Day 4 of FORP III was another one of feverish work as the participants were striving to start putting their benches together. Which meant, of course, the final fitting of all the joinery.

One image that was prevalent during the day was sharpening tools to get the joints as crisp as possible; numerous sharpening stations sprouted around the room.

Another snapshot that amused me was this tray of analgesics that was emptied at some point in the day. This was hard physical work, the kind few of us were used to at this level of intensity.


The buzz of activity was the air that we breathed throughout the day.


One of the benches I followed ws the one being built by this father-and-son team, whose tool kit had not arrived for reasons I never quite knew. Nevertheless, I was pleased to make my own kit available to them and they put it to good and successful use.






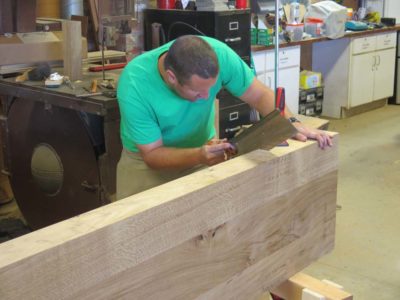




Meanwhile around the room twenty tales were unfolding and moving towards completion.

This is one of my favorite pictures from the week, with Will providing some useful ballast to Horace’s bench.

Jameel and Jeff provided the real-time, real-space tutorial on installing the Benchcrafted criss-cross leg vise that was part of the package of every bench.




Tim the mechanic was the first guy across the finish line, and hearty congratulations abounded.


John and Phil were next to finish, and I think this will be a treasured family memory for generations yet to come. The excitement was rising for another half-dozen benches ready to assemble Friday morning.

That evening was the open house with a cajun stew for supper, and my Gragg chair on display or anyone who wanted to give it a try.
Day 3 of FORP is pretty much an extended schizophrenic moment as the participants are settling into the routine of work and fellowship, knowing what and why they are doing what they are doing. The morning generally starts out smoothly with restrained purposefulness but as the day goes on there is a palpable edge to the atmosphere as the sentiment, “Oh crap, I’ve only got two more days to get this done,” wafts into the shop.
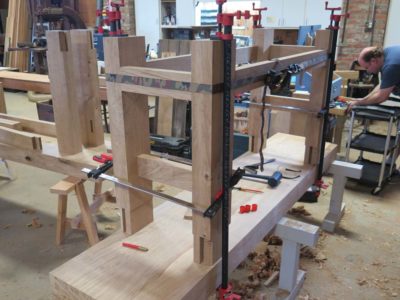
Wednesday was Mortise Day and the intensity was thick. At the beginning of the day everyone was first wrapping up their base assemblies so they would know where to put the mortises.

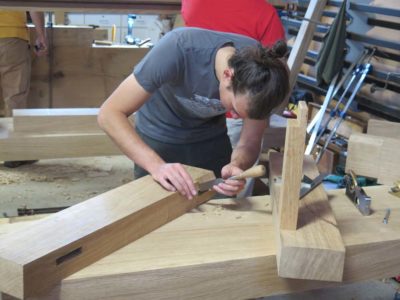
There was a fair bit of tenon trimming also, especially for the dovetailed tenon cheeks.
Oh, and lots of checking to make sure “square” was really square.

Around mid-morning Chris gave the sermon on executing the double tenons. There were two major steps and some folks did one first (sawing the outer dovetailed tenon) and other went the other way (drilling out the waste for the inner tenons).
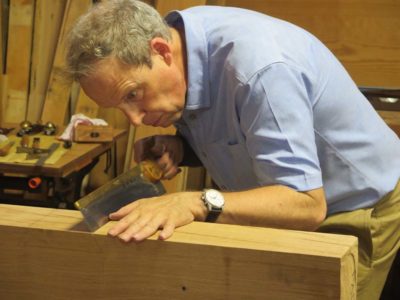
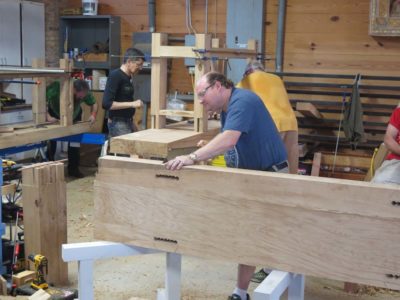
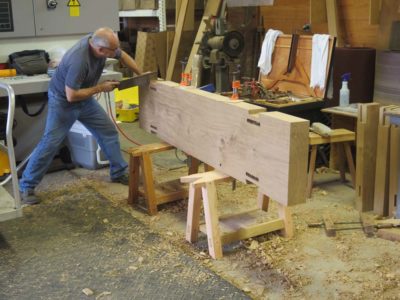
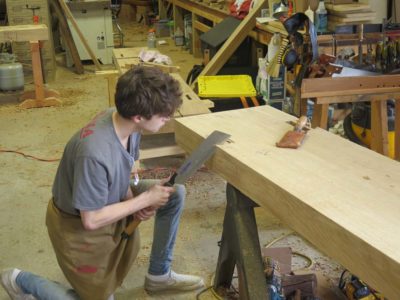

