In the run up to summer activities at The Barn — the Professional Refinisher’s Group gathering in June, the Parquetry workshop in July, Planemaking with Tod Herrli in August, hollows-and-rounds and advanced planemaking, and the Boulle Marquetry workshop in October (there are still spaces for all workshops) — there were many high priority housekeeping issues. High on the list was the fact that there were still sections of the siding that provided no impedance to the encroachment of nature.
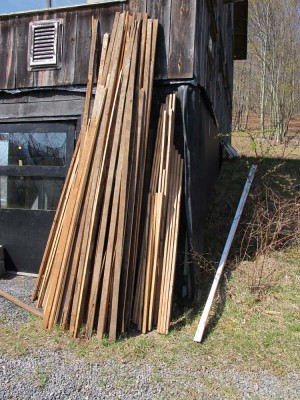
Last month my pal Tom and I cut probably a thousand linear feet of battens to close up the gaps between the siding boards, and that project continues as a filler between every other of the 12, 691 top priorities in my life. Combined with a generous application of spray foam insulation/sealant in the multitude of cracks I have noticed a dramatic drop in livestock already.
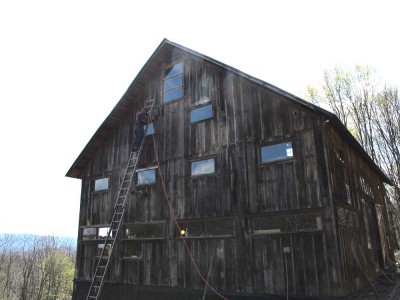
I was also really nervous when I saw tons of wasps buzzing about last month, but since I have robbed them of many nesting places, they seem to have moved on. Three summers ago they built a paper nest literally the size of a bushel basket. Not something you want visitors to be concerned about.
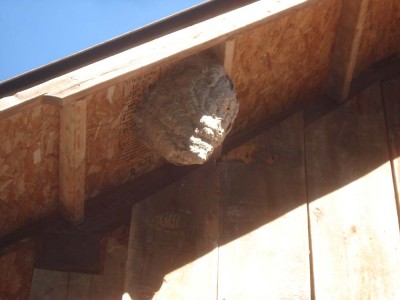
And finally, since the Barn has been a non-stop construction site for almost seven years there is a mountain of construction debris that just won’t go away no matter how many trips I make to the dump. Well, I recently spent several evenings with a roaring bonfire, so even that nuisance is receding.
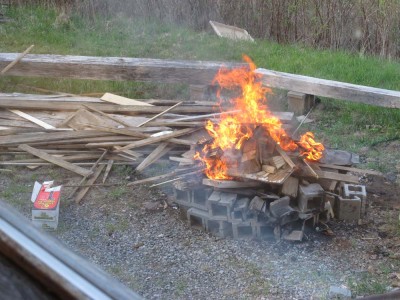
The results were most gratifying.

As far as I know these are my teaching/hosting commitments for this year.
March 8/9 and 15/16 – For the next two weekends I will be demonstrating at my pal David Blanchard’s shop on Main Street in Monterey VA during the Annual Maple Festival. If you are in the neighborhood stop in to say “Hi.”
March 21-23 I will be teaching a parquetry workshop at the Kansas City Woodworkers Guild.
May 30 – June 1 will be the Finisher’s Retreat, an annual event I host for the two chapters of the Society of American Furniture Makers in which I am active. This year it is the Virginia Chapter. For more information contact Bob Mustain at mustainrw@juno.com
June 24-26 The Eighth meeting of the Professional Refinisher’s Group, and the third time the event has been at The Barn. For more information, contact Ben Myre at bcmyre@hotmail.com.
July 18-20 will be a weekend parquetry workshop at The Barn.
August 11-17 will be a week with plane maker Tod Herrli at The Barn. the first three days will be a workshop on making a hollow-and-round pair, the next four days will be something a bit more advanced; topic not yet finalized.
September 12-14 Woodworking in America, Winston-Salem NC. I will be presenting two topics, the first being Traditional Finishing and the second being Gold Leaf.
October 3-5 will be a weekend workshop in Boullework Marquetry at The Barn.
October 21 I will give a presentation to my dear friends of the Washington Woodworker’s Guild. At the moment the topic is probably Inlaying Pewter.
