge for newcomers until they get the knack of it, something I will be addressing in a blog in a week or so unless the spirit moves me to make it sooner.
More tomorrow.
The past couple weeks I have been assembling and packing the supplies I need to teach the Parquetry class at the Kansas City Woodworker’s Guild next weekend. I will be repeating this class at The Barn in July so you can get an idea of the syllabus for that too.
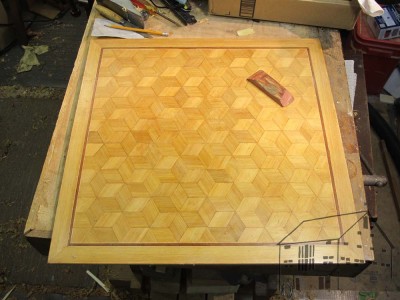
The preparation has been both frustrating and delightful, frustrating because so much of our material possessions are in chaos with the ongoing move, but delightful in that it allowed me to experience the parquetry process all over again, including the making of this panel.
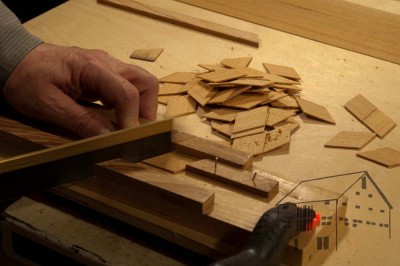
During the class we will be making all the jigs, cutting the veneer strips and lozenges,
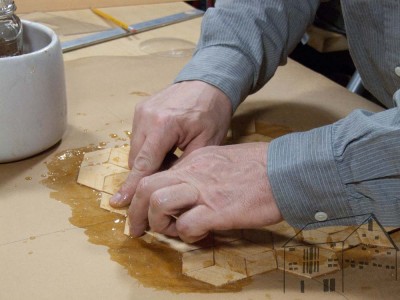
assembling the pattern,
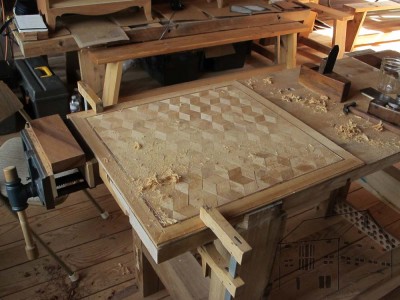
planing,
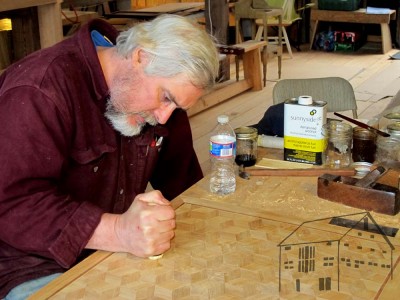
polishing, and completing the panel in this design, although the dimensions will be a bit different, and ending with a beeswax finish just like the originals back in the 1700s.
If you are interested in coming for the July class at The Barn drop me a line here.
While prepping for my upcoming visit to the Kansas City Woodworking Guild to teach a class based on Roubo’s Plate 286 I was casting about for my inventory of toothing planes. I can find three of them, but the other half-dozen are MIA. If you happen to know where I put them, please let me know.
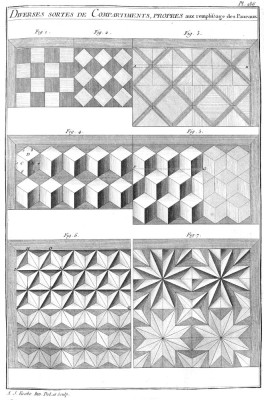
In lieu of finding my remaining stash of planes I revived an old homemade tool idea from the mists of the distant past. A word of caution: this will take almost five full minutes to make it with a cost of zero, so don’t say didn’t warn you. You will need 1) a block of scrap wood, 2) a hacksaw blade, and 3) a pair of metal shears.
Step 1 – Find a block of scrap wood. Cut it to about 6 inches long.