There was a lot of deep breathing as this was the start of irreversible steps. For the most part everyone had on their game faces for sawing the dovetail shoulders. Except for Brian #4 who was never more than a moment away from a hearty laugh. I think the class had something like five Brians, four Andrews, and three Tims.
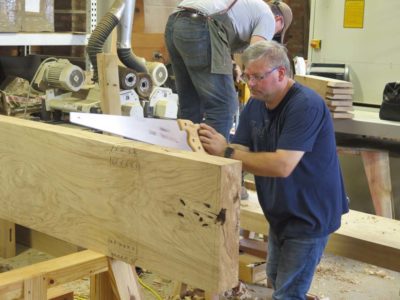


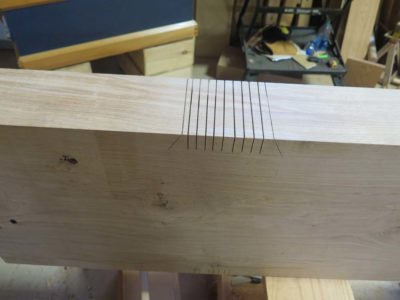

Once the angled cheeks were cut the waste was kerfed to facilitate removal.
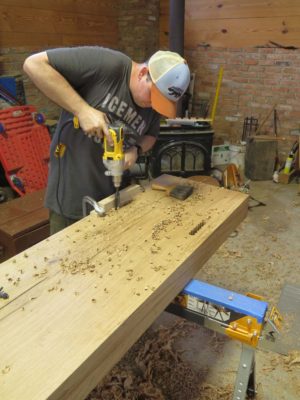


For the inner mortises the waste was drilled out and for many the edges of the joint were established with a saber saw, a technique I have never employed.



Then the chopping began in earnest.
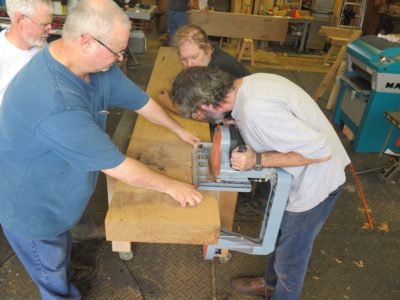
Somewhere along the line Schwarz encountered this beast of a hand-held bandsaw, using it to trim the ends of the slabs and kerf the outer mortises.
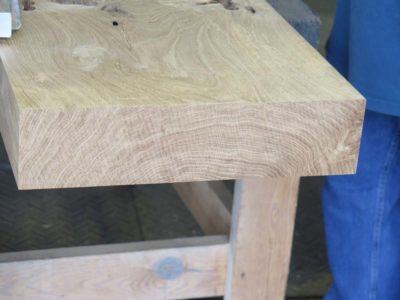
I included this picture just because the wood was so remarkable.

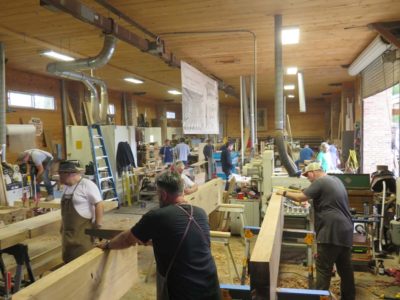
Yes indeed, the joint was jumpin’ this day.