When you combine this schedule with settling in out in the mountains, submitting the manuscript for To Make As
Perfectly As Possible: Roubo on Furniture Making sometime in April-ish, and the manuscript for Virtuoso: The Tool Cabinet and Workbench of Henry O. Studley some time around Thanksgiving, it seems like a pretty full year.
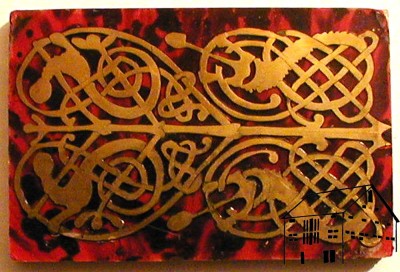
Boullework is the method of composing either pictorial or filigree marquetry employing metal sheet, usually brass, pewter or copper, with veneers of tortoiseshell. Tortoiseshell is now a proscribed material after the CITES Treaty of 1975. Instead we will make our own “tordonshell,” a convincing artificial material I invented for just this purpose, to make a pair of small marquetry panels, one the negative of the other. Some projects may instead use ivory planks for either the metal sheet or the tortoiseshell.
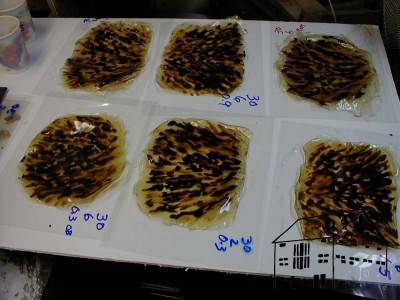
This three-day workshop will be limited to six participants, and will take place October 2-4, 2014, with a registration of $375.
The historic technique of marquetry — the application of veneers in a decorative manner — is so huge that several course opportunities will barely touch the surface. The techniques taught and practiced in the class are exercises based in great part on my own experience and the research done in producing To Make as Perfectly As Possible: Roubo on Marquetry based on L’Art du Menuisier, the monumental 18th century Parisian woodworking treatise by A. J. Roubo, and other historical ante-types documented by other scholars.
Starting with slabs of lumber we’ll make a parquetry and banded panel guided by Roubo’s Plates 286 and 287. We will saw our own veneer (mostly with a power band saw but if you are really motivated we can try my several veneer frame saws) and construct the necessary sawing and planing templates needed for the project.
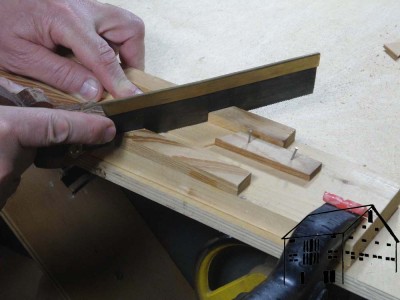
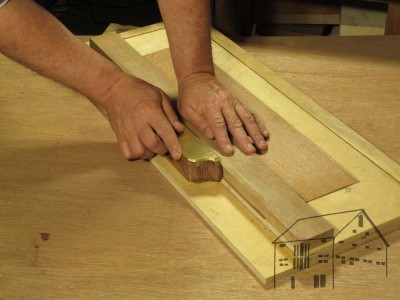
This workshop is limited to six students and will be three days long, July 18-20, 2014, with a registration of $375. A tool and supply list will be sent to all participants in advance of the event.
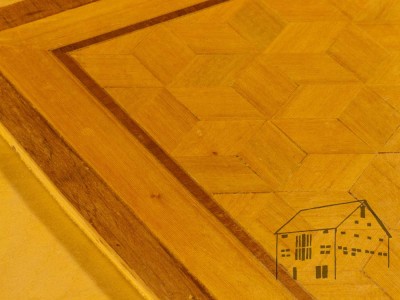
This is the “Week of the Bench” as I am joined at The Barn by old friend Dave Reeves and newer friend Jason Weaver, who is the webmeister of this site. When I asked Jason to design and construct the site, one thing he asked for was to spend time at The Barn “learning stuff.” This is the first installment. Three guys trying to finish two benches in five days. hmmm.
I’ve been assembling a nice inventory of large-ish hunks of lumber, and a stack of vintage (salvaged around 1950?) 12-foot long 5×12 Douglas Fir beams struck me as a nice starting point for a Roubo bench, and Jason agreed. The end result will be (we hope) a ~8-foot Roubo bench with a pair of Benchcrafted vises.