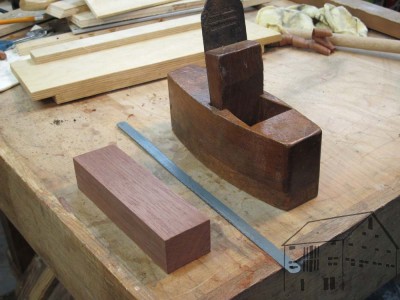
Step 2 – Find a hacksaw blade, and cut off a piece equal to the width of the block.
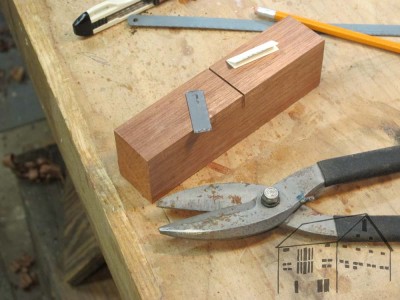
Step 3 – at abut the center of the block, on the side of the block mark the depth of the blade body to the base of the teeth.
Step 4 – Using a saw (in my case I used my band saw) cut a kerf to the depth you marked in Step 3.
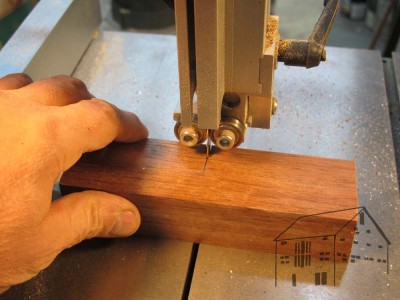
Step 5 – Ram it home. if necessary add a small shim of paper to the kerf to make sure the blade fits tightly. Adjust the blade so that the teeth tips are exposed about 1/16″.
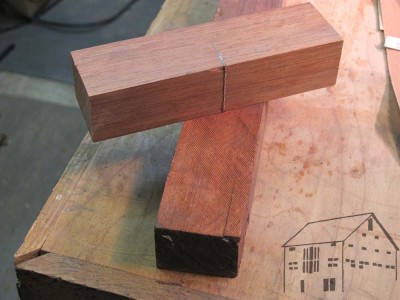
You now have an inelegant but functional toothing plane, a necessary tool for dealing with sawn veneer marquetry.
Step 6 – I will cover this in Part 2.
As far as I know these are my teaching/hosting commitments for this year.
March 8/9 and 15/16 – For the next two weekends I will be demonstrating at my pal David Blanchard’s shop on Main Street in Monterey VA during the Annual Maple Festival. If you are in the neighborhood stop in to say “Hi.”
March 21-23 I will be teaching a parquetry workshop at the Kansas City Woodworkers Guild.
May 30 – June 1 will be the Finisher’s Retreat, an annual event I host for the two chapters of the Society of American Furniture Makers in which I am active. This year it is the Virginia Chapter. For more information contact Bob Mustain at mustainrw@juno.com
June 24-26 The Eighth meeting of the Professional Refinisher’s Group, and the third time the event has been at The Barn. For more information, contact Ben Myre at bcmyre@hotmail.com.
July 18-20 will be a weekend parquetry workshop at The Barn.
August 11-17 will be a week with plane maker Tod Herrli at The Barn. the first three days will be a workshop on making a hollow-and-round pair, the next four days will be something a bit more advanced; topic not yet finalized.
September 12-14 Woodworking in America, Winston-Salem NC. I will be presenting two topics, the first being Traditional Finishing and the second being Gold Leaf.
October 3-5 will be a weekend workshop in Boullework Marquetry at The Barn.
October 21 I will give a presentation to my dear friends of the Washington Woodworker’s Guild. At the moment the topic is probably Inlaying Pewter.
When you combine this schedule with settling in out in the mountains, submitting the manuscript for To Make As
Perfectly As Possible: Roubo on Furniture Making sometime in April-ish, and the manuscript for Virtuoso: The Tool Cabinet and Workbench of Henry O. Studley some time around Thanksgiving, it seems like a pretty full year.
Recent Comments