Tuesday morning saw me working with Jeff Miller in the lower shop building because the Tannewitz band saw there was better suited for finishing up the tenon cheeks and the dovetailed shoulders on the front tenons. Though there are no pictures of us doing that I did get a pretty neat pic of Bo’s crew distressing some sweet oak box beams for a custom interior someplace.
Jeff had an appointment elsewhere for a few hours so I was working with Jameel to get all the tenon cuts finished, and we did.
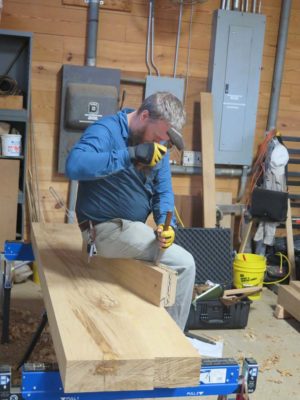
I got back up to the main work room just before lunch and there was a flurry of activity and the bench parts began to come together. Lots of tenon valley cleaning out,

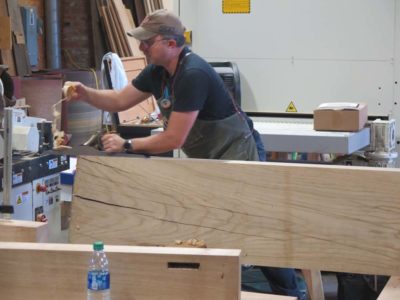
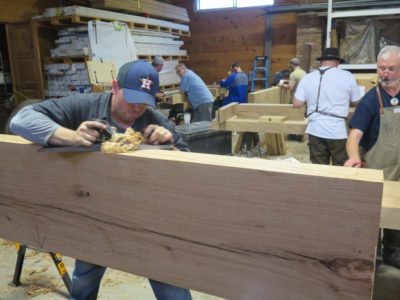
edges being trued to make sure the layouts of the mortises were correct, (the long curls were ankle deep that afternoon),

the dovetail cheeks were cross-cut and trued



and a whole lotta stretcher mortises were matched with their mortises.
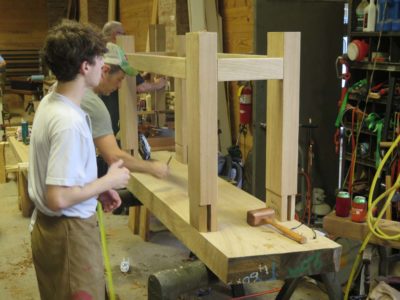

Before long there was a collection of upside-down bench bases on display.

Around mid-afternoon The Schwarz gave a demo on laying out the base to the top and marking and cutting the mortises into the latter.

So that’s what was happening all over the place for the rest of the day.
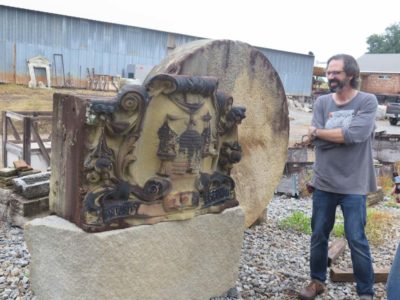
The day was capped by another walk through the yard full of antiquities, with Chris being captivated by this sculpted sandstone bank faced detail of a bee hive.
I thought I had been told to arrive at 9 the first morning, so I did, only to find out that the first students arrived before 7AM to stake out their work stations and set up, so the bee hive was buzzing long before I got there.
As I came to learn throughout the week the students body was an amazing mix of folks; a chemical engineering professor, a video production entrepreneur, a lawyer/lobbyist, three professional woodworkers/furniture makers, a cybersecurity geek, a geophysicist, a playwright, a CPA, a custom floor maker and his furniture design student son, a fireman, a mechanic, an energy engineer, an electrician, a high-end custom home builder, a rancher, two surgeons, a military helicopter pilot, and maybe another couple of folks I cannot remember at the moment. There was no shortage of interesting things to talk about during meals and breaks.
Frankly put, the gallery of student set-ups was a dizzying cornucopia of horses and tool inventories, with the former ranging from old-school carpenter’s horses to sooper high tech devices the likes of which I had never seen.
Take a look.
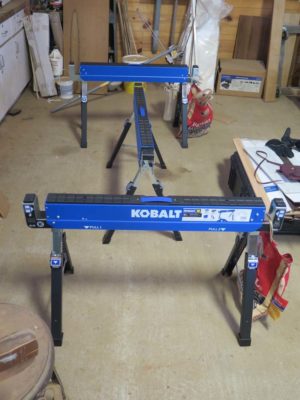