Dave had somewhat different bench needs, as a successful furniture restorer he did not need a massive behemoth like a Roubo, so he is making a lighter weight version of the same concept. He arrived with a pair of 3-1/2″ hackberry (!) slabs and a bunch of other timbers to make his bench. His only vise will be a leg vise with an Erie Toolworks screw.
I promised a fairly vigorous if not brutal pace of work as we all worked side-by -side, and thus far we have kept to that promise.
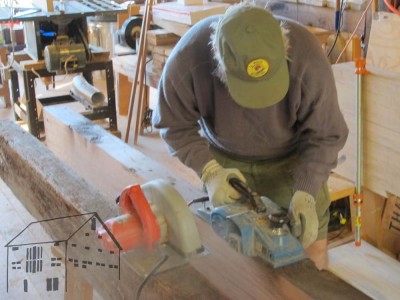
We began Monday evening by running all the slabs through my friend Tony’s giant planer, and Tuesday morning we set to getting them glued up.

My Ryobi 6-inch timber framer’s portable joiner was conscripted for the task, along with a scrub plane, and #5 set up as a fore plane, and a #8.
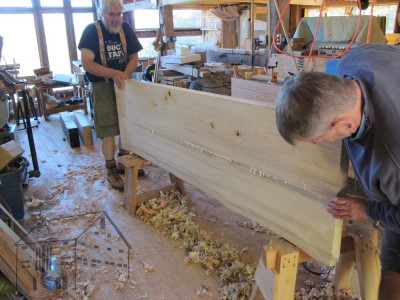
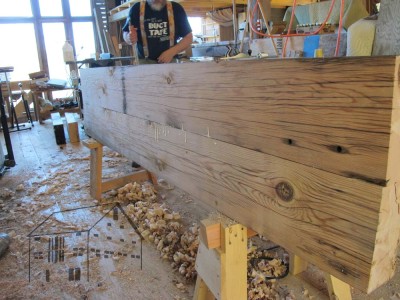
By noon we had them glued up and set aside, with leg stock prep on tap for the afternoon.

The afternoon was all about getting leg stock flat, square, and true. Both guys made progress, with the goal for today being the readiness of all the leg stock and a good start on flattening the glued up slabs. While our choreography was a bit off in the steps, we done good.
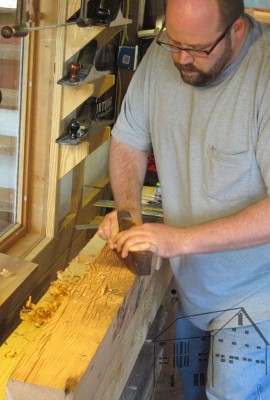
By the time we stopped for dinner both tops were flat, and legs were coming together nicely.
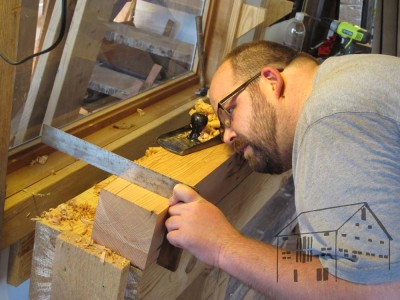

Again, the typical progression was from a coffin plane set up as a scrub plane, a #5 used as a fore plane, and a #8 jointer to finish things off.
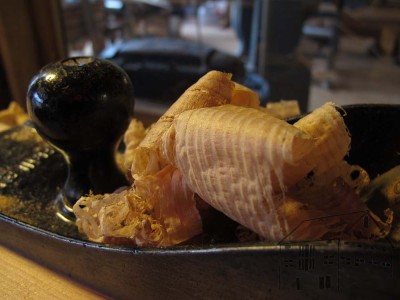
This is pretty much what you want to see coming off the blade when trueing up.
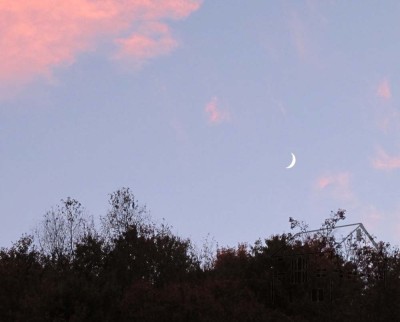
As we finished last night the sky was ablaze with an azure and fluorescent pink composition with a crescent sliver of white highlight.