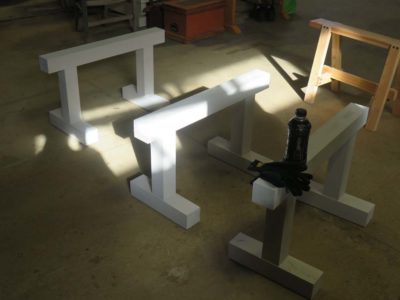
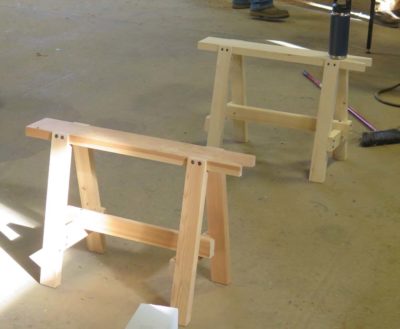





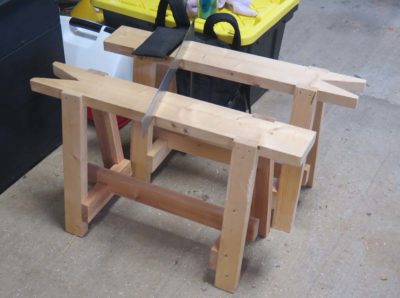


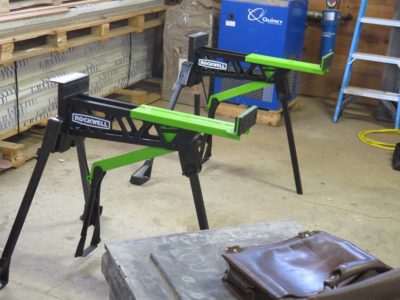



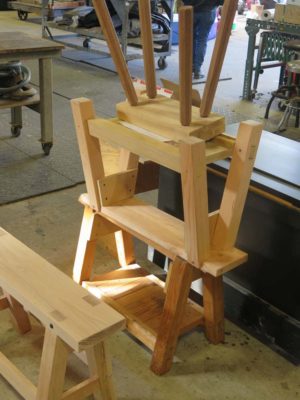

As for tool inventories and their containers they ranged from several ATCs and Dutch cabinets to plastic tubs to simple canvas bags. I’ll take a look at them in another post.
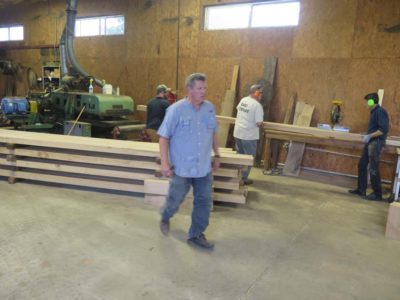

As I arrived the last of the bench tops were being fed through the Stratoplaner, the prehistoric minivan-sized machine that planed all four surface of the 300-pound slabs simultaneously. One by one these took their places in the appropriate work stations.
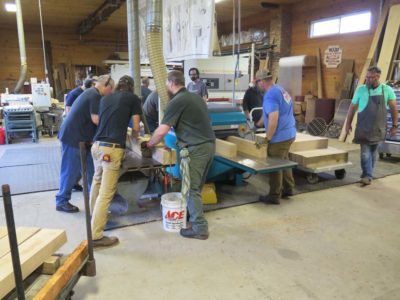
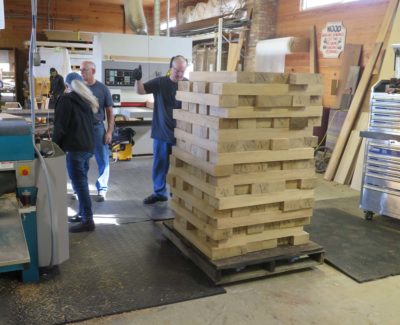
In short order the preparations for the 80 legs commenced.
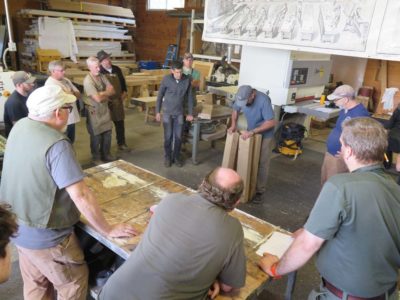




A quick tutorial on laying out the double tenons on the tops of the legs (and keeping track of them!) was followed by the soundlessness of eighty sets of tenons being laid out.

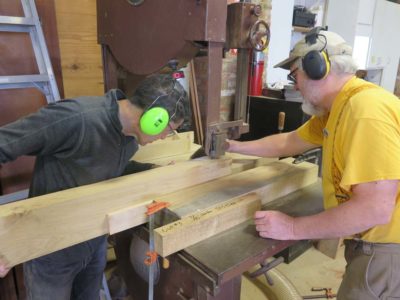
While that was underway Will Myers and Father John Abraham prepped the stretcher stock, and once again Jeff Miller and I tag-teamed to make jigs for cutting the tenon shoulders. Which we did. A lot.


As the day closed the air was filled with the sounds of wailing away on the valleys between the double tenons and the scriiitch of planing the edges of the tops square and true so the double mortise layout could be executed.
And that was Day 1.
We recently convened the third iteration of the French Oak Roubo Project in Barnesville, Georgia, chronicled at some length by the Brothers Abraham. It was even more frenetic than in the past as there were several more benches being built (21) and fewer instructing enthusiasts, so we were all a-hopping.
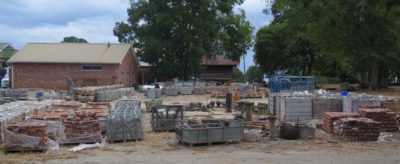
Once again our incredibly generous host was Bo Childs, a renowned importer of French architectural antiquities and manufacturer of uber-elite interiors in the style of the ancients. The setting is intoxicating with artifacts hundreds of years old scattered around the lot.
I arrived on Saturday night in order to put in a solid day of work preparing on Sunday. (Driving straight through downtown Atlanta at 8PM after dinner with dear friends was a real treat, at one point there were 16 lanes of traffic, none of them moving.) None of us like working on Sundays, preferring it to be a day of fellowship, meditation, and rest, but some times reality intrudes.


The Abrahams had already begun the stock preps several days earlier with Bo on the bandsaw (he is an artist with that thing) and those benches that needed gluing up were mostly already done.
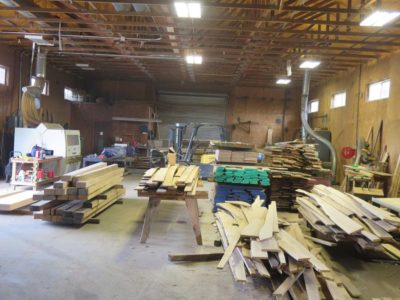
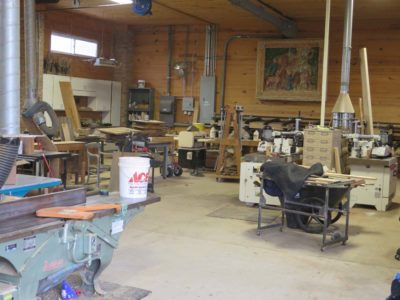
As the final bit of sawmilling and gluing-up was completed, the undeniable reality was that our work spaces for the coming week serve as a functioning commercial millwork shop the rest of the time and these spaces needed to have some discipline imposed on them.

Slowly the students began to trickle in and the piles of 5-1/2″ thick white oak slabs grew.
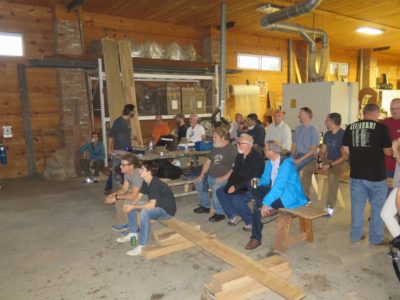
The festivities began at 6PM with a barbeque, and the The Schwarz took the stage to introduce the program of the week.
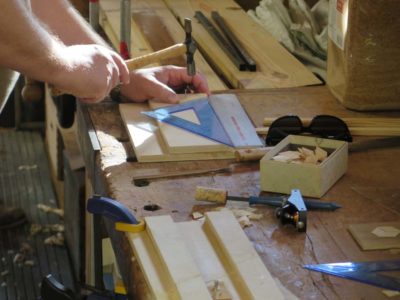
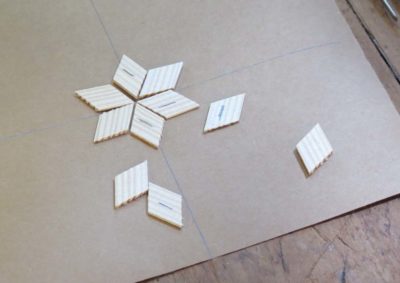
Given the prominence of 60-degree angles in the worlds of parquetry and Roubo benches, during the “Making Roubo Squares” workshop earlier this summer I made a couple of 30-60-90 brass triangles, as did the participants after I demonstrated the lesson they learned in seventh grade Geometry class: the hypotenuse is exactly twice the length of the base of this right triangle.