Today was all about keeping things moving forward, fast. To help with the cleanup problem we hauled the bench tops outside to keep the mess out there.
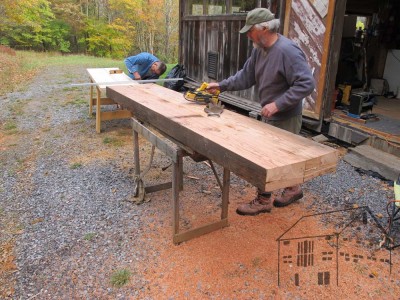
Both ends of the tool spectrum, with me using my power planer to hog off a lot of stock in a hurry, with Dave in the background using a horned wooden plane set up as a shallow-cut fore plane.
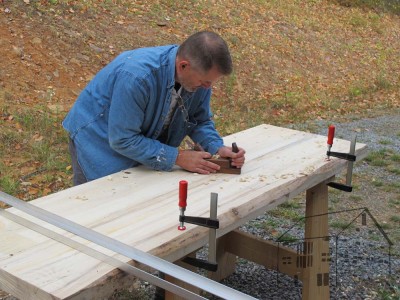
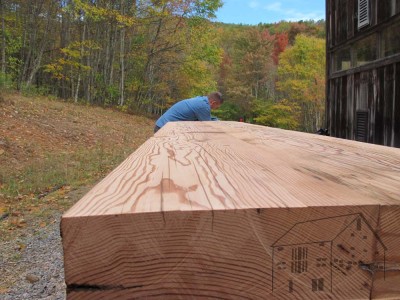
The slabs of Douglas Fir are going to make a spectacular bench. I will probably be using it at WIA next week.
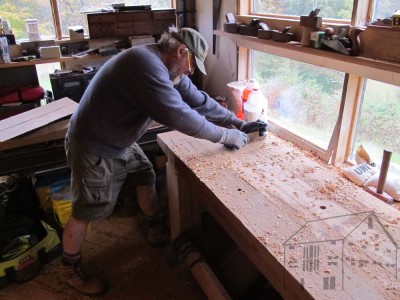
While both guys were busy, I snatched some time to finally flatten my very first Roubo bench from several years ago. I will add a crozet and some dog holes on the left leg.


Dave trued his legs and cut the double tenons (and learned about – and learned to love – holdfasts in the process), and Jason should have his four legs ready tomorrow.
Again tonight there should be no insomnia in the ranks, as we are finding consciousness leaving the grounds fairly early, and arriving late. Aching joints and groaning muscles are the hallmark of the morning, but once we get going we seem to be almost ambulatory.
More later.
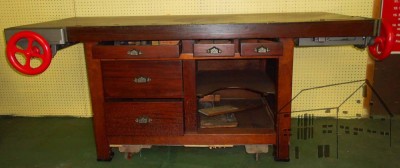
The first stop on my grand tour of New England was in southern Rhode Island, where AlanJ was patiently restoring a recently acquired piano-maker’s bench with two similar vises, one configured for the face position on the bench, the other for use as an end vise. I first became aware of this bench many months ago when a friend notified me of its presence on Ebay (this photo of the bench with red-handled vises was from the original listing). Jameel Abraham and I discussed at length the possibility of purchasing this bench, but in the end we dithered long enough for Alan to purchase it before we could make up our minds.
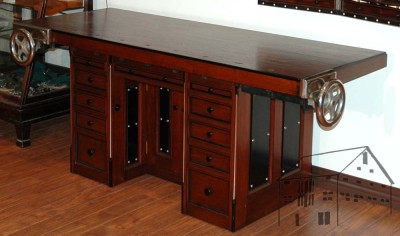
Alan’s new (to him) bench has an iron clad provenance, purchased from the descendents of a known piano maker and a documented home base of the Emerson Piano Company of Boston, along with some notable similarities to Henry Studley’s workbench (pictured here).
He has even begun to compile historical research about the piano maker, which warms my heart. After my tracking him down, Alan has been nothing but generous with images and background information. With his invitation in hand I headed north from The Peoples’ Republic of Maryland with Rhode Island as the home to the first of a half dozen vises I would study on this trip.