I finally got my first one ready for battle, albeit without the decorative flourishes I had been wanting. I simply did not have the time at present but car return to add them when I do get the time.
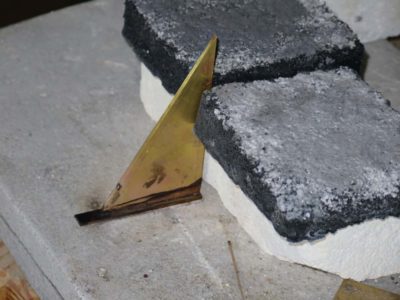

I soldered on the lip for the base, then just cleaned up all the edges and surface and it was ready for action.

Get to work, you triangle you!
Recently I was contacted by my friend Justin, who was coming to town to visit his folks. Justin is an enthusiastic and knowledgeable tools collector and broker, and was offering me a piano makers’ vise he had found (actually he has now acquired almost a dozen of them). We spoke on the phone and he sent some pictures and I asked him to bring the best of the lot, which he did.

I bought it, Of course I did. It was practically a moral imperative. It will replace the Sheldon vise on the end of my Studley-replica bench top ASAP. Or, it might go as a face vise on the Sheldon end, diagonal to the existing vise essentially turning this into a partner’s bench.
Stay tuned.

One of the fixtures integral to my ongoing work on building Gragg chairs is this shaving beam I made when embarking down Gragg Boulevard several years ago.
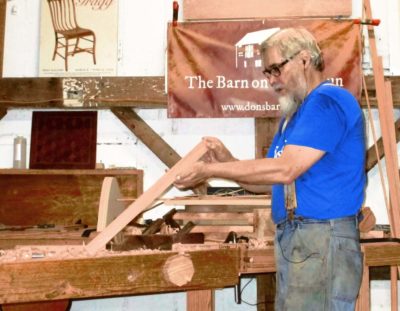
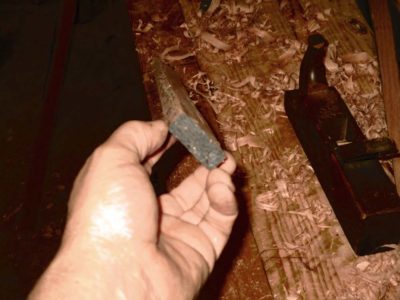
When I am in the heat of battle I need to move back and forth frequently while preparing the stock for the chairs prior to steam bending the elements, checking then by eye and small sizing jig I keep in my pocket or right there on the bench. I found it to be tiresome, and frankly after a while painful, to get up and down from my shaving horse dozens of times a day. Instead I designed and built this fixture that allows me to work on my feet with much less stress to my creaky hips.
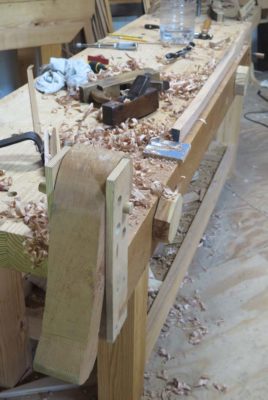
The core of the device is a hunk of 4″ x 6″ Douglas fir from the scrap pile. To that I built a cam clamp head that can grab and hold pieces of split oak (what I normally work with) so that I can shave it close to the final dimension with typical drawknives and spokeshaves, working at waist height while standing.

An additional feature at the other end is a tiny woodscrew clamp with one jaw permanently screwed to the end of the beam. This makes it possible for me to work in both the pulling and pushing directions on the same device. It is nearly effortless to go from pulling a drawknife on a workpiece to switching to pushing either spokeshaves or hand planes getting the piece ready for the steam box.


A series of holes for stops helps hold the workpieces in place while I am yanking on them in one direction of the other.

The entire device is bolted to the rear side of the Roubo workbench I keep up in the video studio on the fourth floor. I drilled 1-1/2″ holes through the beam, then horizontal 1-3/8″ holes in the corresponding location on the edge of the workbench slab. I tapped out the holes in the workbench slab and use threaded Moxon screws through the shaving beam to affix it in place. It can be removed quickly and easily.



Like I said, this device has become an integral part of making Gragg chairs AND imparting greater speed and comfort to that process. It may not be an overstatement to suggest that this bench accessory has become so important that my passion to continue down the road of making and revising Gragg would be substantially diminished without it.
Once while being visited by an acquaintance who volunteers at a wounded vet rehab facility he noticed that this shaving beam could be made entirely accessible to people in wheel chairs by simply setting it up between trestles rather than attached to the side of a fixed work bench.
Last time I heard from him he was making some for the shop of the rehab facility, and that pleased me even more as it could be one component of regaining healing and wholeness for vets who had sacrificed so much on my behalf.
Recently while noodling with one of my ripple molding cutters in preparation for the September “Make A Ripple Molding Cutter” class, which like the upcoming “Make A Roubo Shoulder Knife” has been cancelled due to unanimous disinterest (I will soon write about the future of workshops at the barn, most of which have drawn nearly unanimous disinterest and will likely diminish for the most part), I decided that the underlying design concept for that particular machine was too flawed to rescue. So, I tossed in the towel on that particular journey.

At the same time I was doing some cleanup and organizing on the main floor of the barn — alas when you have thousands of square feet of space the tidying is nearly an endless proposition — I decided to address the “problem” of how my lathe has been set up for the past few years. At the time I thought I would really like having the lathe sitting on a mondo beam adjacent to two of the vertical timbers holding up the third and fourth floors. In practice I realized that I REALLY did not like that set-up. What to do?

Well, with the ripple molding cutter being moth-balled I suddenly had the perfect base available for use with the lathe. So now it sits thereon, and I like the new set-up much, much better. An additional benefit is that the new base is long enough to hold not only my wood lathe but also my micro machinist lathe.
Excellent.
And fear not about the fate of the mondo beam. It now serves as part of a bench outside being used in my ongoing tactical training and practice.
Returning unapologetic after a week of spending time with the family, and even missing the ostensible subject by one day, let me spend a few minutes looking forward in the context of Workbench Wednesday. As we last left the subject I posted a gallery of past and current inventory of workbenches either in the Barn or made by me in the barn. But make no mistake, this does not end the string of workbenches by my hands. So here goes a glimpse of what the future might look like. There are many projects at various stages of development and planning extant.

Tim’s Bench
Next up on the workbench agenda is to make a massive 10-foot Nicholson-style gunsmith’s partner’s bench for my friend TimD. Tim is a gunsmith making superb late 18th century long rifles and often teaches workshops on the subject. For that reason Tim wanted a workbench that could suffice for both his own work but that of a student on the other side as well. As is often the case for me the starting point is select SYP from Virginia Frame in Fishersville VA. I’ll get this delivered to Tim sometime later in the summer, but first we have to line up two additional stout fellows at the finished bench will weigh in at just under 450 pounds.
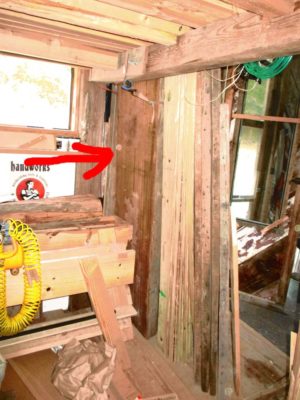
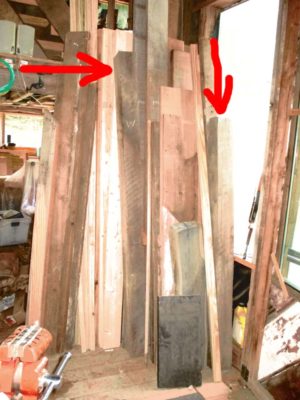
The Mahogany and Walnut Roubo
When I first encountered the H.O. Studley menagerie in person I was particularly struck by his workbench. While I could not imagine myself using his tool cabinet as a routine matter, I definitely saw the workbench as a valued addition to my work space. Then, when the famed lumber store in the Cincinnati area closed I asked Chris Schwarz to get me a slab of mahogany from which I could make such a bench. He acquired a sweet 7-1/2′ x 24″ x 4″ slab. Subsequent visits and close inspection of Studley’s bench revealed it was not a mahogany slab but rather a laminated top with oak cores and mahogany faces. I set the mahogany slab aside and now know that I will turn it into the over-the-top Roubo bench it was evidently destined to become. In addition to the magnificent mahogany slab I have the necessary 6″ x 8″ vintage black walnut stock to make the legs. This should be a real eye catcher when finished.
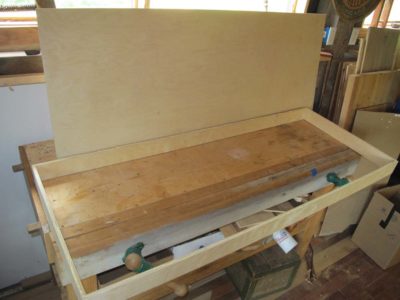
The Ultimate On-Site Restoration Bench
This knock-down lightweight bench is the third generation of the concept, and will include many new features but not sacrifice much of the lightness. I started this bench a few years ago and set it aside but hope to get back to it in the coming days. Stay tuned.
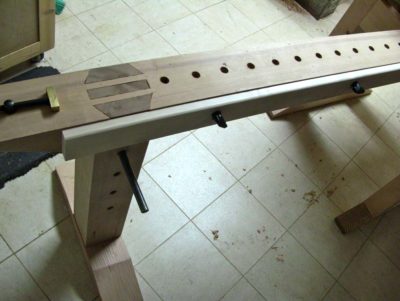