The bench itself was so similar to Henry Studley’s workbench that it is nearly inconceivable to me that the makers of these two benches were not working from the same playbook. The top of Alan’s bench is a surface of two magnificent planks of Cuban Mahogany — hard, dense, and beautifully figured. These 5/4 planks are laminated onto a 3” core of white oak. Altogether they weigh about three hundred pounds. Add the two 80-pound vises and you are up to almost 450 pounds. Studley’s bench is made of solid Cuban mahogany, but glued up from five slabs. The edges and corners of this bench are an ebonized oak strips about ½” square, while Studley used actual ebony.
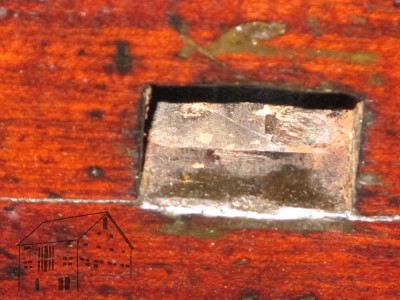
The dog holes on Alan’s bench are actually mortises chopped directly through the entire slab, while Studley’s are blocks in a glued construction method.
The vises of this bench were of the correct form and general configuration; a unified casting of the face jaw and the sliding platform “way,” a generous 9-1/4” wheel handle driving a twin-lead 1-1/8’ x 3 tpi Acme screw for fast, smooth action with a robust clamping when engaged. The face vise opens about 16”, which is emerging as a standard dimension for these vises.
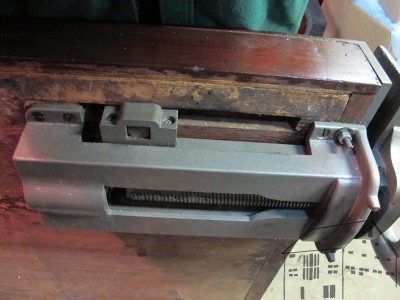
The tail vise has a collar affixed to the sliding “drawer” which allows for a dog to project up through the top.
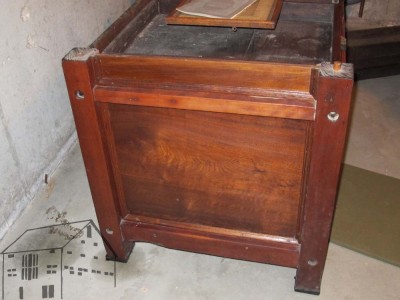
The base is similar in concept to the base that came on a bench I bought last summer in that it is clearly a “knock-down” cabinet that was ordered from a commercial vendor (note the four connecting bolt), and the top was made to fit this base. Studley’s base was long lost, and the current owner of the Studley bench fabricated a new one based on the shadows on the underside of the bench top and the aesthetic details of the tool cabinet.
All in all a magnificent start to the trip, and I look forward to Alan’s reports of his ongoing restoration of the bench and vises, which now have a pewter-ish appearance. I hope to get back to re-visit the restored bench next fall.
Thanks Alan!

I am not sure if two events establish a tradition, but I am hoping that is the case. For the second year in a row I set aside a weekend in May to host one of the local Chapters of the SAPFM with whom I am involved to gather at The Barn for a weekend of fellowship and woodfinishing.
The first weekend of May 2013 The Barn hosted a “Finisher’s Retreat Weekend” for the Chesapeake Chapter of the Society of American Period Furniture Makers. I co-taught the event with old friend DaveR from Knoxville. The premise for the weekend was for each participant to bring a completed furniture making project and we would finish it together. Together Dave and I led them through the Six Steps for Perfect Finishing, beginning with preparing the surface of the workpiece and wrapping up with a glorious artifact portrait of their piece on top of Franklin Floor.
Since the task for each participant was to arrive with a recently constructed piece awaiting the final, transformative finishing processes, the range of projects was broad and the quality of workmanship exceedingly impressive. Between my ministrations on surface prepping, wax finishing and brushing shellac, and Dave’s instructions and demonstrations with spirit varnish pad polishing and traditional asphalt coloration, and the continuous cross pollination, great progress was made on each project.
I look forward to May 16-18, 2014, where we can perhaps cement the new tradition for SAPFM members to come finish the pieces they built over the winter.
Recent Comments