photos courtesy of Shannon Rogers
Replicating Shannon Rogers’ Joinery Bench(es)
The first time I saw Shannon Rogers’ two-part joinery bench with the tall, standing bench and its companion planning beam I offered the highest compliment I could: “Darn, I wish I had thought of that design for myself.” At this point of my working life I cannot say that I actually need it right now, but I can definitely see a time where a differing living situation might make this a perfect fit for me.
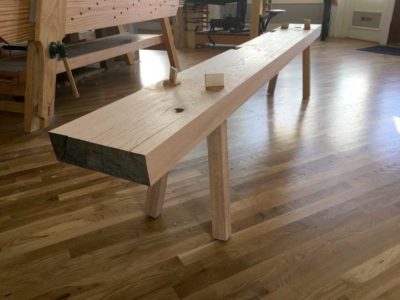
photo courtesy of Christopher Schwarz
The Roman Bench
Since Chris Schwarz made his research into this low slung bench, and viewing Jonathan Fisher’s iteration of it, I knew this bench was something I needed to build and have around. In great part this is because it might make great allowance for working while sitting down. Plus, since I also dabble in fiction writing I would like to incorporate the workbench into a series of short stories I am trying to sketch about the working life of Joshua Bar Joseph, a/k/a Jesus of Nazareth, prior to his assumption of His earthly ministry. Having this bench around to inspire me could, well, inspire me.

Curly Maple and Oak Roubo
Over the years I have compiled a substantial inventory of lumber including some pretty big stuff. Included in this is a slab of curly maple I have squirreled away, along with some fabulous 6×6 oak for the legs of a sweet Roubo. I have worked on the slab on-and-off for a few years, but perhaps this autumn is the time to bring this ting to the finish line.

photo courtesy of William Duffield
Replicating William’s Benchtop Auxiliary
Some time ago at an SAPFM regional chapter meeting my friend WilliamD showed his auxiliary bench-top-bench, a concept I first heard about from Steve Latta. The appeal of this appendage is pretty evident in that it reduces the amount of bending over that is required for detail work. At the moment I just use a nice piece of plywood sitting on a pair of shoji-work-style mini-horses.
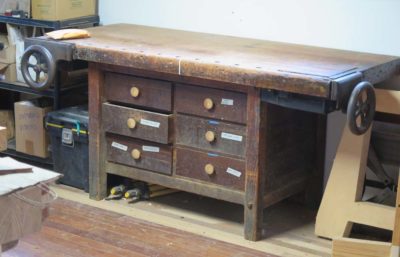
Restoring My Piano Maker’s Bench
This thing needs a thorough going over including adding a new layer of mahogany over the current top which would first be flattened. Oh, and the vises both need cleaning, polishing, and nickel plating.

Bob’s Slabs
My pal Bob got these 10″ x 15″ white oak timbers ( two are 10′, one is 8′) from his brother, who works for a hardwood saw mill, to chop up as firewood. Bob thought I might put them to better use as workbenches or something and I agree. When I look at this stack all I can see is a bunch of Roubo bench tops.

More Workbenches for A Possible Gragg Chair Workshop
Should I decide to offer a Gragg Chair Building Workshop, to which I am about 90% leaning, we will need another three or four workbenches up in the attic studio, the only place large enough to host such a class. If I do go in this direction these benches, almost certainly Nicholsons, would would be a winter time project at the end of this year.
That’s all I can think of for now. I might need to think about an annex for The Barn…
Recent Comments